Análisis, diseño y fabricación del prototipo de la máquina de vapor Cornish
Analysis, design and manufacture of the Cornish steam engine prototype
María Pérez Viedma (1), Rafael López García (2), Eloisa Torres Jiménez (3), Rubén Dorado Vicente (4), Alberto García-Collado (5)
Resumen
Este trabajo enmarcado en el ámbito de la historia de la ingeniería mecánica y de las máquinas y mecanismos trata de ahondar en el principio de funcionamiento de la máquina de vapor tipo Cornish con una descripción de la misma, los componentes implicados y sus peculiaridades. Dicho principio de funcionamiento incluye el análisis termodinámico teórico que describe su ciclo de vapor. Así mismo, se ha llevado a cabo un análisis mecánico en uno de los elementos con la finalidad de conocer más en profundidad algunos parámetros y las fuerzas a las que estaba sometido dicho elemento. Por otra parte, se ha reconstruido un prototipo de la maquinaria a escala mediante diferentes tipos de tecnologías y materiales. Para esta reconstrucción, el modelo ha sido diseñado con un programa CAD para una mejor visualización del resultado final.
Palabras clave: Máquina de vapor, ciclo termodinámico, CAD, impresión 3D, prototipado rápido
Abstract
This work in the field of the history of mechanical engineering and of machines and mechanisms tries to delve into the principle of operation of the Cornish type steam engine with a description of it, the components involved in it and their peculiarities. This principle of operation includes the theoretical thermodynamic analysis that describes its vapor cycle. Likewise, a mechanical analysis has been carried out in one of the elements in order to know more in depth some parameters and the forces to which said element was subjected. On the other hand, a prototype of the machinery has been rebuilt to scale using different types of technologies and materials. For this reconstruction, the model has been designed with CAD program for a better visualization of the final result.
Keywords: Steam engine, thermodynamic cycle, CAD, 3D printing, rapid prototyping
Recibido / received: 05/06/2021. Aceptado / accepted: 06/10/2021.
1 Estudiante de Ingeniería Industrial, Universidad Jaén, Jaén, España
2-5 Departamento de Ingeniería Mecánica y Minera, Universidad Jaén, Jaén, España
Autor para correspondencia: Eloísa Torres Jiménez; e-mail: etorres@ujaen.es
Doi: 10.23800/10512
Introducción
Este artículo se centrará en la primera máquina de vapor que fue instalada en la provincia de Jaén con óptimos resultados, empleada principalmente en el desagüe de las minas y que contribuyó al inicio de la revolución industrial de la comarca [1].
La actividad industrial más productiva de la provincia de Jaén era la extracción de plomo de las minas ubicadas principalmente en Linares, La Carolina y El Centenillo. El verdadero problema de las minas siempre había residido en los elevados costes de producción, que eran muy superiores a los grandes productores internacionales. Los costes de producción, por razones tecnológicas, se iban incrementando proporcionalmente a la profundidad de excavación y, por consiguiente, también aumentaba el problema de desagüe de la mina. Por tanto, para solucionar ese problema, se instaló en 1849 la primera máquina de vapor, que dio óptimos resultados. Su destino fue las minas de Pozo Ancho. Esta máquina era de cilindro vertical y balancín tipo Cornish.
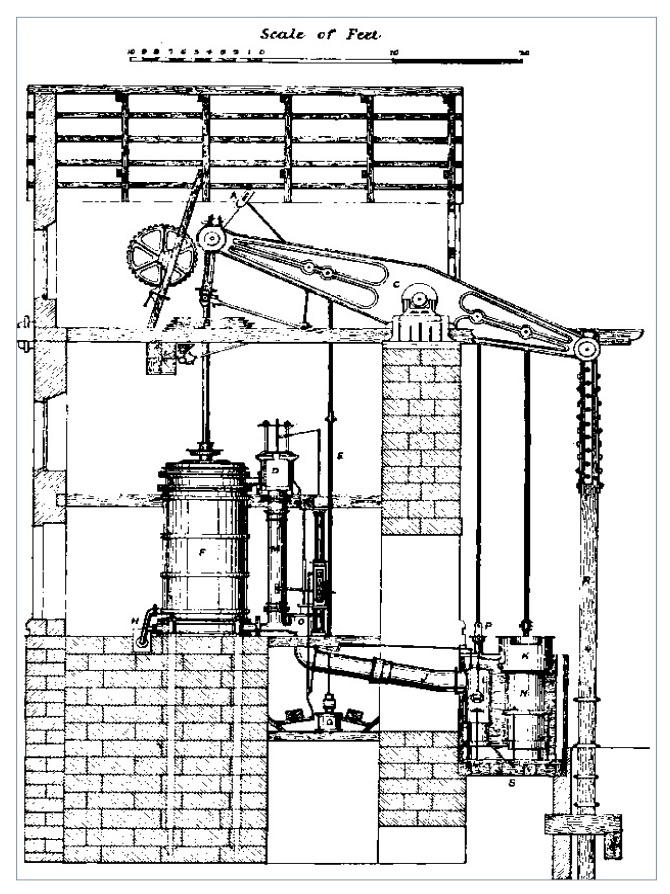
Las máquinas de vapor tipo Cornish surgieronen Cornwall (Inglaterra) de donde proviene su nombre. Su misión principal era la de bombear agua de las minas de la zona. Este tipo de máquina surgió a partir del año 1800, cuando la patente de James Watt acababa y también surgió debido al alto precio del carbón de la zona. Estos hechos propiciaron los cambios realizados en las primeras máquinas de vapor de Watt para aumentar su rendimiento y así reducir la cantidad de carbón necesaria para el desagüe de las minas [2].
