Aplicación de mapa de flujo de valor a la mejora en los procesos de diseño y construcción de reformas en edificios de viviendas
Application of a value flow map to the improvement of the design and construction processes of reforms in residential buildings
Paula Álvarez García (1); Manuel Domínguez Somonte (2) y María del Mar Espinosa Escudero (3)
Resumen
El pensamiento esbelto está fuertemente arraigado en el sector industrial, que tiene unos claros objetivos de eficiencia y productividad alentados por la producción en serie. El mundo de la arquitectura, como el del sector naval y aeronáutico permanece estancado en su búsqueda de una fabricación óptima del prototipo. El pensamiento esbelto, revolucionario al cuestionar la producción por lotes, se presenta como una oportunidad para el sector. El objetivo del presente artículo es el desarrollo de una metodología esbelta capaz de establecer un plan de mejora en los procesos de diseño y construcción de reformas en edificios de viviendas. Para tal fin, se propone utilizar la herramienta de mapa de flujo de valor (MFV), capaz de analizar el estado actual de la organización e implementar una serie de cambios que eliminen el desperdicio y añadan valor a los proyectos. Estos cambios tienen relación con la aplicación de otras herramientas propias de la construcción esbelta como las tecnologías de sistemas de información en construcción (SIC).
Palabras clave: Diseño esbelto, arquitectura, construcción, valor.
Abstract
Lean thinking is strongly rooted in the industrial sector, which has clear efficiency and productivity objectives encouraged by mass production. The world of architecture, like the naval and aeronautical sector, remains bogged down in its search for optimum prototype manufacturing. Lean thinking, revolutionary in questioning batch production presents itself as an opportunity for the industry. The objective of this article is the development of a lean methodology capable of establishing a plan of improvement in the design and construction processes of reforms in residential buildings. To this end, it is proposed to use the Value Flow Map (MFV) tool, capable of analyzing the current state of the organization and implementing a series of changes that eliminate waste and add value to projects. These changes are related to the application of other tools of lean construction such as Building Information Modeling (BIM).
Keywords: Lean design, architecture, construction, value
Recibido / received: 20/06/2021. Aceptado / accepted: 01/07/2021.
1 Ingeniería del diseño. Universidad Nacional de Educación a Distancia-UNED (España).
2 Escuela Técnica Superior de Ingenieros Industriales, Departamento de Ingeniería de Construcción y Fabricación de la Universidad Nacional de Educación a Distancia-UNED (España).
3 Escuela Técnica Superior de Ingenieros Industriales, Departamento de Ingeniería de Construcción y Fabricación de la Universidad Nacional de Educación a Distancia-UNED (España).
Autor para correspondencia: palvarez495@alumno.uned.es (P. Álvarez).
ORCID: 0000-0002-4748-0588 (P. Álvarez); 0000-0003-1037-0542 (M. Domínguez); 0000-0002-2812-7041 (M. M. Espinosa)
El pensamiento esbelto, lo más actual
Womack y Jones (1) definen el pensamiento esbelto como un método para hacer más y más con menos y menos, actualizando así la famosa frase del gran maestro de la arquitectura, Mies van der Rohe. El método busca especificar valor, alinear las acciones creadoras de valor de acuerdo con la secuencia óptima, llevar a cabo estas actividades sin interrupción siempre que alguien las solicite y realizarlas de forma cada vez más eficaz.
Tipos de despilfarro o muda
El origen japonés del término se explica históricamente. Taiichi Ohno, ejecutivo de Toyota, es el responsable de haber identificado los primeros siete tipos de muda. La relevancia histórica de este personaje industrial reside en su descubrimiento de que la mayor parte de las actividades que se llevan a cabo en una organización, no añaden valor neto al producto o servicio final que se entrega al cliente y, por ello, se deben eliminar o mejorar. A continuación, se desarrollan los siete tipos de muda identificados como obstáculos en la cadena de valor por Taiichi Ohno, incluyendo dos más, uno introducido por los ya citados autores de lean thinking en 1996 y uno último definido por Jeffrey Liker (2). A modo introductorio de la cuestión arquitectónica, a la hora de explicar estos patrones, lo haremos adaptándolos a la industria de la construcción (3).
Sobreproducción
Exceso de producción tanto con respecto a la cantidad como a la calidad. Elaboración de planos adicionales, no necesarios o excesivamente detallados; uso de un equipamiento muy sofisticado cuando uno más sencillo sería suficiente.
Esperas
Tiempo de inactividad resultado de la no finalización de un proceso anterior, de falta de datos, materiales, equipos, aprobaciones, financiación, personal, área de trabajo inaccesible, iteración entre varios especialistas, contradicciones en los documentos de diseño, retraso en el transporte o instalación de equipos, falta de coordinación entre cuadrillas, repetición del trabajo debido a cambios en el diseño y revisiones, accidentes por falta de seguridad.
Transporte innecesario
Movimiento interno de recursos redundante en la obra debido a una mala distribución y falta de planificación de los flujos de materiales e información.
Sobreprocesamiento
Inclusión de aquellos procesos que causan el uso excesivo de materia prima, equipos o energía generando, además, controles de calidad adicionales.
Exceso de inventario Inventarios excesivos, innecesarios o antes de tiempo que conducen a pérdidas de material y a costes financieros por la compra anticipada.
Movimientos innecesarios
Llevados a cabo por los trabajadores durante su trabajo. Utilización de equipos inadecuados, métodos de trabajo ineficaces, falta de estandarización o mal acondicionamiento del lugar de trabajo.
Defectos de calidad
Errores en el diseño, mediciones y planos, falta de coordinación entre técnicos, mano de obra poco cualificada.
Bienes y servicios sin valor para el cliente
Especificaciones técnicas y de diseño no solicitadas en el encargo, atractivas para los profesionales del sector, pero no para el cliente.
Talento
Pérdida de nuevas ideas y buenas aptitudes por la falta de motivación y atención a los empleados.
Principios del diseño esbelto
Los principios para alcanzar el valor y evitar el desperdicio son los que siguen (3):
Especificar el valor
El concepto de valor constituye el punto de partida para el pensamiento esbelto y se define como aquello que el cliente quiere. El papel del productor es el de crear valor a partir de las necesidades expresadas por el cliente, principal sostén de la empresa a largo plazo. Para especificar el valor, la herramienta fundamental es el diálogo con el consumidor.
Flujo de valor
Definido como el conjunto de todas las acciones específicas requeridas para la transformación de materiales e información en un producto o servicio terminado y entregado al cliente, desde la concepción de su diseño hasta su ejecución y desde el pedido hasta la entrega y cobro.
