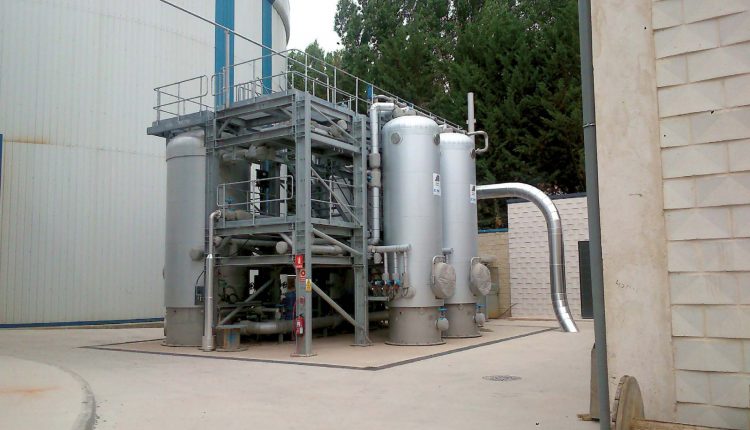
Evaluación del balance de masa y energía de una planta de pretratamiento de hidrólisis térmica de fangos Cambi en una EDAR
Mass and energy balance evaluation of a Cambi sludge thermal hydrolysis pretreatment plant in a WWTP
José García Cascallana
Resumen
Se requiere una gran cantidad de energía eléctrica para la depuración de las aguas residuales y un elevado coste económico asociado a dicha actividad. Una de las formas clásicas de reducir estos costes consiste en disminuir el consumo de energía eléctrica mediante el incremento de la eficiencia a lo largo de todo el proceso de depuración y otra es optimizar la generación de energía eléctrica y ajustar el autoconsumo de la planta en función del biogás producido en los digestores. Este artículo se ha basado en optimizar la producción de biogás y energía eléctrica y disminuir el fango deshidratado mediante la instalación de una planta de pretratamiento de hidrólisis térmica de fangos Cambi antes de los digestores. La metodología adoptada ha permitido realizar el cálculo de los equilibrios de masa y energía, tomando como punto de partida de diseño los fangos espesados primarios y secundarios calculados a partir de los datos registrados en la planta de tratamiento durante el período 2011-2016. El balance de masa y energía realizado ha permitido conocer el funcionamiento de los ciclos batch y medio de la planta en función de los diagramas obtenidos de temperatura, presión, concentración, inyección de vapor, etc., en cada uno de los tanques que conforman la planta.
Palabras clave: Deshidratación, gases de proceso, vapor flash, polielectrolito, expansión isentálpica.
Abstract
A large amount of electricity is needed for the treatment of wastewater and this activity entails a high economic cost. A classic way to reduce these costs is to decrease the consumption of electricity by increasing the efficiency throughout the whole treatment process. Another option is to optimize the generation of electrical energy from biogas produced by anaerobic digestion. This article optimizes the production of biogas and electrical energy along with the decrease of the amount of dewatering sludge by the implementation of a Cambi thermal hydrolysis pre-treatment plant before the digesters. The methodology adopted calculated mass and energy balances, using the production data of primary and secondary sludge registered in the treatment plant during the period 2011-2016. The mass and energy balances carried out have allowed for knowing the operation of the batch and average cycles of the plant based on the diagrams obtained of temperature, pressure, concentration, steam injection, etc., in each of the plant tanks.
Keywords: Dewatering, process gases, flash steam, polyelectrolyte, isenthalpic expansion.
José García Cascallana
Recibido / received: 27/04/2020. Aceptado / accepted: 29/03/2021. Ingeniero Técnico Industrial (Universidad de León), Ingeniero Industrial (UNED), Ingeniero Técnico de Minas (Universidad de León), Grado en Ingeniería de la Energía (Universidad de León), Máster en Tecnología Láser (Universidad Politécnica de Madrid) y Doctor por la Universidad de León. Ocupación actual: Ministerio de Trabajo y Economía Social. +
E-mail para correspondencia: jgc0504@yahoo.es.
Introducción
El aumento de los precios de la energía y la gran preocupación sobre el cambio climático global llevan a la necesidad de mejorar la independencia energética de las estaciones de tratamiento de aguas residuales (EDAR). Transportar y tratar las aguas residuales urbanas para cumplir con los estándares aceptables de calidad del agua requiere una cantidad sustancial de energía, principalmente energía eléctrica (Chae y Kang, 2013).
La digestión anaerobia mesofílica (DAM) se considera una parte importante y esencial de una EDAR moderna que transforma la materia orgánica del fango en biogás, reduciendo la cantidad de sólidos finales y destruyendo la mayoría de los patógenos presentes (Abelleira et al., 2012). La producción de fangos en las EDAR se está convirtiendo en un tema ambiental extremadamente importante (Abelleira et al., 2015). Los fangos producidos en EDAR municipales e industriales pueden llegar a contener componentes orgánicos y minerales como metales pesados y especies orgánicas refractarias, lo cual justificaría en algunos casos la consideración de los fangos como materiales peligrosos (Neyens y Baeyens, 2003).
El CH4 contenido en el biogás puede ser utilizado como fuente de energía renovable para la producción de energía, ya sea térmica o eléctrica o tratado hasta conseguir un incremento en la riqueza del mismo que permita su uso como combustible para vehículos (Zhang et al., 2014). La estabilización de fangos mediante DAM permite reducir los costes de transporte y disminuye, de esta forma, las emisiones de gases de efecto invernadero. Algunos otros beneficios ambientales de la DAM incluyen la reducción del olor, el control de patógenos y la conservación de nutrientes (Peña y Steinmetz, 2012).
Para mejorar el rendimiento de la DAM, incluyendo la elevada producción específica de biogás, el enfoque más lógico es la disrupción de las paredes de las células microbianas del fango y permitir la liberación de los sustratos degradables fuera de sus células para ser más accesible a los mecanismos extracelulares en la etapa de hidrólisis. Se han desarrollado tecnologías que consiguen un rendimiento en la DAM del fango potencialmente mayor gracias a la desintegración de los fangos antes de la DAM con el objetivo de acelerar la etapa de hidrólisis: son los llamados pretratamientos (Phothilangka, 2008). Hay una serie de pretratamientos, principalmente ozonización, ultrasonidos, microondas, térmicos y mecánicos, pero de todos ellos, el térmico es el más utilizado actualmente.
La etapa de hidrólisis incluye la degradación de las macromoléculas insolubles en compuestos solubles, poniéndolos a disposición de los microorganismos implicados en la DAM. La hidrólisis térmica (HT) se ha estudiado en el rango de temperaturas de 60-270 ºC. Los procesos de HT pueden clasificarse en dos grupos: a) pretratamiento por debajo de 100 ºC, que se considera un pretratamiento a baja temperatura y b) pretratamiento por encima de 100 ºC a elevada temperatura y bajo presión, el cual se conoce como HT a alta presión. Se ha descubierto que el pretratamiento a baja temperatura incrementa la solubilización del fango con menos energía que el de alta temperatura, pero no mejora la digestión del fango. La producción de biogás no aumenta con temperaturas comprendidas entre 60 y 90 ºC, mientras que el pretratamiento a temperaturas más elevadas en el intervalo de 140-160 ºC ha permitido una reducción del tiempo de reducción hidráulica para la digestión desde 18-20 días a 12-14 días y un aumento en la producción de biogás. Por tanto, el pretratamiento a alta temperatura es más eficaz. La HT genera productos no biodegradables más allá de cierta temperatura dependiendo de las características del fango bruto. En el pretratamiento a alta temperatura se ha encontrado que las temperaturas por encima de 200 ºC desencadenan reacciones de Maillard que producen melanoidinas, polímeros heterogéneos de alto peso molecular. Las melanoidinas son difíciles de degradar y pueden obstaculizar la degradación de otras sustancias orgánicas (Sarwar, 2015).
Los efectos combinados de la temperatura, la presión y la despresurización súbita se traducen en un aumento significativo de la solubilización y en la reducción del tamaño de partícula en el fango hidrolizado. La explosión de vapor fue introducida y patentada como un proceso de pretratamiento de biomasa en 1926 por Mason WH (Stelte, 2013). Mediante la realización de una expansión isentálpica del fango entre el reactor y el flash-tank se consigue la destrucción de las macroestructuras celulares presentes y la disrupción celular. Esto produce una explosión de vapor, desintegración celular, una gran disminución de la viscosidad y destrucción de las estructuras macromoleculares (Kleivena et al., 2007). Otros autores indican que la temperatura ha demostrado ser el parámetro más influyente, mientras que los cambios en la presión no producen modificaciones significativas en las características del fango (Urrea et al., 2015).
Adicionalmente, el proceso de HT a menudo se asocia con problemas de acumulación de NH3 en los digestores que causan inhibición de la actividad metanogénica. La amonificación de las proteínas por la HT puede ser una consideración importante. La producción de NH3 podría reducirse marginalmente al operar con un proceso de pretratamiento de HT a 150 ºC (Wilson y Novak, 2009). Aunque el NH3 es un nutriente esencial para el crecimiento bacteriano, puede inhibir la metanogénesis si está en concentraciones elevadas (Yenigun y Demirel, 2013).