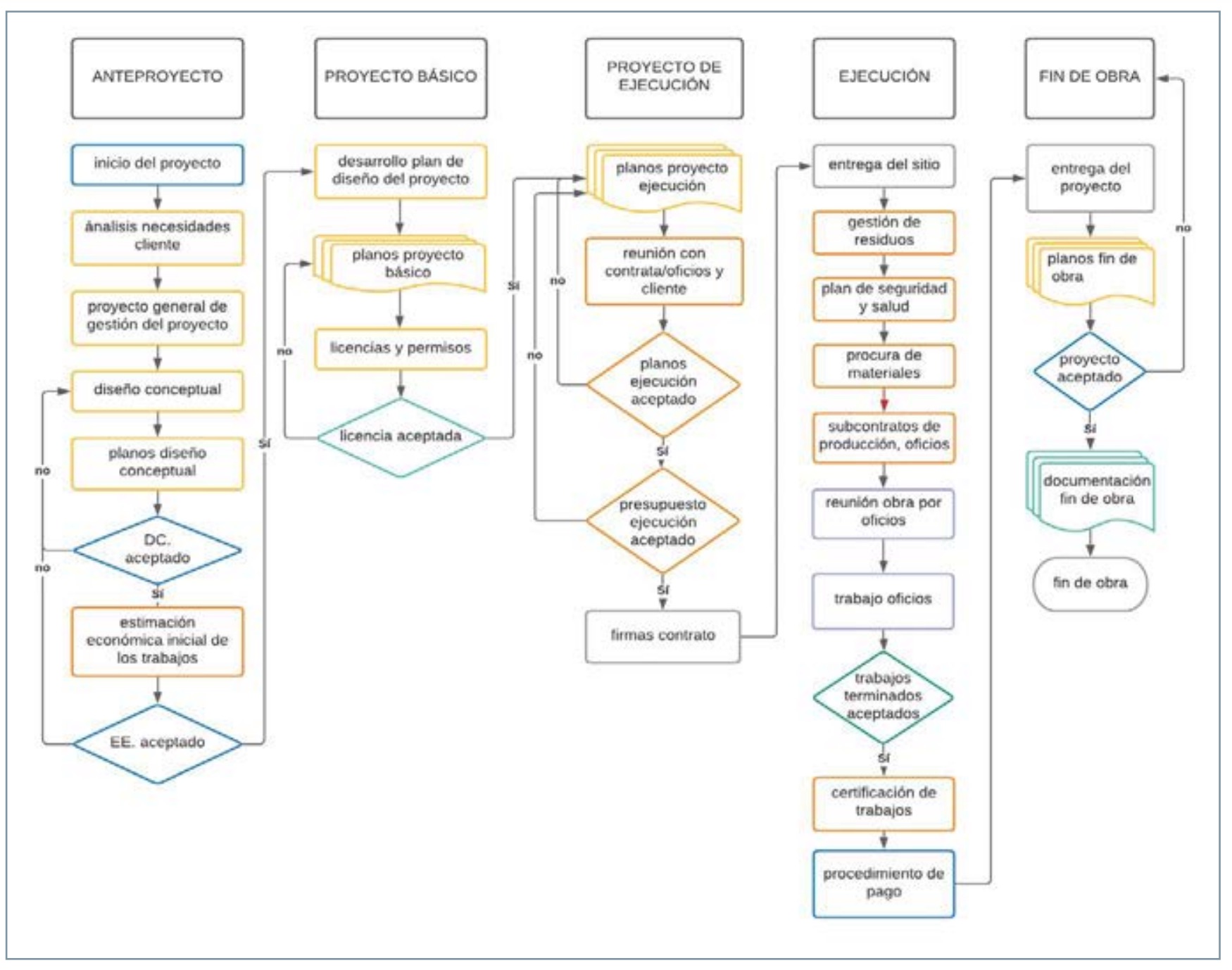
Flujo
Reconocidos el valor y aquellas acciones que lo generan, nuestra organización está en posición de llevar a cabo una reorganización del sistema. En este punto, el pensamiento esbelto critica la producción mediante lotes, ya que esta duplica ejercicios de transporte y movimientos. Este dato, confuso para los sistemas tradicionales de producción industrial, se traduce en cambio, atractivo para el sector de la arquitectura, ya que la alternativa creada por Taiichi Ohno y sus colaboradores, el trabajo de flujo continuo, es fácilmente adaptable al sector y su producción de construcciones prototipo.
Sistema de tracción
El cliente en una empresa de este tipo no es solo el consumidor final (cliente externo), sino que, durante la producción de flujo continuo, un trabajo aguas abajo es cliente de otro, aguas arriba (clientes internos). De este modo, las acciones posteriores solicitan, impulsan la actividad de las anteriores, dan señales de sus necesidades, de modo que se evitan sobreproducciones y excesos de inventario. Es el cliente, tanto externo como interno, quien tira de la demanda y no el fabricante o productor quien empuja los productos hacia el cliente.
Perfección
Entendida como horizonte, la perfección es la búsqueda sin límites de la reducción de esfuerzo, tiempo, espacio, coste y fallos proporcionando así, valor puro al consumidor. Se rige por las acciones del sistema de tracción y, gracias a él, la empresa encuentra aquellos obstáculos que han de ser eliminados para que el flujo de valor sea realmente continuo.
Transparencia
Estímulo para alcanzar la perfección. Tiene que ver con lo anotado en el apartado de flujo de valor. Se traduce en el pleno acceso a la información de todos los implicados en el proceso, desde las primeras etapas (diseño), de modo que la búsqueda de mejoras es continua y transversal a todos los participantes.
Capacitación
Para que el estímulo anterior pueda tener cabida es necesario contar con mano de obra capacitada, que detecte errores y apta para trabajar en la mejora continua de toda la cadena de valor.