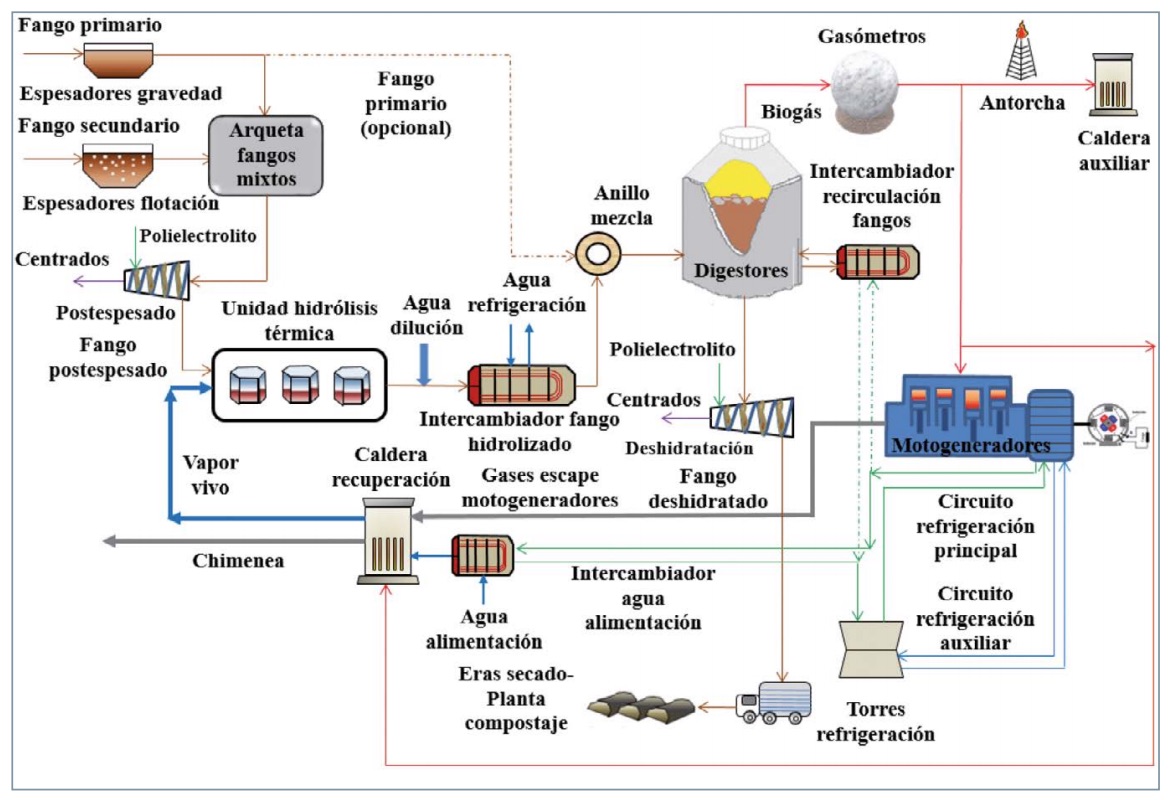
Sin embargo, una ventaja importante es la reducción del contenido de agua de los fangos usualmente por deshidratación mecánica, que es crucial para reducir los costes producidos en su manejo posterior (Fenga et al., 2014). Las proteínas presentes en el fango se caracterizan por tener una elevada capacidad para retener agua. Dado que en el proceso de HT, las proteínas se desnaturalizan, se destruye dicha capacidad de retención de agua (Kleivenb et al., 2007) y entonces se pueden conseguir unos valores mucho más altos en la concentración del fango deshidratado. La reducción del contenido de agua de los fangos usualmente por deshidratación mecánica es crucial para reducir los costes del manejo de fangos (Fengb et al., 2014).
El sujeto de análisis ha sido la EDAR de Burgos, equipada con un proceso de pretratamiento con HT convencional de tecnología Cambi tipo batch y el objeto ha sido obtener el balance de masa y energía de esta planta en el punto de diseño establecido. La planta de HT trata de incrementar la producción de biogás y energía eléctrica y, además, disminuir la cantidad de fango deshidratado.
Materiales y métodos
Descripción de la EDAR
Esta planta tiene la función básica de recoger las aguas residuales domésticas de las poblaciones circundantes y las industriales, reducir su contaminación aplicándoles un pretratamiento, tratamiento primario (decantadores primarios), secundario (reactores biológicos y decantadores secundarios) y terciario (decantadores lamelares, ozono y rayos ultravioleta) y devolver las aguas residuales purificadas al río Arlanzón con unos parámetros de vertido dentro de los valores reglamentarios. La capacidad de tratamiento de aguas residuales es de 156.504 m3 /día para servir a un total de 1.056.692 habitantes equivalentes (h.e.) (EDARa , 2020).
La figura 1 representa el diagrama general de proceso de la EDAR con HT convencional. En él se puede apreciar la inserción de la planta de HT entre postespesado y digestores a fin de realizar el pretratamiento térmico al fango. También existe la posibilidad de hidrolizar solamente el fango secundario. Esta posibilidad está representada en el diagrama anterior mediante una línea discontinua que indica fango primario (opcional).
Descripción del escenario
La tabla 1 muestra los valores del fango espesado obtenidos a la salida de los espesadores de gravedad y flotación de la EDAR durante los años 2011-2016 y que han constituido los datos de partida; se han denominado “punto de diseño”.
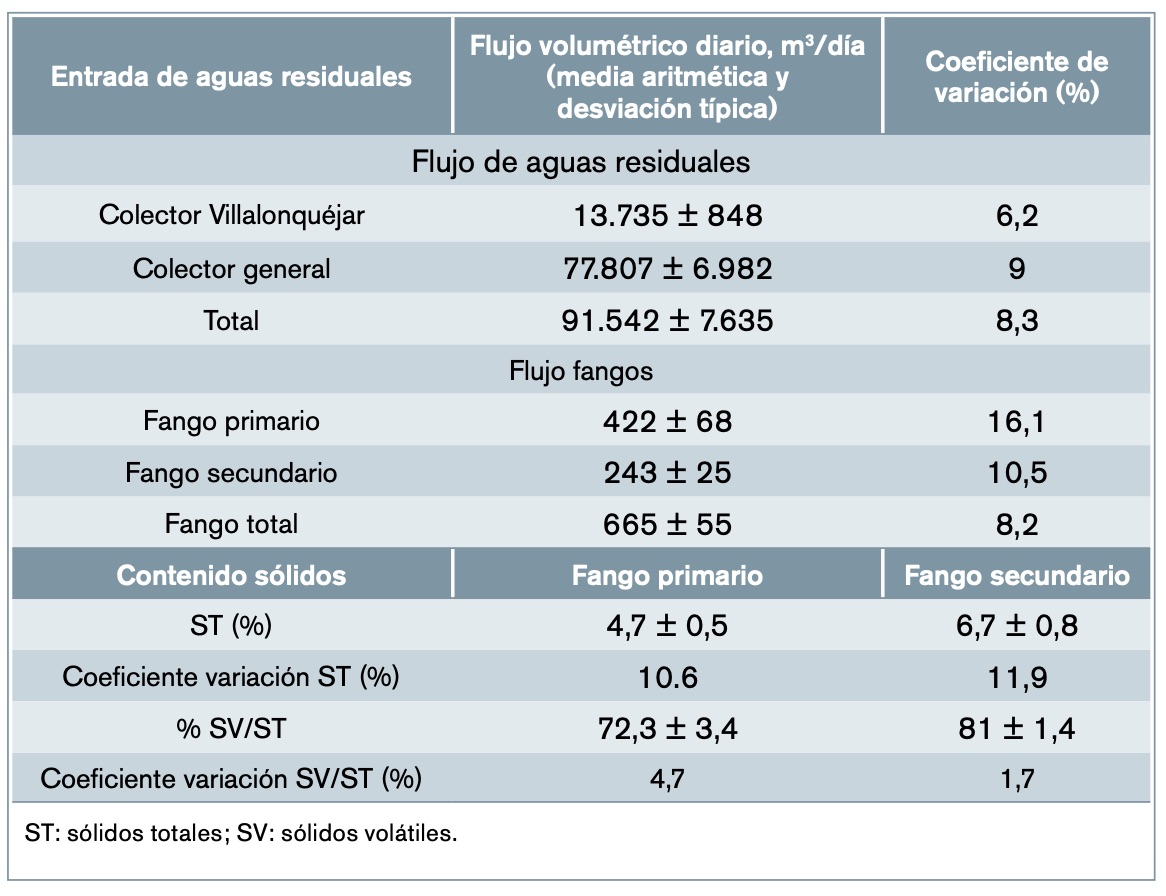
La planta de HT instalada en la EDAR de Burgos tiene la función de elevar la temperatura del fango, mantenerla durante un tiempo determinado en los reactores y llevar a cabo una despresurización súbita al flash-tank con objeto de realizar la HT. La tabla 2 indica las especificaciones de carácter general del proceso de HT Cambi.