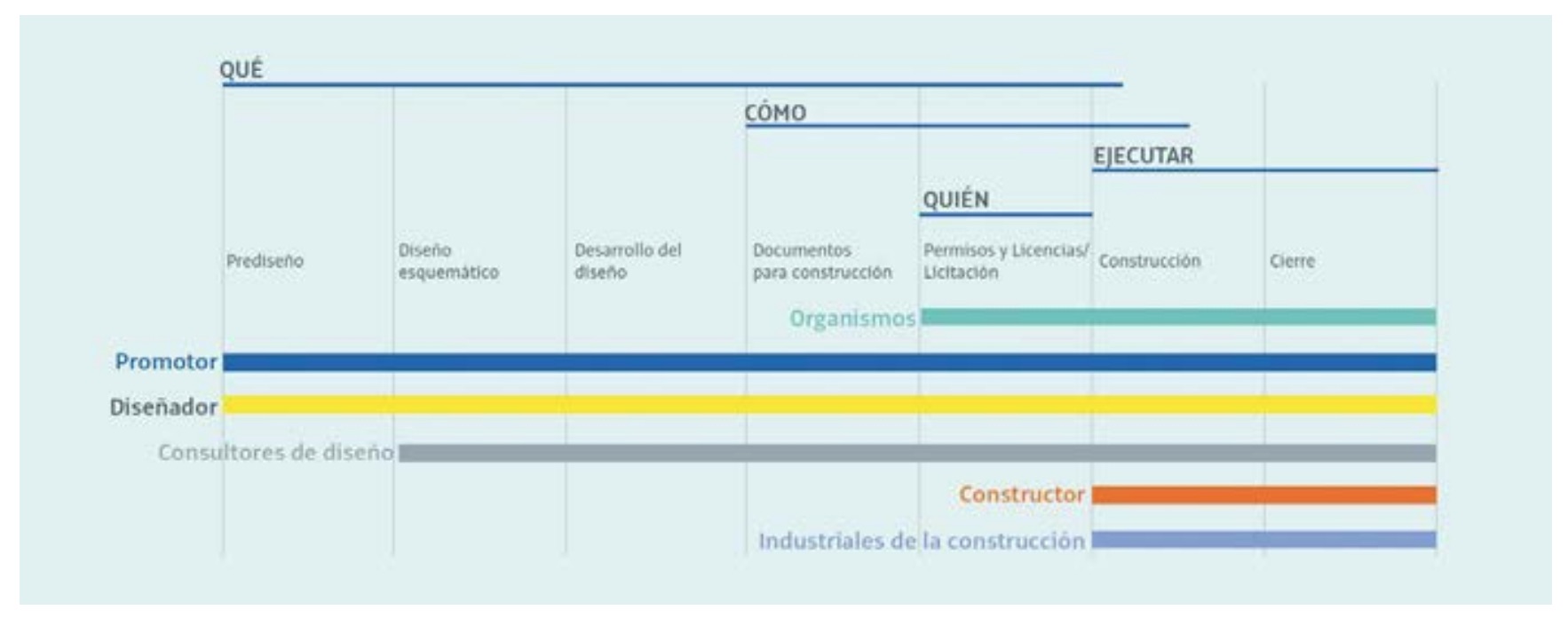
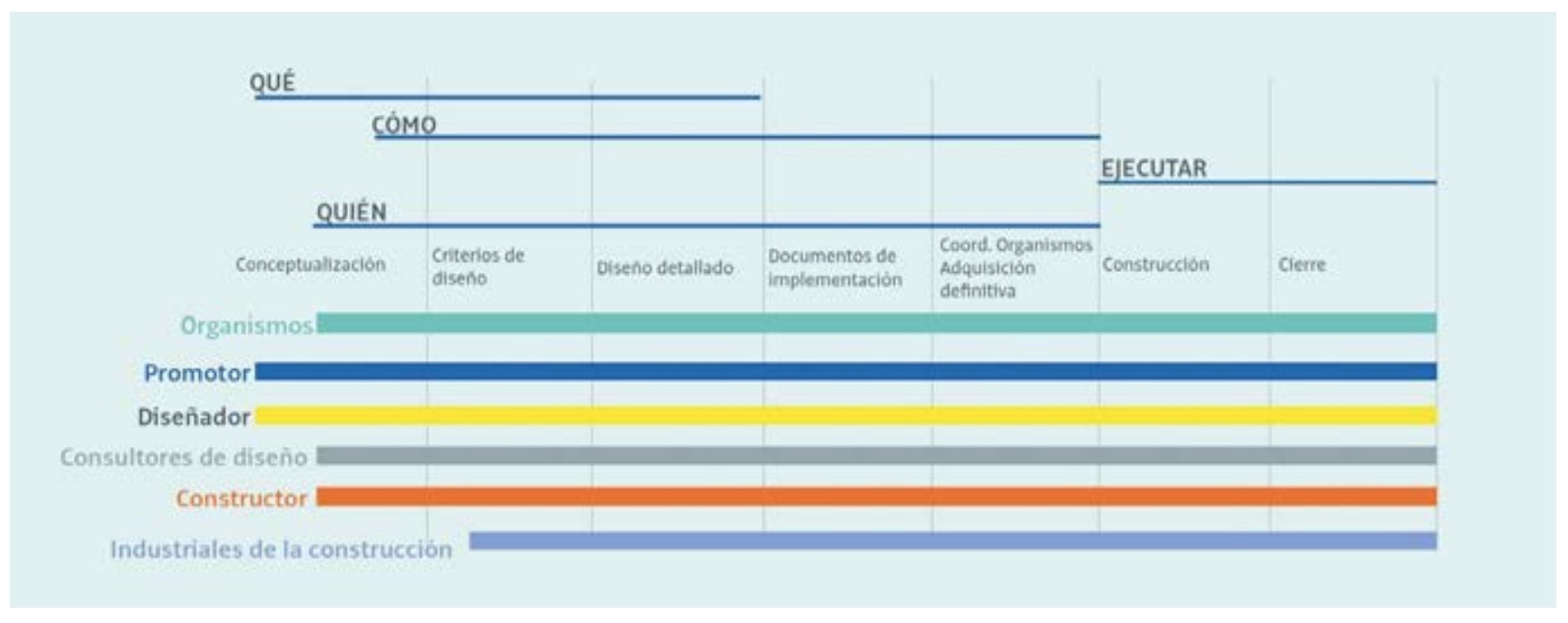
Herramientas de diseño esbelto
Sistema del último planificador
Se trata de un sistema planificador que actúa sobre las relaciones entre etapas (así es como se planifica tradicionalmente) y participantes (4).
– Definición de proyecto. Especificación del valor para las partes interesadas, el criterio de diseño y los conceptos de diseño. Esta etapa es llevada a cabo por representantes de todas las fases del proyecto, a diferencia de la gestión tradicional, que únicamente implica al ingeniero/ arquitecto y al cliente.
– Diseño preciso. Diseño de producto y del proceso para su construcción. En este momento es importante prestar atención a posibles oportunidades que ayuden a incrementar el valor. Se intenta reducir plazos de entrega en la cadena de suministro, para así invertir más tiempo en el diseño y la generación de valor.
– En general, durante todo el proceso se tiende a postergar la toma de decisiones de diseño lo máximo posible, intentado generar varias alternativas bien detalladas que aseguren resoluciones correctas. Esta estrategia constituye una herramienta en sí misma, llamada diseño basado en conjuntos, que se explica más abajo.
– Suministro preciso. Este paso se da cuando los procesos y productos están definidos para ser detallados, fabricados y entregados.
– Fabricación y logística. Constituye la charnela entre fabricación y montaje.
Todo este proceso se gestiona a través del control de la producción y la estructuración del trabajo. El esquema incluye también la conexión entre proveedor y cliente.