La planta de HT es una planta denominada THP-B6.2, tipo batch o lotes, suministrada por la empresa noruega Cambi, con una capacidad nominal de tratamiento de 35 t ST/día (12.775 t ST/año), pero que puede admitir el 20% más de capacidad hasta un máximo de 42 t ST/día (15.330 t ST/año) (Kleiven, 2014; EDARb , 2020). Si la capacidad necesaria de tratamiento de la planta superara en algún momento las 42 t ST/hora, operaría al máximo de su capacidad con fango primario-secundario y el resto de primario se enviaría directamente a los digestores sin hidrolizar. La tabla 3 muestra los parámetros de diseño más importantes de la planta y sus referencias.
Se define el ciclo batch como el realmente ejecutado por la planta THP-B6.2. La entrada de fango al pulper y salida del flash-tank operan de forma continua, mientras que los reactores lo hacen de forma batch. Por otro lado, el ciclo medio es un ciclo ficticio que consiste en ponderar los parámetros batch a todo lo largo del ciclo completo del reactor.
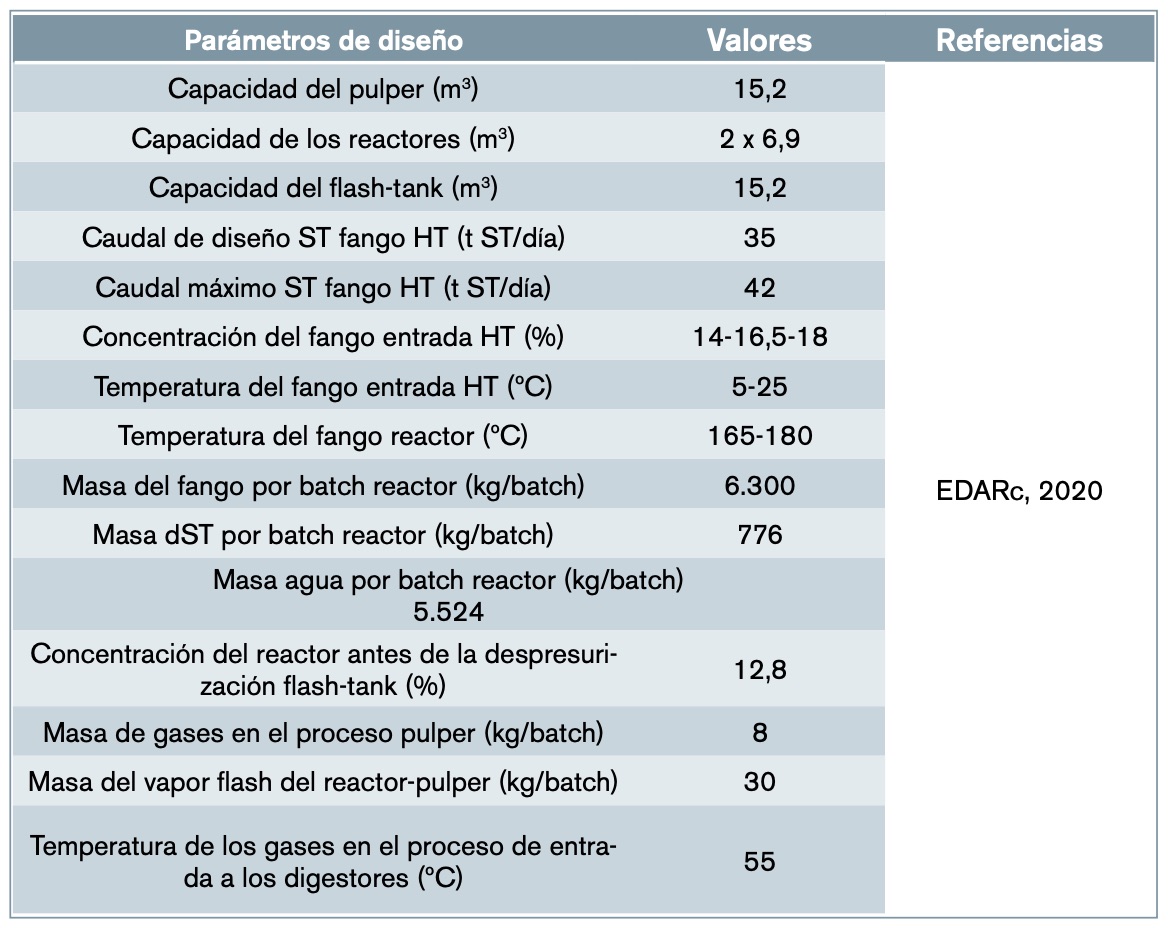
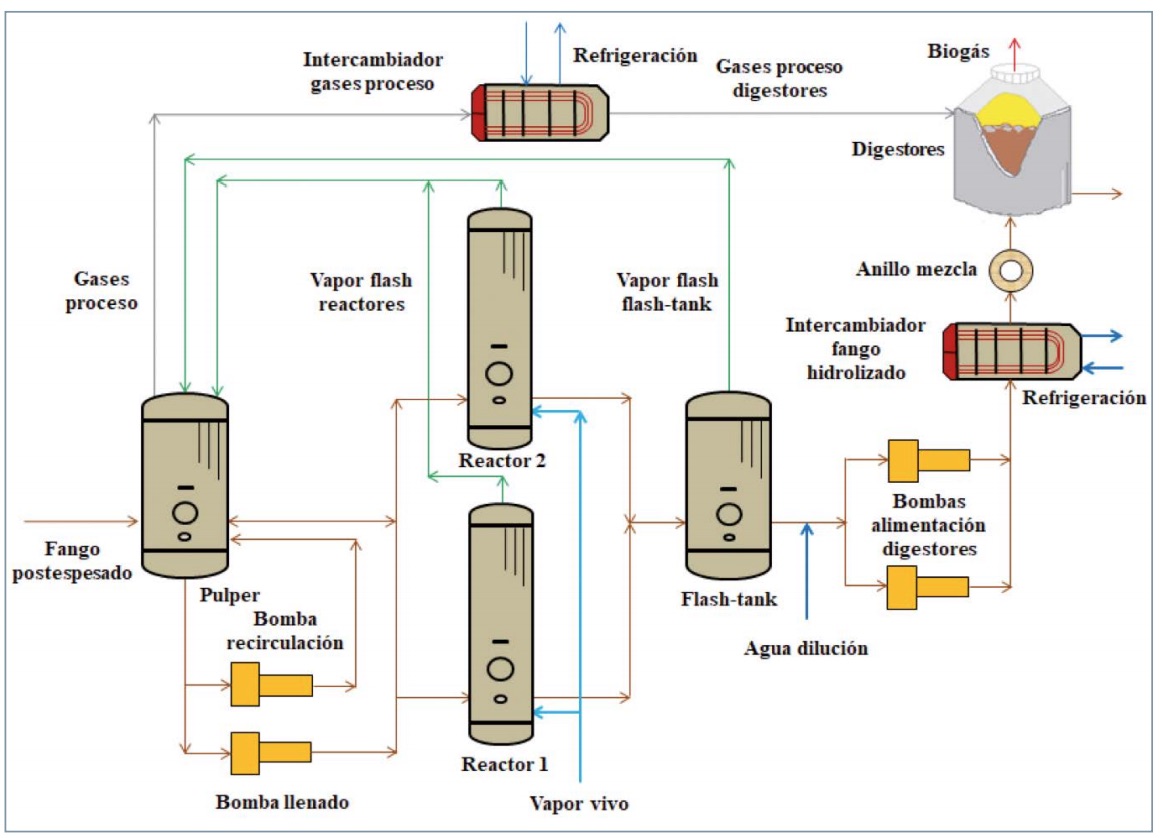
La figura 2 permite observar el diagrama de flujo de operación de la planta THP-B6.2. La concentración del fango espesado mixto compuesto por fango primario y secundario se incrementa en posespesado antes de ser introducido en la planta de HT con objeto de rebajar el contenido de agua presente y disminuir el aporte energético que es necesario realizar en los reactores para alcanzar la temperatura de reacción establecida. Esta planta consta de tres partes fundamentales: pulper, reactores y flash-tank. La HT se produce en los reactores mediante el incremento de temperatura del fango por la aportación externa de vapor vivo saturado y la permanencia de un cierto tiempo de reacción a esta temperatura. A continuación, se realiza una despresurización súbita isentálpica casi instantánea desde los reactores al pulper para enviar a este los gases de proceso. Inmediatamente después, el fango sufre otra despresurización súbita isentálpica hacia el flash-tank y se forma vapor flash que es enviado al pulper y sirve para el precalentamiento del fango posespesado de este tanque antes de ser introducido en los reactores y disminuir la aportación energética a realizar en ellos. La concentración y la temperatura del fango una vez hidrolizado a la salida del flash-tank se disminuye mediante la inyección de agua de dilución y, posteriormente, se bombea hacia el intercambiador de fango hidrolizado para disminuir más la temperatura hasta alcanzar la adecuada de entrada al anillo de mezcla de los digestores.
El fango se introduce en el flash-tank desde el reactor a una velocidad aproximada de 700 m/s, impactando contra las paredes del tanque, donde hay una placa metálica de desgaste que proporciona una superficie adicional para que absorba el impacto del fango despresurizado (Moss, 2013; Loomisa et al., 2018). Los gases de proceso abandonan el pulper hacia los digestores por su parte superior. La entrada de vapor flash al pulper procedente del flash-tank se introduce en el pulper por su parte superior y la entrada de vapor vivo en el reactor, aproximadamente, a 1/4 de la altura del depósito mediante varias toberas. El nivel de fango del pulper y del flash-tank varía constantemente, pero el flujo másico de fango de entrada al pulper y de salida del flash-tank son ambos siempre constantes, aunque no iguales. La concentración del fango va variando según el tanque en el que se encuentre, pues la cantidad de agua se va modificando en función de la entrada de vapor vivo o de entrada-salida de vapor flash en cada tanque.
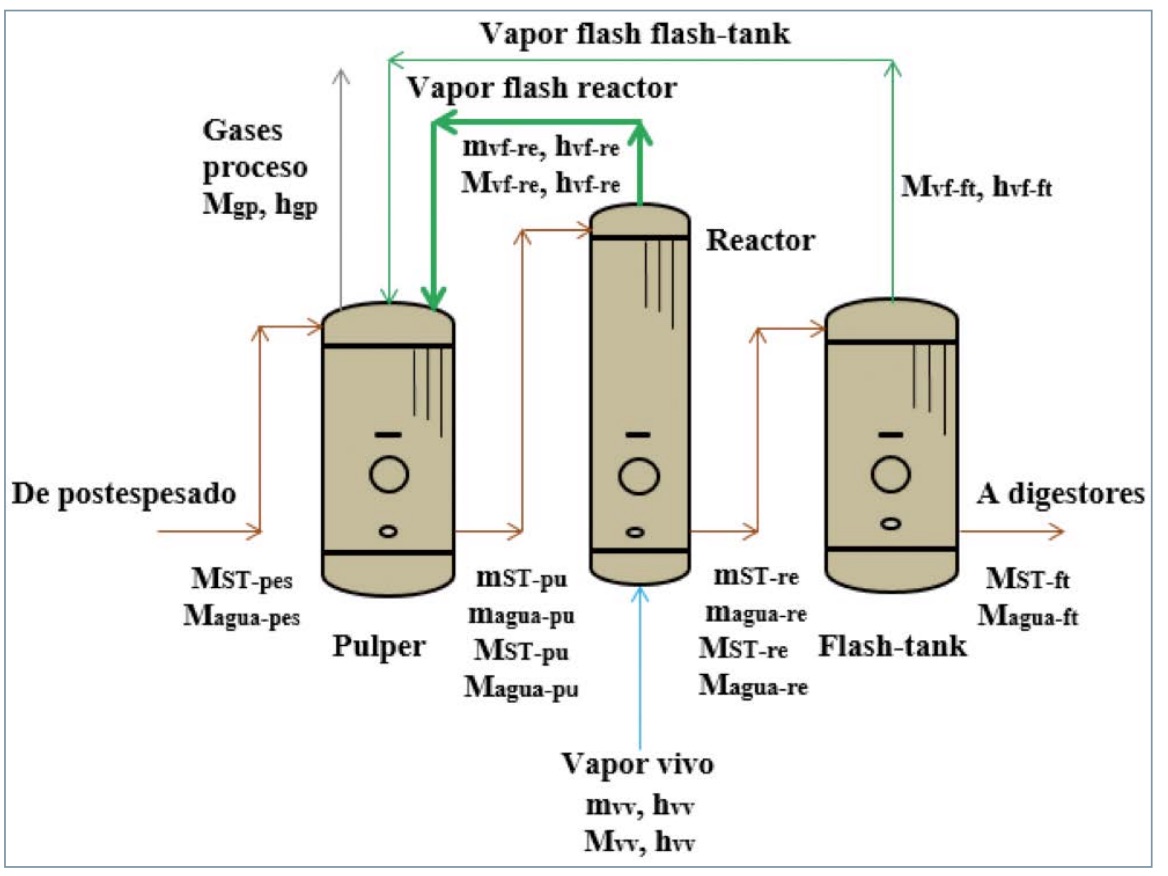
Ecuaciones de cálculo de la planta THP-B6.2
La figura 3 muestra el diagrama de flujo de la planta THP-B6.2 con la nomenclatura de todas las variables necesarias para efectuar el equilibrio de masa y energía de la línea de fangos tanto del ciclo batch como del medio.
Las ecuaciones del ciclo batch son exactamente las mismas que para el ciclo medio, con la única diferencia de que el ciclo batch parte de los valores conocidos de ciertos parámetros de los reactores. Las letras minúsculas de los parámetros indican ciclo batch y las mayúsculas ciclo medio.
La ecuación (1) representa el balance de masa y la Ecuación (2) el de energía de la planta THP-B6.2 y ambas constituyen las denominadas “ecuaciones exteriores” para el ciclo medio. Para obtener estas ecuaciones, se ha aislado completamente la planta y se han considerado únicamente aquellas variables que interactúen con el exterior, sin tener en cuenta lo que ocurra en su interior. El sistema aislado creado debe estar en equilibrio de masa y energía.
donde MST-pes y MST-ft son los flujos másicos de ST del fango de entrada al pulper y de salida del flash-tank (kg/h), Magua-pes y Magua-ft los flujos másicos de entrada de agua del fango al pulper y de salida del flash-tank (kg/h), Mvv el flujo másico de vapor vivo de entrada al reactor (kg/h), Mgp el flujo másico de gases de processo (kg/h), T0 y Tft las temperaturas de fango de entrada al pulper y del flash-tank (ºC), hvv la entalpía específica del vapor vivo de entrada a los reactores (kJ/kg·ºC) y hgp la entalpia específica de los gases de processo (kJ/kg). Las incógnitas a despejar son Mvv y Magua-ft y todas las demás son datos conocidos de la planta.
La ecuación (3) muestra el balance de masa y la Ecuación (4) el de energía del flash-tank.
donde MST-re es el flujo másico de ST del fango de salida del reactor (kg/h), Magua-re el flujo másico de salida de agua del reactor (kg/h), Mvf-ft el flujo másico de vapor flash del flash-tank (kg/h), hvf-ft la entalpía específica del vapor flash del flash-tank (kJ/kg·ºC) y Tre la temperatura del fango de salida del reactor (ºC). Las incógnitas a despejar son en este caso Magua-re y Mvf-ft.
La ecuación (5) muestra el balance de masa y la Ecuación (6) el de energía de los reactores.
donde MST-pu es el flujo másico de ST del fango de salida del pulper (kg/h), Magua-pu el flujo másico de salida de agua del pulper (kg/h), Mvf-re el flujo másico de vapor flash del reactor a pulper (kg/h) y hvf-re la entalpía específica del vapor flash del reactor a pulper (kJ/kg). Las incógnitas a obtener son Magua-pu y Tpu.
La ecuación (7) muestra el balance de masa y la ecuación (8) el de energía del pulper.
Todos los parámetros ya son conocidos, y estas ecuaciones son combinación lineal de las demás.
La ecuación (9) permite transformar cualquier parámetro del ciclo batch a ciclo medio mientras que la aplicación de la ecuación (10) es posible obtener el tiempo del ciclo de operación de los reactores.
donde Parciclo-medio y Parciclo-batch son cualquier parámetro del ciclo batch o medio, tciclo el tiempo del ciclo de operación de los reactores (min), mST-pu la masa de ST por batch introducida en el pulper (kg/batch) y Nre el número de reactores en operación (uds).