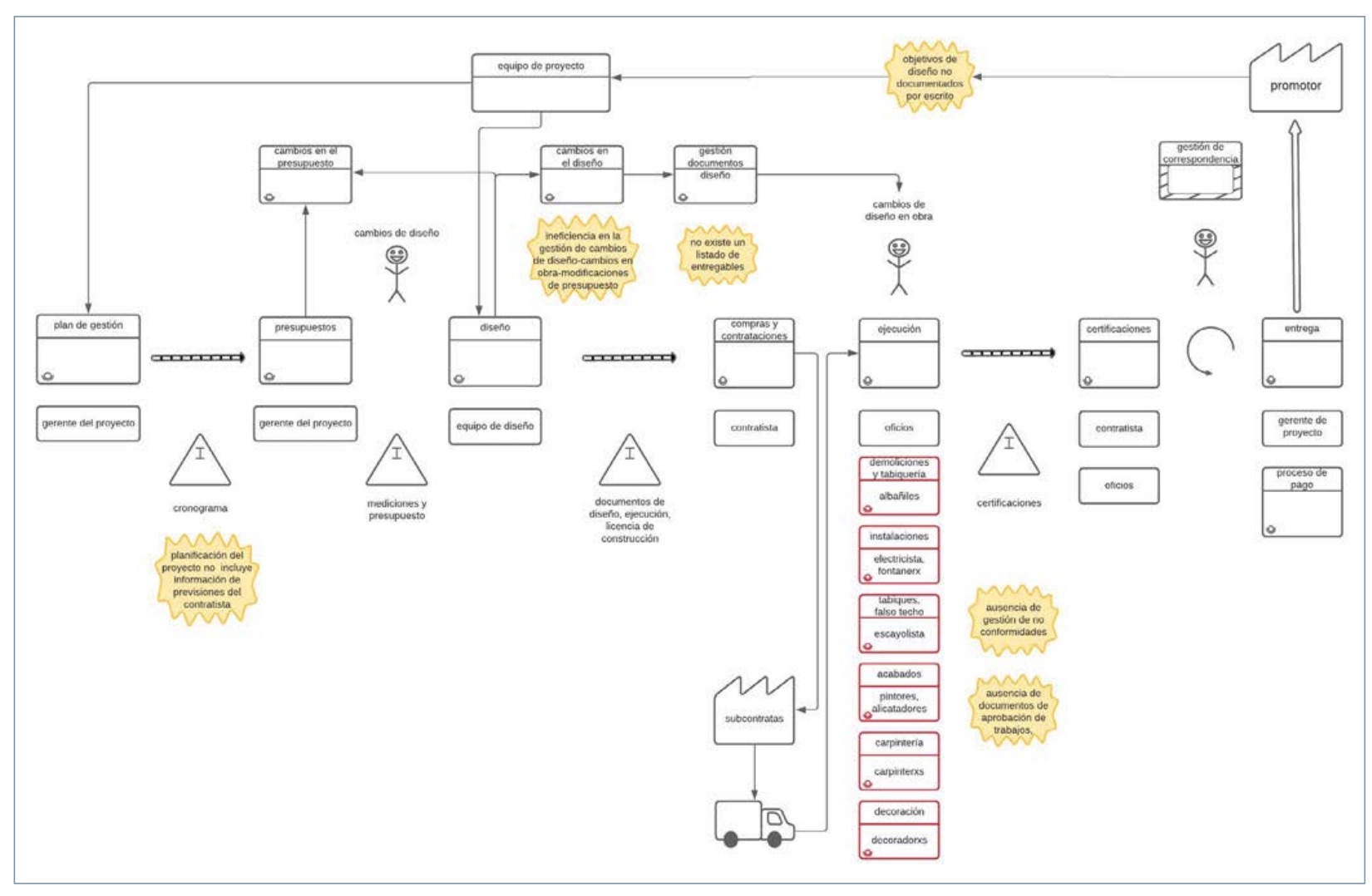
Entrega integrada de proyectos
Se origina como una actualización de la herramienta anterior basada en la colaboración entre los diferentes actores que forman parte del proyecto con la intención de anular metas individuales a favor de un único objetivo, alcanzar el valor.
Para que el proyecto integrado suceda, todos los integrantes deben cumplir con una serie de principios (3).
– Respeto mutuo y confianza.
– Beneficio mutuo y recompensa.
– Innovación colaborativa y toma de decisiones.
– Participación temprana de actores clave.
– Definición temprana de objetivos.
– Planificación intensificada, mejorar resultados de diseño.
– Comunicación abierta.
– Tecnología apropiada, entrando en juego otras herramientas como BIM.
– Organización y liderazgo, roles claramente definidos.
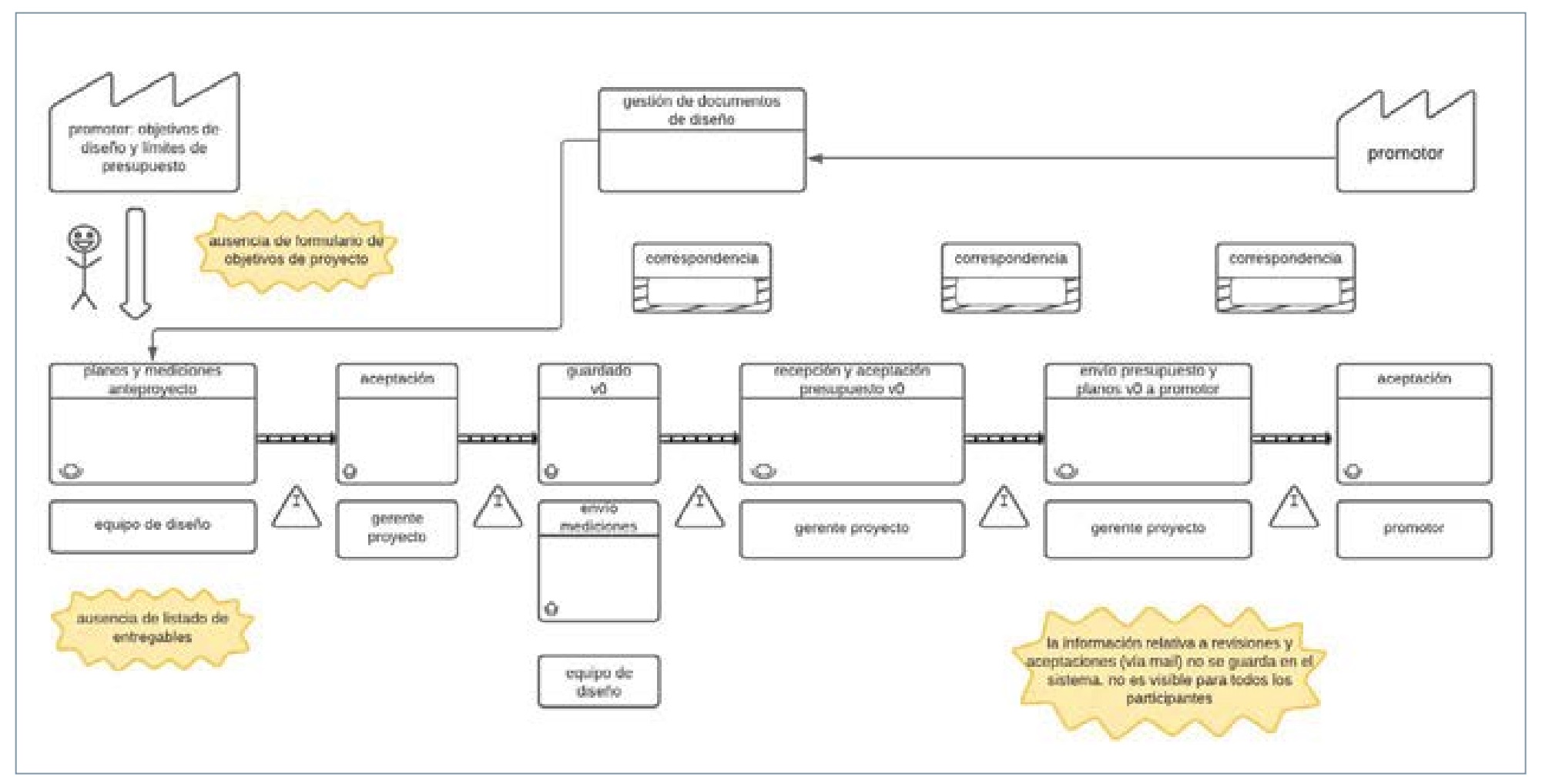
Coste objetivo
Basado en los principios fundamentales de pensamiento esbelto, busca establecer contacto con el cliente para especificar el valor y partiendo de esta base, mejorar el flujo.
Se ejecuta en la fase de diseño y es una herramienta clave del sistema del último planificador en su fase “definición de proyecto” (3).
El proceso se inicia fijando el precio en función de aquello que crea valor para el cliente. Se calcula entonces el coste permitido, que no es otra cosa que el precio de venta menos el margen de beneficio. Es interesante recordar que el valor se especifica en función de las necesidades del cliente (interno y externo), pero también de la empresa. Por ello, si el coste de producción es mayor que el permitido se deben establecer ciertas mejoras.
Sistemas de información en construcción (SIC)
Plataforma indispensable para la colaboración en el diseño y la construcción del proyecto. Actúa como base de datos para todos los participantes, permitiendo gestionar la instalación más allá del momento constructivo. Se constituye como un recurso efectivo durante todo el ciclo de vida de la instalación. Forma parte del ya citado sistema de entrega de proyectos integrados.
Sus principales características son (5):
– Mejorar flujo de comunicación, transparencia.
– Coordinación de la secuencia de trabajo.
– Mayor aporte de visualización para mejorar la comprensión del proyecto.
Además, sirve de gran ayuda en los procesos de modificación. Estos se llevan a cabo de forma ágil y eficaz. Reduce el despilfarro en forma de variabilidad (aquella que no aporta valor), mejorando el flujo de trabajo y la calidad.
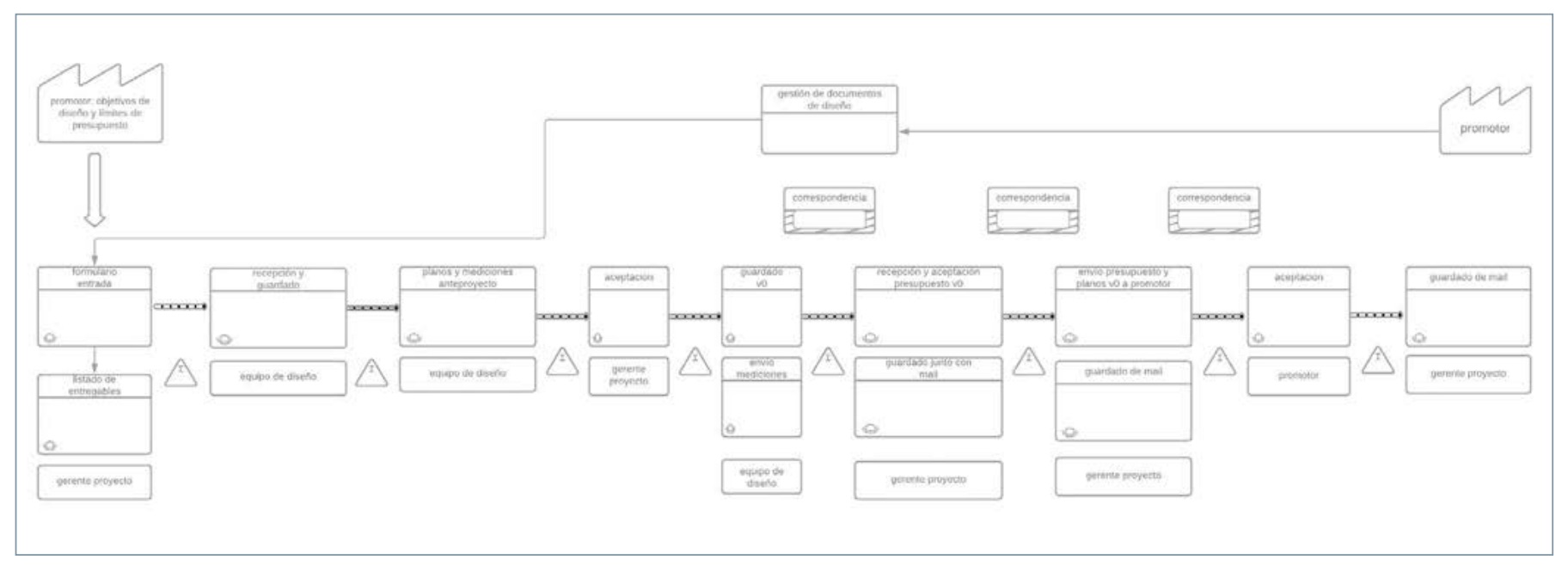
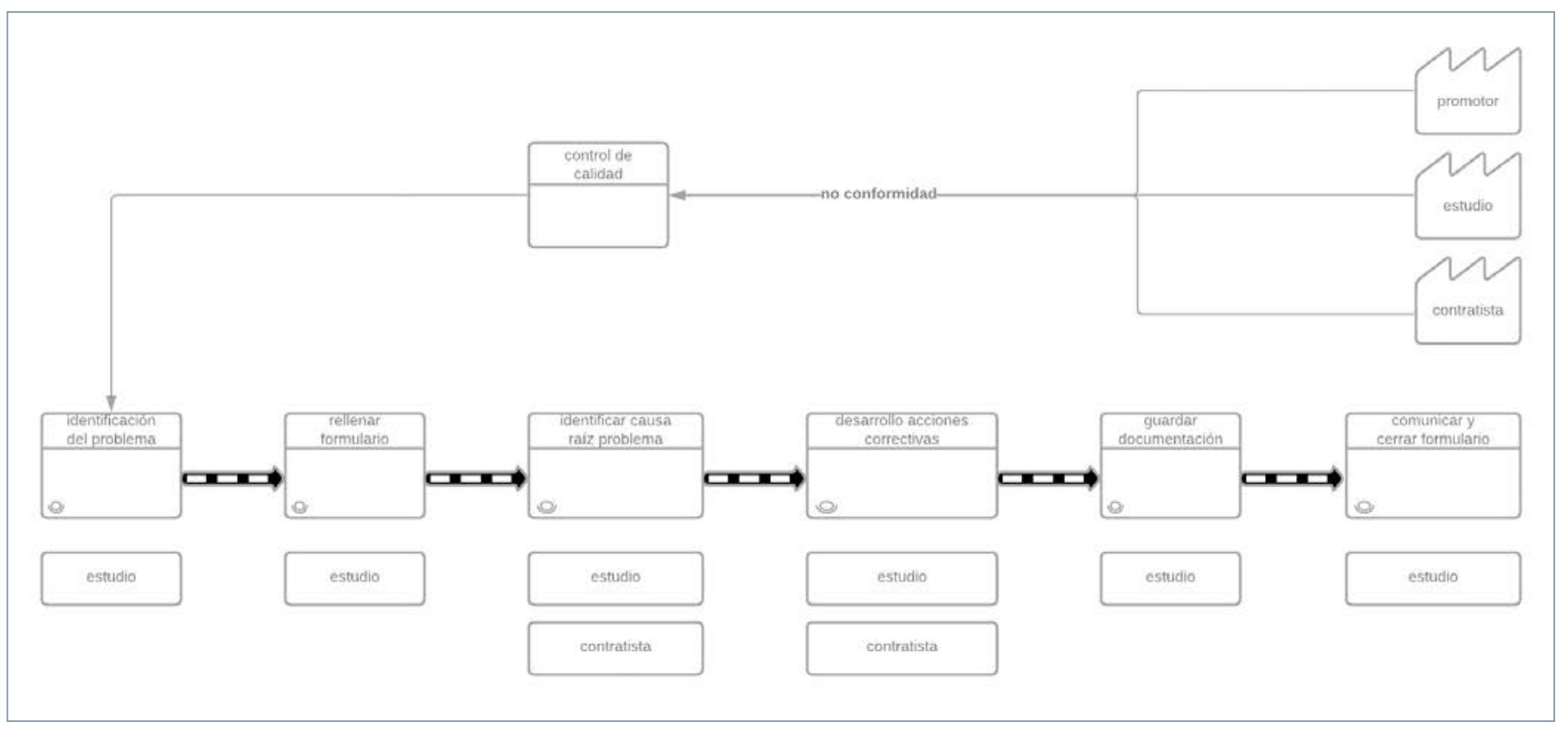
Diseño para el desmontaje (DPD)
Se trata de un proceso de diseño cuyo objetivo es reducir el consumo de recursos y la producción de residuos durante la construcción y el reciclaje de los edificios. Su intención es la de cerrar ciclos de materiales, reduciendo despilfarros y el considerable impacto ambiental de la construcción.