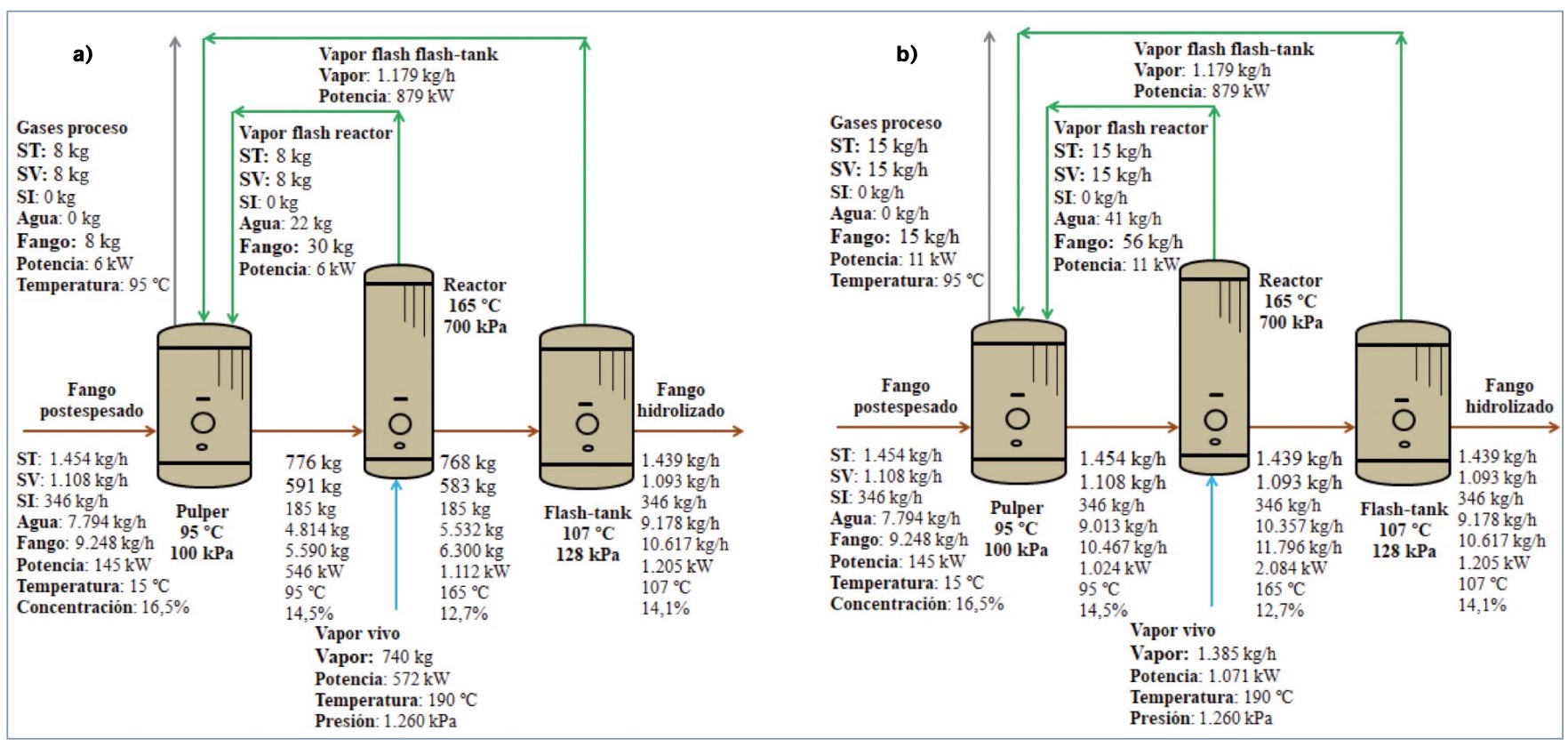
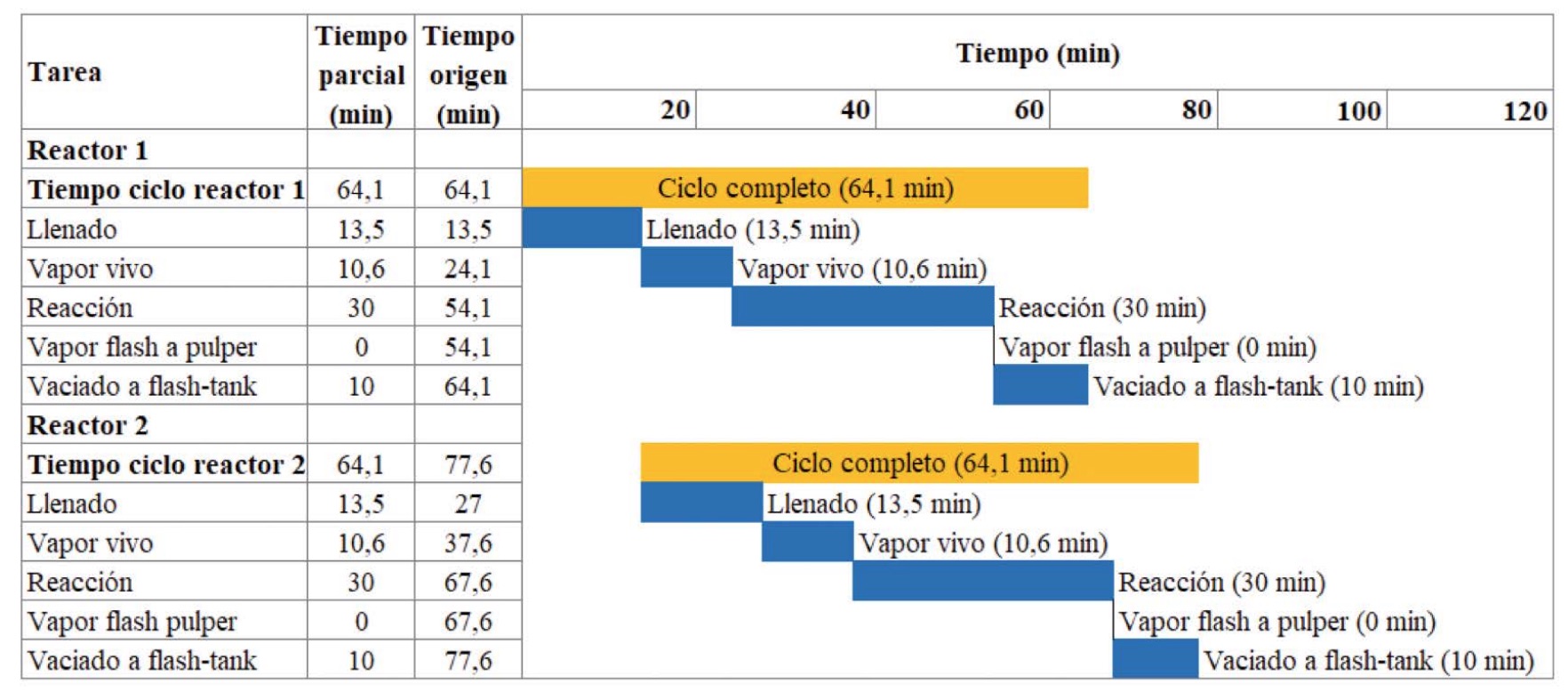
Resultados y discusión
Balance de masa y energía del ciclo batch y medio
La masa de fango introducida por batch en cada uno de los reactores asciende a 6.330 kg/batch, correspondientes a 776 kg ST/batch, agua 4.814 kg/batch y vapor vivo 740 kg/batch, con una concentración del fango del 12,8%. Por otro lado, la salida de vapor flash durante la despresurización isentálpica súbita casi instantánea de los reactores hacia el pulper asciende a 30 kg/batch, compuestos por 8 kg/batch de ST (considerados únicamente SV) y 22 kg/batch de agua mientras que la salida de los gases de proceso del pulper hacia los digestores es de 8 kg/batch, correspondientes a estos SV anteriores procedentes del reactor. El flujo másico de fango enviado hacia el flash-tank desde cada reactor asciende a 6.300 kg/batch, ST 768 kg/batch y agua 5.532 kg/batch, con una concentración ahora del 12,7%. Se observa la pérdida en el reactor de 8 kg/batch de ST, que corresponden a SV exclusivamente y constituyen los gases de proceso. La figura 4a muestra el balance de masa y energía de THP-B6.2 para el ciclo batch de un reactor con los valores obtenidos de sus principales parámetros.
En la figura 4b se puede ver la aportación de 56 kg/h (11 kW) de vapor flash enviados desde el reactor hacia el pulper formados por 15 kg/h de SV (gases de proceso) y 41 kg/hora de agua. Asimismo, desde el pulper se envían 15 kg/hora (11 kW) de gases de proceso hacia los digestores. Se observa también el intercambiador de refrigeración de los gases de proceso encargado de enfriarlos desde 95 ºC hasta 55 ºC antes de ser introducidos en los digestores. Como consecuencia de esta refrigeración, parte de estos gases condensan y retornan al pulper por la misma tubería formando un bucle. Sin embargo, estos condensados no se han tenido en cuenta en el balance de masa y energía del pulper.
El agua de dilución inyectada en el fango a la salida del flash-tank antes de las bombas de impulsión de fango hidrolizado a digestores tiene dos misiones importantes: reducir la concentración del fango del 14,1% hasta el 10% para introducirlo, posteriormente, en los digestores y reducir la temperatura del fango de 107 °C a 79 °C para proteger las bombas de tornillo de alimentación de fango hidrolizado a digestores.Una vez alcanzada la concentración del 10% y la temperatura de 79 °C, esta debe reducirse aún más hasta 50 °C con objeto de que los digestores mantengan su temperatura de funcionamiento de 41 °C teniendo en cuenta las pérdidas de potencia térmica asociadas a la transmisión de calor y pérdidas en tuberías e intercambiadores y biogás producido. Esta disminución de temperatura se realiza en el intercambiador de fango hidrolizado, cediendo 472 kW mediante la refrigeración con agua de servicios generales que presenta una temperatura de 15 °C.
Operación de la planta THP-B6.2
La tabla 4 muestra cada una de las etapas del ciclo de operación de llenado-vaciado de fango, vapor flash a pulper e inyección de vapor en los dos reactores en función del tiempo y en el punto de diseño de fango espesado establecido. Cada reactor cuenta con un total de cinco etapas de operación y un desfase en el tiempo de funcionamiento equivalente al tiempo de llenado de un reactor, pues solo es posible llenar uno a la vez.