Como teoría se basa en tres conceptos fundamentales (6):
– Los ciclos de materiales. Actualmente, la construcción se basa en ciclos lineales, se consumen recursos y se generan residuos. El objetivo es poder reutilizar y reintegrar estos residuos en algún punto del ciclo, cerrándolo.
– La jerarquía del reciclaje.
– Identificar las capas del edificio.
Se busca construir de un modo más racional, abierto e industrializado, facilitando la división y recogida de los residuos, favoreciendo su valoración y diseñando no solo la construcción, sino también el desmontaje de los edificios.
Diseño basado en conjuntos
Sistema definido por Ward en 1995. Considera que generar varias alternativas muy detalladas para un diseño mejora la capacidad de análisis y ayuda en la toma de decisiones.
Siempre se ha considerado este hecho un desperdicio de tiempo. La práctica habitual pasa por tomar decisiones de diseño tempranas cuando las alternativas no están bien definidas, pero, de nuevo, Toyota ha revelado que esta práctica no es la más eficiente.
Mapa del flujo de valor
Se trata de una técnica gráfica que, mediante el empleo de iconos normalizados, integra en una misma figura flujos logísticos de materiales y de información. Se utiliza para mostrar qué actividades añaden valor y cuáles no, detectando oportunidades de mejora. Puede utilizarse como herramienta de planificación y control, como herramienta de diagnóstico y también como herramienta de comunicación.
Informe A3
Debe su nombre al papel de tamaño 420 × 297 mm, estándar ISO según el que Toyota lleva a cabo sus comunicaciones de proyectos de mejora continua. Se trata de un método para la formulación de propuestas y un medio para las comunicaciones aprobadas.
Técnica a prueba de errores
Son dispositivos a prueba de errores, impiden que se fabriquen productos defectuosos deteniendo los procesos cuando detectan situaciones anormales. De este modo, evitan el riesgo del error humano, tanto en los ejercicios de control como de ejecución.
Gestión visual
Ligado al principio de la transparencia, permite que todos los trabajadores participantes del flujo de valor tengan acceso a la información de forma actualizada. Datos de interés como los objetivos de producción diarios, la tasa de defectos y cómo afecta el trabajo realizado a la calidad del producto final son las mejoras establecidas.
Se consigue una mayor estabilidad y predictibilidad de los procesos, menos esfuerzo en las labores de gestión, mayor conciencia de los problemas y oportunidades de mejora y sensibilidad a los problemas.
Un ejemplo de este tipo de instrumentos es el llamado “Andon”, término japonés que indica alarma. Consiste en una serie de indicadores visuales o señales utilizados para mostrar el estado de producción.
5S
Consiste en mantener orden y limpieza en las áreas de trabajo, eliminando así la fuente de accidentes, improductividades, costes, defectos de calidad y pérdidas de tiempo. Los principales beneficios son obtener puestos de trabajo más eficientes y proyectores de una imagen más cuidada.
El nombre responde a los términos japoneses: Seiri, Seiton, Seiso, Seiketsu y Shitsuke, utilizados para definir las cinco fases de la técnica:
– Despejar: eliminar elementos innecesarios.
– Organizar: aquellos calificados como necesarios, asignándoles un lugar que evite movimientos innecesarios, esperas, defectos o condiciones inseguras.
– Limpiar y realizar actividades básicas de mantenimiento e inspección de máquinas, herramientas, materiales y del entorno de trabajo.
– Estandarizar y sistematizar los pilares anteriores de modo que no tenga lugar un retroceso a estados de desorganización, suciedad, desorden y excesos.
– Disciplinar y consolidar: hacer de las disciplinas anteriores un hábito.
Obeya Room
Término japonés que significa “habitación grande” o “habitación de guerra”. Pretende eliminar barreras entre departamentos, potenciando el principio de transparencia a todos los niveles. Consiste en la reunión de todas las partes implicadas en el desarrollo de un producto o proceso, facilitando la comunicación y la toma rápida de decisiones.
Tormenta de ideas
Técnica de grupo que pretende encontrar una solución a un problema específico mediante la generación espontánea de ideas originales en un ambiente relajado.
Diagrama Ishikawa
Tiene como objetivo el análisis de problemas y sus soluciones. Se trata de una representación gráfica compuesta por un alinea horizontal al que llegan líneas que simbolizan las principales causas de un problema. A su vez, a estas llegan otras líneas con causas secundarias.
Cambio de matriz en menos de 10 minutos
Se utiliza para la reducción de tiempos de cambio de referencia o de actividad, permitiendo más flexibilidad de los procesos y una menor generación de stocks, así como el acoplamiento de la actividad del proceso a la demanda del cliente.
Mantenimiento productivo total (MPT)
Sistema de gestión del mantenimiento, que busca la mejora continua de la maquinaria y el logro del cien por cien de eficiencia de los procesos de producción, una reducción de las inversiones necesarias en ellos y un aumento de la flexibilidad del sistema productivo, involucrando a todo el personal de la organización.
Kanban
Significa “señal” en japonés y, dependiendo de las aplicaciones, puede ser de diferentes tipos: tarjetas, carros vacíos, etc. Su objetivo es que los procesos aguas abajo se activen cuando el cliente interno emite la señal pertinente. En definitiva, son herramientas que potencian el principio de tracción.
Construcción esbelta
Según el Grupo Internacional de la Construcción Esbelta, fundado en 1993 (3), “La construcción esbelta es un enfoque basado en la gestión de la producción para la entrega de un proyecto, una nueva manera de diseñar y construir edificios e infraestructuras. La gestión de la producción esbelta ha provocado una revolución en el diseño, suministro y montaje del sector industrial. Se aplica a la gestión integral de proyectos, desde su diseño hasta su entrega. La construcción esbelta se extiende desde los objetivos de un sistema de producción ajustada (maximizar el valor y minimizar los desperdicios) hasta las técnicas específicas, y las aplica en un nuevo proceso de entrega y ejecución del proyecto”.
Obstáculos
El primer obstáculo a la hora de implementar la metodología esbelta es la falta de conocimiento de esta y sus beneficios por parte de los participantes, seguido este de la necesidad de cambio en la forma de pensar de todos los participantes de la organización, la confianza de los trabajadores en propietarios y gerentes que nace del compromiso y la transparencia. Otras cuestiones son la dificultad para alinear los intereses de las diferentes partes, así como la impresión generada en algunos trabajadores de que absorbe demasiado tiempo cuando se realizan tareas cuyo aporte de valor no es inmediato y/o concreto.
Para entender los obstáculos específicos de la industria de la construcción es necesario reparar en qué la diferencia de las operaciones de producción industrial.
Lauri Koskela (4) establece tres peculiaridades fundamentales de la industria de la construcción:
– Es un proyecto de edificación que tiene naturaleza única o prototípica.
– Es algo único que cada vez se ejecuta en un lugar diferente.
– Se llevará a cabo por una multiorganización de carácter temporal, que en cada lugar necesitará medios y recursos diferentes y propios de cada zona.
En 2007 añade dos características:
– Los edificios comparten con los barcos y los aviones la característica de que, durante el proceso de ensamblaje, son demasiado grandes para moverse a través de las estaciones de trabajo, de modo que son hechos manteniendo un emplazamiento productivo fijo.
– Por otra parte, los edificios y puentes están diseñados para un lugar específico tanto técnica como estéticamente.
Esta última observación recuerda un concepto original (en el sentido de origen, como bien entiende Gaudí) de la arquitectura. El emplazamiento como contexto para el diseño, el punto de conexión entre arquitectura y urbanismo, paisaje. Se trata de una cuestión a menudo olvidada en la búsqueda de construcciones más eficientes en términos de tiempos y costes, y se cae en la estandarización y la modulación, procesos que salen fuera de los límites del territorio “arquitectura” y se acercan peligrosamente al de la producción industrial.
Entendidas las diferencias, y la idiosincrasia de la arquitectura, es posible acercarse a ella desde un punto de vista esbelto. La situación de partida es la inexistencia de la fábrica como sistema diseñado, es necesario llevar a cabo una planificación única e irrepetible para cada prototipo. La planificación es la línea de producción de la industria de la construcción. La complejidad en resolver esta reside en gestionar adecuadamente las interacciones entre actividades evitando el desperdicio.
Proceso de construcción esbelta
Cwik, Nowak, & Roslon postulan en 2017 (7) un sistema de construcción esbelta dividido en tres planos (objetivos, principios y procesos) que se desarrollan a continuación.
Plano sistémico de objetivos
Partiendo de la base de que el objetivo es el cliente, y este, cualquier proceso resultado de una acción de empuje. Se fijan en función de este objetivo una serie de metas parciales.
– Eficacia
– Claridad en la definición de los procesos de construcción, como la posición y las competencias de los empleados en la organización del proyecto, el diseño de las herramientas de monitorización y la introducción de métodos de visualización que hagan partícipes a los trabajadores en obra.
– Flexibilidad por parte de los participantes en el proyecto para garantizar la pronta implementación de los medios de control en los correspondientes procesos.
– Estabilidad en la implantación de los procesos.
Plano sistémico de principios
Al ser los principios de la construcción esbelta herederos de los de la producción esbelta, hay que tener en cuenta algunas cuestiones:
– Hacer ver a los trabajadores el carácter combinatorio del término valor desde la perspectiva del cliente, distinguiendo entre actividades asociadas al aumento de valor, actividades de desechos ocultos y actividades no ocultas de residuos.
– Necesidad de fomentar la centralización de la generación de valor.
– Potenciar el trabajo en equipo y, por tanto, el vínculo entre los empleados.
– Garantizar una representación sólida de las cuadrillas de trabajo a través del principio de empuje.
Plano sistémico de procesos y métodos
A continuación, se resumen los procesos que aplicar en la construcción esbelta:
– Gestión orientada a procesos de campo.
– Producción continua, necesidad de establecer cronogramas semanales y llevar a cabo reuniones periódicas. Este proceso se lleva a cabo mediante el sistema de último planificador diseñada por Glenn Ballard en 1994 (9). Debe ir acompañada de un medio de visualización que permita discutir determinadas cuestiones en el lugar de trabajo, no solo los plazos, sino también la limpieza, el orden y la calidad de los resultados.
– Control redefinido como “resultado de monitorización”, comunicado a través de los ya citados medios de visualización y capaz de obtener predicciones realistas de las fases de proyecto.
– Centralizar el objetivo de generar valor para el cliente a lo largo de todo el proyecto mediante la descentralización de la toma de decisiones. Todos los empleados son conscientes de los resultados de monitorización; con la información adecuada todos pueden tomar decisiones oportunas
– Coordinación a través del método de empuje y el flujo continuo.
– Elección de elementos modulares y prefabricados cuando sea posible para reducir actividad en el lugar de trabajo.
– Entregas justo a tiempo.
– Mejora continua de un proyecto a otro.
Objetivos y delimitaciones de la metodología
El objetivo del presente artículo es el desarrollo de una metodología esbelta capaz de establecer un plan de mejora en los procesos de diseño y construcción de reformas en edificios de viviendas.
Conocidos los objetivos, principios y procesos de esbeltez aplicados al sector de la construcción, se establecen una serie de objetivos específicos razonables para el caso de estudio.
– Identificar los procesos que componen el proyecto.
– Seleccionar aquellos sobre los que aplicar una determinada herramienta.
– Analizar la situación presente de estos procesos.
– Identificar desperdicios evitables y, con ello, los puntos que mejorar.
– Definir un plan de acción que corrija estas cuestiones en el futuro.
Simplificando, la metodología pretende analizar el desperdicio y su procedencia en la situación presente y elaborar un plan de acción que lo evite y, a su vez, que permita alcanzar mayores niveles de valor.
Metodología
Resolver el primer objetivo específico requiere de la elaboración de un mapa conceptual que defina las acciones llevadas cabo por cada integrante de la organización y sus colaboradores. A partir de esto es posible delimitar un proceso y una herramienta ejemplares para el resto del proyecto.
La detección de aquellas acciones que generan desperdicio y son evitables ve su correspondencia en la herramienta denominada mapa de flujo de valor (MFV). Esta es propia de la industria manufacturera lo que implica que para aplicarla a la industria de la construcción es necesario llevar a cabo algunas adaptaciones. La principal será la selección de una etapa de construcción. El MFV se realiza en el contexto de una planta industrial y con respecto a una familia de productos. Generalmente, se tiende a seleccionar aquella familia de productos con el mayor volumen de producción. En este caso, se seleccionará un proceso específico, el más complejo, que permita acotar un intervalo temporal.
El MFV se basa en el concepto de flujo de valor, es decir, todas aquellas acciones que forman parte del proceso en el que un producto es llevado a su consumidor final. Como herramienta analítica es imprescindible a la hora de permitir una comprensión global de los procesos llevados a cabo por la organización, detectando posibilidades de mejora. Además, constituye un medio de visualización simple, capaz de hacer partícipes a todos los miembros que toman parte del proceso.
La razón principal por la cual se selecciona esta herramienta y no otra es su capacidad de análisis global. A través de ella es posible identificar necesidades que probablemente hagan entrar en acción otros procesos, ya incluidos en el primer apartado de este documento, para alcanzar el valor.