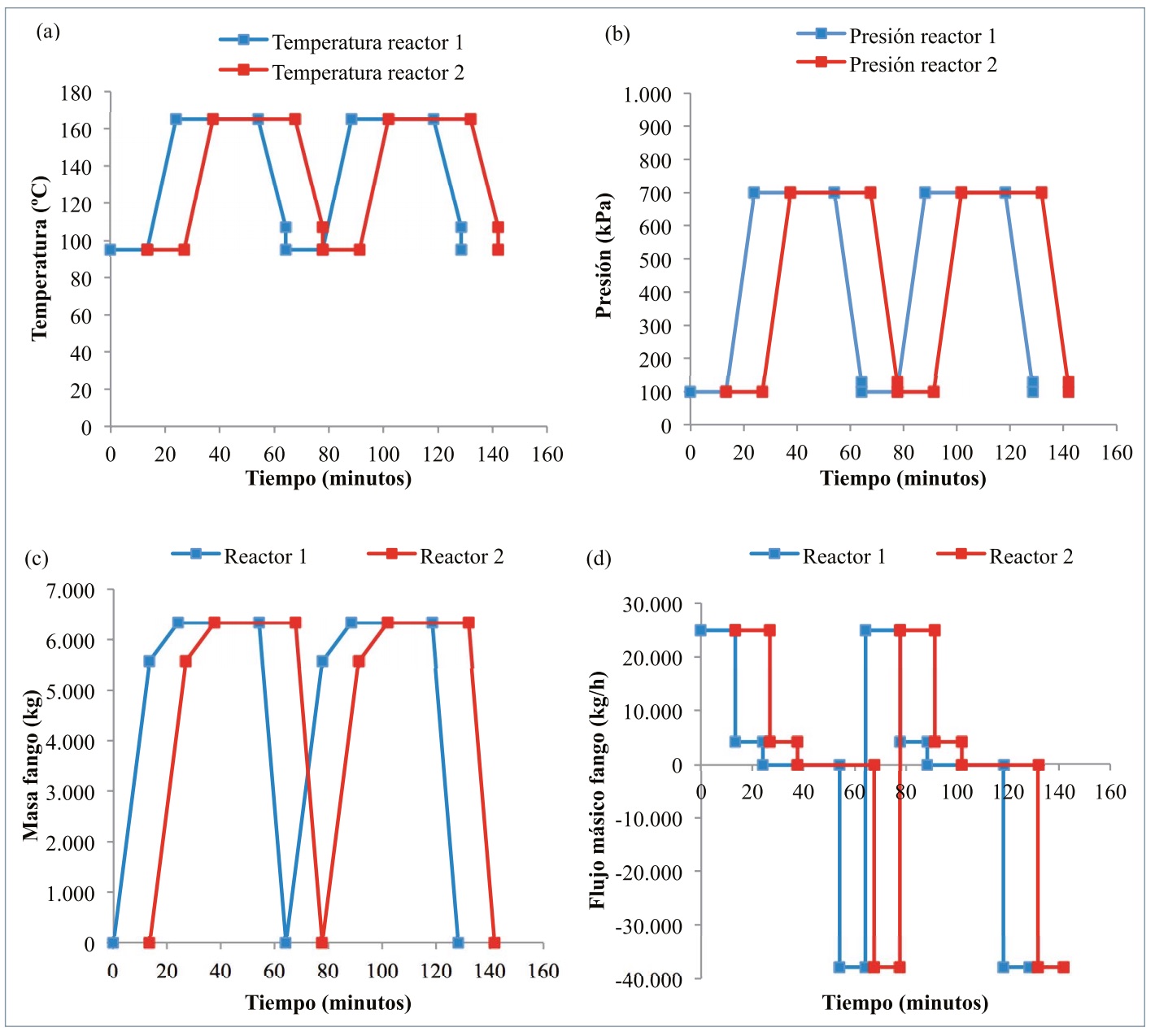
La figura 5a representa la evolución de la temperatura y la figura 5b de la presión del fango en los reactores 1 y 2, ambos en función del tiempo. Se ha representado el desplazamiento en el tiempo del funcionamiento de estos reactores que operan en discontinuo conllevado de forma cíclica a incrementos considerables de temperatura y presión. Esto favorece la fatiga de los materiales involucrados e implica una elevación de los costes de mantenimiento de estas unidades. La temperatura de reacción alcanza los 165 ºC, mientras que la presión debe aumentar hasta los 700 kPa. En la figura 5c se puede observar el diagrama formado por una serie de rectas que constituyen cada una de las cinco etapas de operación señaladas anteriormente en la tabla 4 y cuya pendiente se corresponde con el flujo másico de llenado o vaciado de fango en los reactores. La figura 5d indica la evolución del flujo másico de entrada-salida de fango en los dos reactores en función del tiempo y que corresponde al valor de cada una de las pendientes de las rectas tratadas anteriormente en la figura 5c.
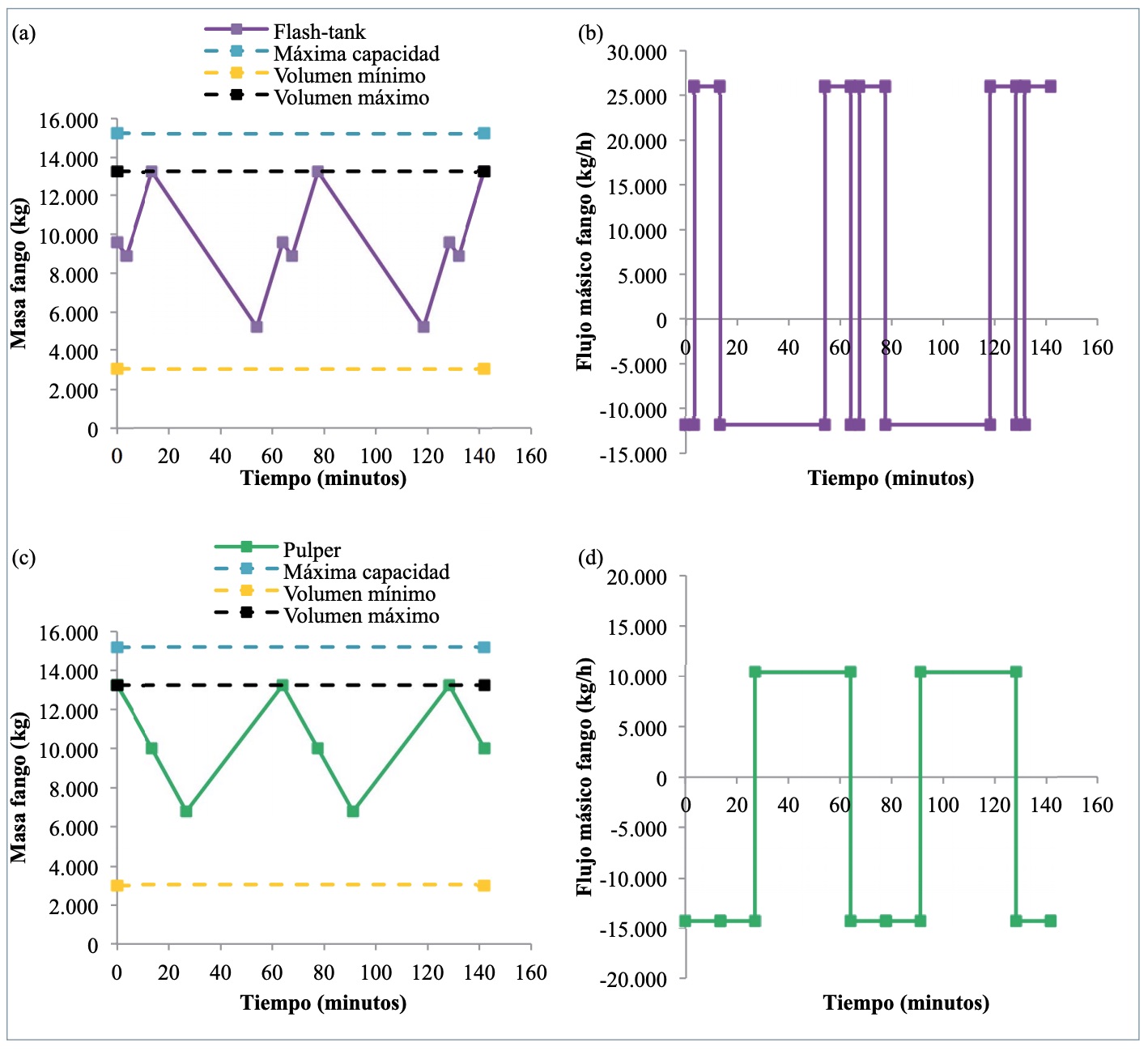
pulper. b) Flujo másico del pulper.
La figura 6a muestra el ciclo de operación de la evolución del llenado-vaciado de fango en el flash-tank en función del tiempo. El nivel del fango en el flash-tank está influido por la entrada de fango hidrolizado desde los reactores y por las salidas de vapor flash hacia el pulper y de fango hidrolizado a los digestores y es variable en función del tiempo. La capacidad máxima de llenado y vaciado en flashtank y pulper es del 87% y el 20% de la capacidad del tanque (EDARd , 2020). La figura 6b representa el flujo másico de entrada y salida de fango que se origina en el flash-tank en función del tiempo, coincidente con las pendientes de las rectas anteriores de la figura 6.a. Se puede apreciar las cuatro etapas que conforman un ciclo completo de cada ciclo. La figura 6c representa el ciclo de operación de llenado-vaciado en el pulper en función del tiempo y la figura 6d representa el flujo másico de entrada-salida de fango que se produce en el pulper en función del tiempo y se pueden observar las dos etapas que conforman un ciclo completo.
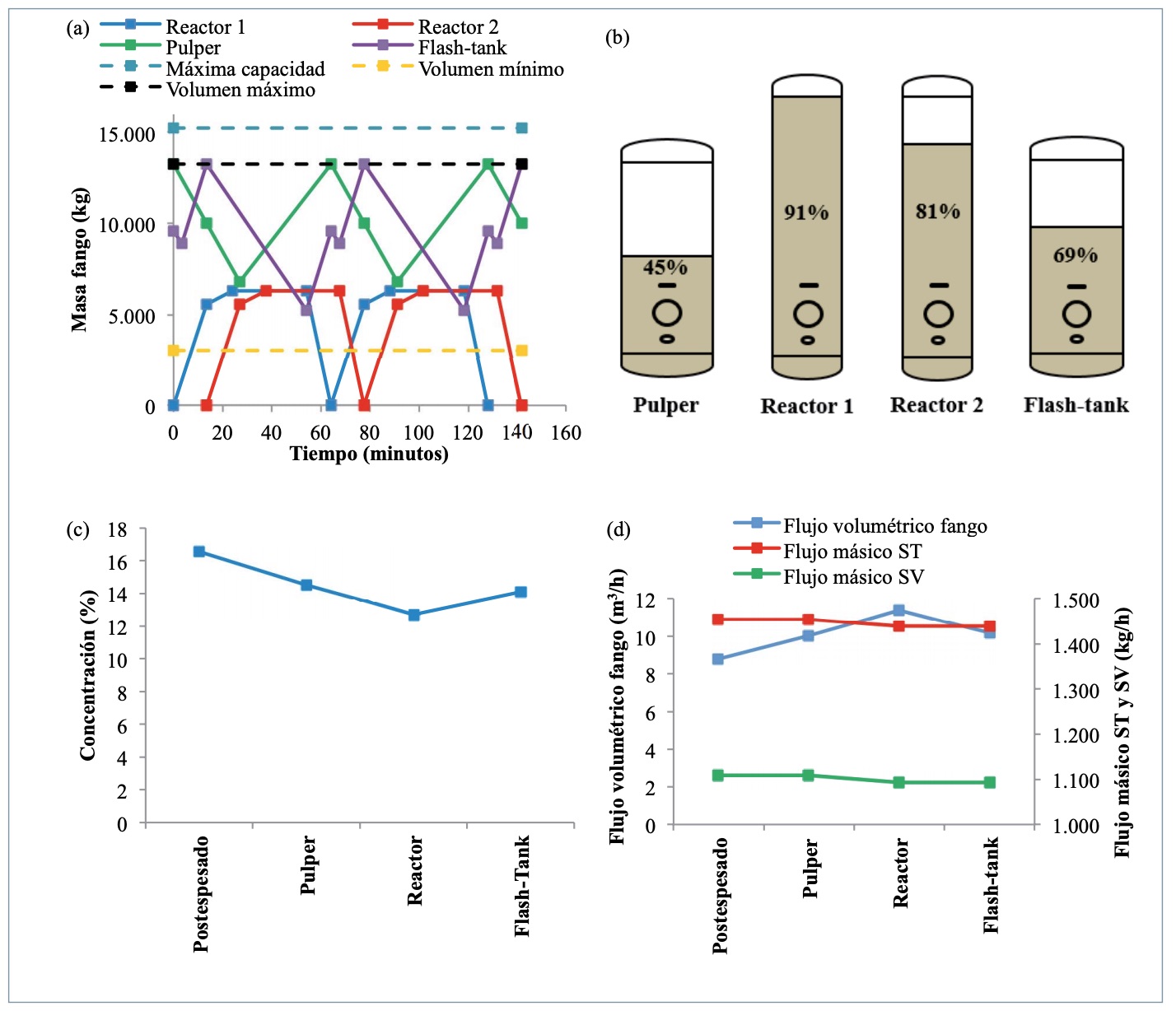
de ST y SV.
La figura 7a permite observar el diagrama de llenado-vaciado simultáneamente en los cuatro elementos que forman la planta: pulper, dos reactores y flash-tank. La figura 7b permite apreciar de forma aproximada los niveles en porcentaje sobre el total de cada uno de los tanques cuando el valor del tiempo del ciclo es de 27 minutos. La figura 7c visualiza la evolución de la concentración en el pulper, reactores y flash-tank en función del tiempo y la figura 7d muestra la variación del flujo volumétrico y másico de ST y SV en el pulper, reactores y flash-tank en función del tiempo.
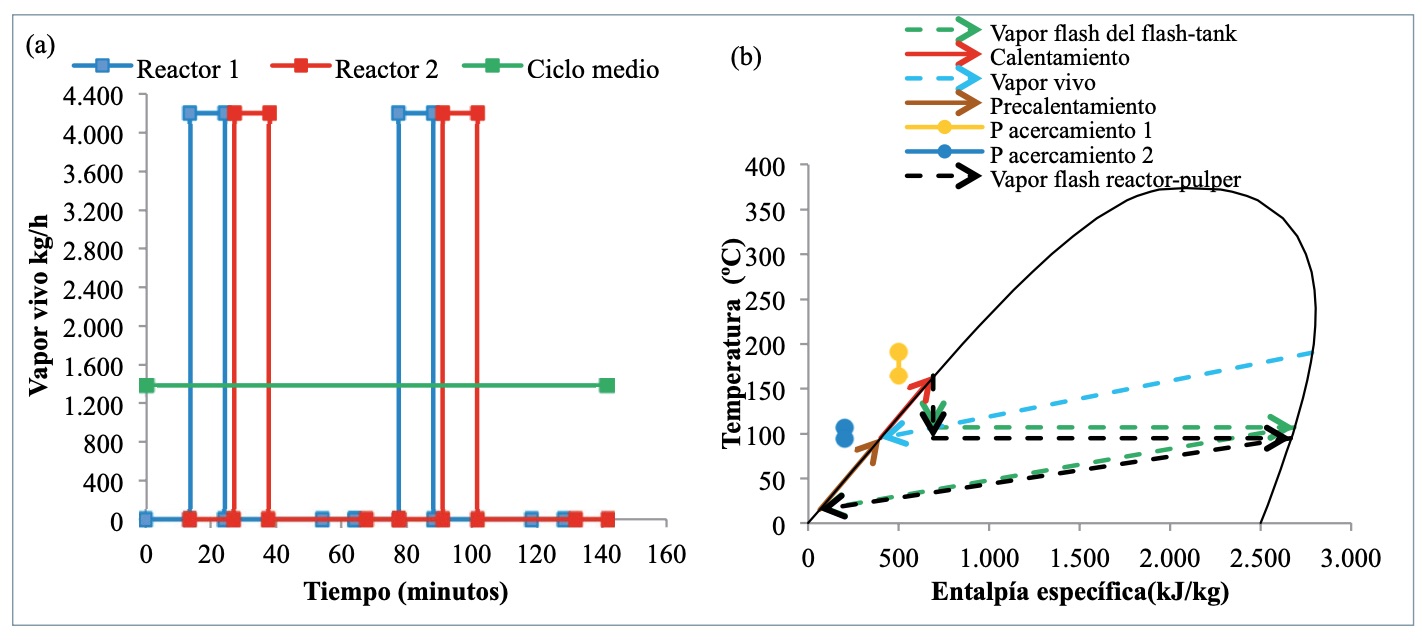
pulper.