Puede ser que se detecte desorden en las zonas de trabajo y esto impida un desarrollo normal de las tareas. Si es así, el MFV estará llamando a la acción a las 5S. Si se detecta una falta de comunicación entre las partes, probablemente sea necesario implantar un sistema BIM que permita la coordinación, secuenciación y visualización de los proyectos por todos los participantes. Cuando hay problemas a la hora de tomar decisiones y las que se toman no son acertadas, nuestra compañía deberá poner en marcha un trabajo de diseño basado en conjuntos, capaz de generar varias alternativas a un mismo problema. De esta manera, se mejora la capacidad de decisión. La aplicación del MFV es un primer paso para la implantación de los principios y herramientas propios del diseño y la construcción esbeltas.
Aplicación a la mejora en los procesos de diseño y construcción de reformas en edificios de viviendas
El MFV atiende a dos momentos, el presente y el futuro. Como se especifica en los objetivos ya mencionados, primero se analiza la situación actual de los procesos seleccionados y se elabora el mapa de estado actual.
Se establecen los iconos de procesos y se relacionan a través de las flechas del flujo. Detectadas aquellas operaciones inútiles o redundantes se pasa a representar el mapa de estado futuro en el que se implementan los cambios pertinentes.
El último paso sería el de la implementación de dichos cambios y el análisis de los resultados. No se puede olvidar el concepto de mejora continua, la necesidad de cambio para hacer posible el progreso, la eficiencia y el aumento de la productividad.
Flujograma
El flujograma de proyecto define de forma genérica las cuatro fases de proyecto: anteproyecto, proyecto básico, de ejecución y fin de obra. Este esquema se aprovecha para representar los actores implicados en cada etapa. El azul simboliza las tareas del promotor, el amarillo, del estudio de arquitectura, el verde la administración, el naranja al contratista, el lavanda las contratas y el gris al conjunto de todos (Fig. 1).
Esta clasificación de colores ayuda a comprender el momento cronológico de entrada de cada participante en el proyecto. A la vista de los resultados, se asume cómo el esquema actual es más parecido al propio de una construcción tradicional (Fig. 2) en la que diseñador y promotor son los únicos presentes en la totalidad del proyecto, cuando el objetivo es obtener un esquema como el que se muestra en la figura 3.
La primera conclusión sería, por tanto, la necesidad de interacción con el resto de participantes desde el inicio del proyecto, aumentando la confianza entre los integrantes y fomentando la capacidad de toma de decisiones de cada uno de ellos (con conocimiento de causa) en situaciones de conflicto. En este caso, el análisis insta a la implantación de los principios acotados por el sistema integrado de entrega de proyectos.
MFV
Se procede, tras este paso, a elaborar el mapa de flujo de valor (Fig. 4) del proyecto tipo definido por las fases anteriores. Tras su definición se detectan los siguientes puntos que mejorar:
– Los objetivos de diseño definidos por el promotor en las sucesivas reuniones no se documentan por escrito, lo que generará confusiones en el futuro.
– Dado que el contratista no entra en juego hasta la fase de ejecución, la elaboración del cronograma inicial no tiene en cuenta las previsiones reales de esta etapa.
– No hay un sistema de empuje que resuelva la gestión de cambios en obra, diseño y modificaciones de presupuesto. Los planos, las mediciones y el presupuesto no se encuentran ligados por ningún tipo de código o referencia, de modo que la correspondencia de las versiones depende de la persona encargada del proyecto en ese momento.
– No se cuenta con un listado de entregables adaptado a cada proyecto, en parte, como consecuencia de la ausencia del listado de objetivos planteados por el promotor.
– Tampoco existen protocolos de gestión de conformidades; las deficiencias son corregidas, pero no almacenadas en el sistema, de modo que no se aprende de los errores.
– Del mismo modo, los aciertos tampoco se valoran. No hay modelos de aprobación de trabajos; la validez depende del acuerdo verbal entre las partes.
A partir de la elaboración del mapa de flujo de valor, es posible continuar el análisis haciendo hincapié en aquellos puntos en los que se ha detectado desperdicio.
En este caso se muestra el ejemplo del proceso de gestión de documentos, insuficiente en el momento presente debido a cuestiones que ya se apreciaban en el MFV general y que se completa cuando se realiza un análisis más exhaustivo. Se detecta que, además de la falta de determinada documentación, hay deficiencias en la forma de archivar la correspondencia, y no es visible esta para todos los trabajadores (Fig. 5). Se apela aquí al concepto de transparencia.
Para darle solución, se elabora un modelo de gestión de documentos futuro (Fig. 6) que tiene en cuenta las deficiencias del presente:
– Elaboración de un formulario de objetivos de diseño.
– Elaboración de listado de entregables.
– Sucesivos guardados y codificaciones de archivos en el sistema.
Por otra parte, se plantea un modelo de gestión de no conformidades (Fig. 7) que almacena datos de identificación, corrección, guardado y comunicación.
Conclusiones
Los esquemas presentados son un ejemplo de empleo de la metodología basada en el análisis de MFV.
Los resultados obtenidos demuestran la eficiencia del método a la hora de detectar procesos redundantes o susceptibles de ser mejorados. Los diagramas aquí presentados responden al análisis de determinadas etapas y procesos, pero es posible aplicarlos a la totalidad del proyecto. Además, los resultados de su aplicación no son definitivos y deben revisarse tantas veces como sea necesario de cara a alcanzar la perfección.
El análisis realizado manifiesta la necesidad de elaborar formularios y documentación específica para determinados procesos. Con todo y como se planteaba en uno de los apartados, la solución del problema de comunicación entre las partes estará en la aplicación de un modelo BIM. No obstante, esta clase de implantación implica grandes inversiones en la formación de los participantes, quienes han de confiar en el proceso.
El análisis MFV es un primer paso para labrar la confianza de los participantes e iniciar el camino hacia una construcción más eficiente y responsable.
Referencias
(1) Womack, J.P. & Jones, D.T. (1997) Lean Thinking— Banish Waste and Create Wealth in your Corporation, Journal of the Operational Research Society, 48:11, 1148.
(2) Bautista, M., (2016). Propuesta de aplicación de Lean Construction a través de un sistema Kanban, en un estudio de arquitectura. Recuperado de https://riunet.upv.es:443/handle/10251/59858
(3) Lezana Pérez, Emilio Achell Pons, J. F. (2014). Introducción a Lean Construction. Fundación Laboral de La Construcción. Retrieved from www. fundacionlaboral.org
(4) Koskela, L., Howell, G., Ballard, G., & Tommelein, I. (2007). The foundations of lean construction. Design and Construction, (January 2014), 211– 226. https://doi.org/10.4324/9780080491080
(5) Latorre Uriz, A., Sanz, C., Sánchez, B., (2019). Aplicación de un modelo Lean-BIM para la mejora de la productividad en redacción de proyectos de edificación. Informes de la Construcción, 71, 313.
(6) Martin Goñi, Paula & González Barroso, José Maria & Rey, Albert. (2014). The ‘design for disassembly’, a Lean methodology. 10.13140/ RG.2.1.1442.6721. (7) Cwik, K., Nowak, P., & Roslon, J. (2017). Introduction to Lean Construction. Warsaw.