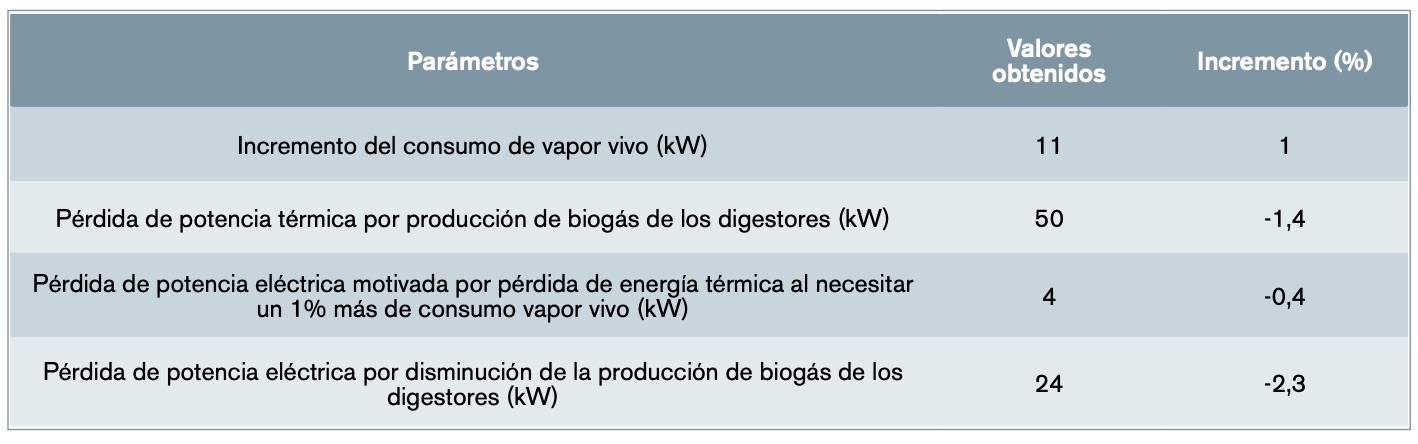
La figura 8a indica la evolución del flujo másico de vapor vivo procedente de la caldera de recuperación inyectado en los reactores 1 y 2 en función del tiempo. A efectos del cálculo desarrollado, se consideran dos inyecciones de vapor vivo de los reactores 1 y 2 en un ciclo completo de 64,1 minutos como si fueran únicamente del reactor 1, lo que es totalmente equivalente al tratarse de reactores iguales y tener el mismo ciclo. El ciclo medio presenta un valor de 1.385,1 kg/hora de vapor correspondiente al 33% del inyectado en cada batch. La figura 8b representa el diagrama temperatura-entalpía específica del precalentamiento del fango en el pulper mediante vapor flash proveniente del flash-tank y reactores además del calentamiento del fango en los reactores mediante vapor vivo inyectado desde la caldera de recuperación.
El equilibrio de energía de los gases de proceso enviados desde el pulper hacia los digestores alcanza los 11 kW, lo que supone el 1% sobre la energía del vapor vivo introducido, que asciende a 1.071 kW (1.060 kW sin gases de proceso). Los gases de proceso abandonan el pulper hacia los digestores, donde son refrigerados en el denominado foul gas skid (Loomisb et al., 2018). Este proceso se realiza mediante agua del circuito de servicios generales, rebajando de esta forma su temperatura antes de la entrada en digestores. Los gases de proceso recolectados en el pulper se consideran gases contaminantes debido a toxicidad (mercaptanos), mal olor y el nivel de saturación de agua que poseen. En otras plantas Cambi, a diferencia de la de Burgos, los gases de proceso enfriados se comprimen para ser introducidos directamente en las tuberías del sistema de alimentación de fango hidrolizado a los digestores para su descomposición (Loomisc et al., 2018; Williams y Burrowes, 2017). La tabla 5 indica las pérdidas de energía asociadas a la acción de los gases del proceso.
Conclusiones
La planta de hidrólisis térmica de fangos analizada permite elevar la producción de biogás en digestores y de energía eléctrica en motogeneradores, además de disminuir la cantidad de fango deshidratado con respecto a la digestión anaerobia inicial. Sin embargo, la instalación de un proceso de hidrólisis térmica Cambi requiere una inversión importante y tiene como desventajas la elevación del consumo de polielectrolito, el consumo excesivo de biogás en la caldera mixta de recuperación al ser un proceso batch y desaprovechar gran cantidad de la energía de los gases de escape, el autoconsumo de energía eléctrica propia tras la inserción del nuevo proceso, la gran complejidad introducida y los costes de operación adicionales que se introducen en la planta. La gran ventaja de la hidrólisis térmica es la disminución del volumen de digestores al reducirse el tiempo de retención hidráulica, por lo que su aplicación óptima es para depuradoras de nueva construcción, y se desaprovecha esta importante ventaja en depuradoras ya en funcionamiento como es el caso. Esta tecnología desaprovecha una cantidad elevada de energía térmica que repercute negativamente en el equilibrio energético-económico de la planta. Con todos estos pros y contras, la forma de establecer la viabilidad de un proyecto de hidrólisis térmica es realizar un minucioso balance económico del proceso completo.
Agradecimientos
El autor desea dar las gracias al apoyo recibido por la EDAR de Burgos y a la Universidad de León durante la redacción de este artículo.
Referencias
Abelleira J, Pérez-Elvira S, Sanchez-Oneto J, Portela J, Nebot E. (2012). Advanced Thermal Hydrolysis of secondary sewage sludge: A novel process combining thermal hydrolysis and hydrogen peroxide addition. Resources, Conservation and Recycling, 59, 52-7. https://doi.org/10.1016/j. resconrec.2011.03.008.
Abelleira J, Pérez-Elvira S, Sánchez-Oneto J, De la Cruz R, Portela R, Nebot E. (2015). Enhancement of methane production in mesophilic anaerobic digestion of secondary sewage sludge by advanced thermal hydrolysis pretreatment. Water research, 71, 330-40. https://www.researchgate. net/publication/ 272296616Enhancement_of_ methane_production_in_mesophilic_anaerobic_ digestion_of_secondary_sewage_sludge_by_ advanced_thermal_hydrolysis_pretreatment.
Chae K, Kang J. (2013). Estimating the energy independence of a municipal wastewater treatment plant incorporating green energy resources. Energy Conversion and Management, 75, 664-72. https:// doi.org/10.1016/j.enconman.2013.08.028.
EDAR. (2020). Estación de tratamiento de aguas residuales de Burgos.
Feng G, Ta W, Zhong N, Liu L. (2014). Effects of thermal treatment on physical and expression dewatering characteristics of municipal sludge. Chemical Engineering Journal, 247, 223-30. https:// www.researchgate.net/publication/261184316_ Effects_of_thermal_treatment_on_physical_ and_expression_dewatering_characteristics_of_ municipal_sludge.
Kleiven H, Soler L, Sanz M. (2007). La HT como pretratamiento de la digestión de fangos de depuradora. Una alternativa madura. III Jornadas técnicas de gestión de sistemas de saneamiento de aguas residuales. https://aca-web.gencat.cat/ aca/documents/…/jornadatecnica003/volum_ ponencies_es.p, acceso abril 2020.
Kleiven H. (2014). Presentation to Delegation from Poland. https://docplayer.net/20745602- Presentation-to-delegation-from-poland, acceso abril 2020.
Loomis P, Jacobs T, Samir Mathur S, Guven E, Hurtado, Christy P. (2018). Thermal Hydrolysis. The Next Generation.https://www.cdmsmith.com/-/ media/White-Papers/Thermal-Hydrolysis—-TheNext-Generation—-Loomis.pdf, acceso abril 2020.
Moss L. (2013). Thermal Hydrolysis Pretreatment: Benefits and Challenges. http://www.tacwa.org/ agendaandpresentations/presentation/2013_ Nov_4_Lynne_Moss_THP_.pdf, acceso abril 2020.
Neyens E, Baeyens J. (2003). A review of thermal sludge pre-treatment processes to improve dewaterability. Journal of Hazardous Materials, 98, 51-67. https:// w w w . r e s e a r c h g a t e . n e t / p u b l i c a t i o n / 8023105_A_Review_of_Thermal_Sludge_ Pre-Treatment_Processes_to_Improve_ Dewaterability.
Peña K, Steinmetz H. (2012). Evaluation of pretreatment on the first stage of an anaerobic digester for enhancing bio-hydrogen production and its associated energy balance. Energy Procedia, 29, 469-79. https://doi.org/10.1016/j. egypro.2012.09.055.
Phothilangka P. (2008). Sludge disintegration technologies for improved biogas yield. Doctoral Thesis, Faculty of Civil Engineering, University of Innsbruck, Österreich. https:// www.researchgate.net/profile/ Bernhard_Wett / publication/23425451, acceso abril 2020.
Sarwar R. (2015). Effect of Thermal Pretreatment on Digestibility of Thickened Waste Activated Sludge and Primary Sludge in Two-stage Anaerobic Digestion University of Waterloo, Canada. https://uwspace.uwaterloo.ca/bitstream/ handle/10012/10051/Sarwar_Rubaiya. pdf?sequence=1, acceso abril 2020.
Stelte W. (2013). Steam explosion for biomass pre-treatment. http://www.teknologisk.dk/_root / media/52681_RK%20report%20steam%20 explosion.pdf, acceso abril 2020.
Urrea J, Collado S, Laca A, Díaz M. (2015). Rheological behaviour of activated sludge treated by thermal hydrolysis. Journal of Water Process Engineering, 5, 153-9. https://doi.org/10.1016/j. jwpe.2014.06.009.
Wilson C, Novak J. (2009). Hydrolysis of macromolecular components of primary and secondary wastewater sludge by thermal hydrolytic pretreatment. Water research, 43, 4489-98. https://doi.org/10.1016/j.watres.2009.07.022.
Yenigun O, Demirel B. (2013). Ammonia inhibition in anaerobic digestion: A review. Process Biochemistry 48, 901-11. https://doi. org/10.1016/j.procbio.2013.04.012.
Zhang L, Zhang Y, Zhang Q, Verpoort F, Cheng W, Cao L, Li M. (2014). Sludge gas production capabilities under various operational conditions of the sludge thermal hydrolysis pretreatment process. Journal of the Energy Institute, 87, 121-6. https://doi.org/10.1016/j.joei.2014.03.016.