La principal característica de este motor es el uso de vapor de alta presión, así como la disminución de la pérdida de calor al aislar las tuberías, cilindros y calderas de estas máquinas. Sin embargo, lo que produjo un aumento en el rendimiento del motor fue el cierre de la válvula de admisión de vapor a mitad de carrera, lo que permitía la expansión del vapor hasta una presión más baja, mientras que en los motores diseñados por Watt el vapor era admitido a lo largo de toda la carrera con una presión no muy superior a una atmósfera o dos. Hay otras modificaciones significativas como la disposición del condensador y las calderas [3][4].
Las diversas modificaciones descritas anteriormente que se hicieron en la máquina de vapor en Cornwall produjeron una potencia a un coste menor debido al ahorro en carbón que dichas modificaciones suponían, lo que convirtió esta máquina en una gran revolución debido a su economía.
Elementos principales
Los diferentes elementos que componen la máquina de vapor Cornish se pueden ver en la figura 1:
A: Pieza de retención fijada a la parte superior de la viga por medio de soportes.
B: Bloques; la pieza de retención toca estos bloques y se detiene el pistón. Previene, así, cualquier daño hacia el cilindro por una carrera más larga.
C: Viga principal; el extremo interno es de 16 pies 6 pulgadas y el externo, de 13 pies y 3 pulgadas de largo.
D: Boquilla superior.
F: Cilindro.
G: Gobernador de la catarata.
H: Tubería conectada al cilindro desde las calderas, que se ubicaban en otra casa.
J: Tubo de educción, la palabra educción proviene de educir, que significa sacar una cosa de otra. Es decir, sacar el vapor del cilindro para, posteriormente, ser vertido en el condensador.
L: Condensador.
M: Tubería de equilibrio.
N: Bomba de aire.
P: Bomba de alimentación del émbolo.
R: Vástago.
Y en relación con la zona ampliada D de la figura 2:
B: Cubierta (no separa la cámara E-E como puede pensarse del dibujo; se proporciona un paso ininterrumpido del vapor hacia la cámara).
E: Tapón o varilla de empuje que permiten el funcionamiento de las válvulas y la catarata.
D: Boquilla superior.
F: Válvula de vapor. El vapor llega desde la válvula de regulación atravesando la cámara E-E. El vapor pasa hacia el cilindro a través de esta válvula.
G: Válvula de regulación que regula la admisión de vapor en la cámara E-E.
H: Paso (el vapor atraviesa este paso cuando la válvula de vapor (F) y la de regulación (G) están abiertas.
J: Puerto de vapor.
K: Válvula de equilibrio, situada en la mitad de la boquilla.
M: Tubería de equilibrio.
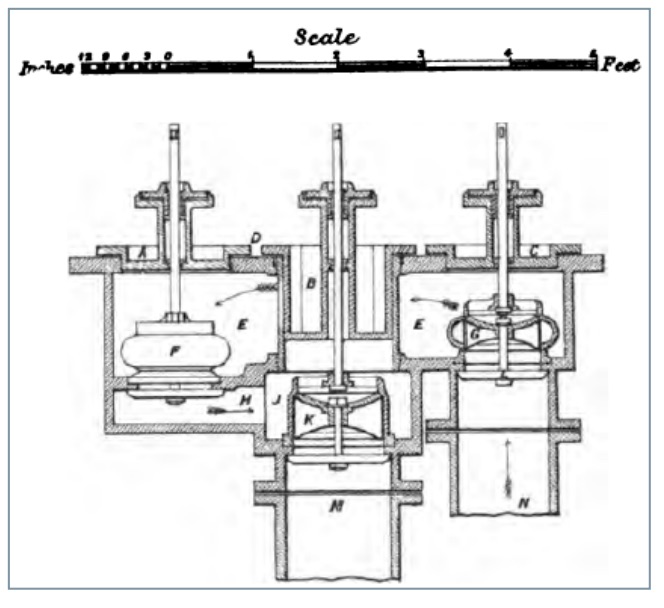
Principio de funcionamiento
Se supone la maquinaria en el punto de comienzo de su carrera descendente, es decir, con el pistón en reposo en la parte superior del cilindro y con la generación de vacío por debajo del mismo.
Estando la válvula de regulación abierta con una apertura fija, regulada manualmente por la su manivela por los operarios, el puerto superior comienza a llenarse con vapor elástico procedente de las calderas.
A partir de las suposiciones anteriores, la válvula de vapor se abre y el vapor atraviesa el puerto superior hasta alcanzar la parte superior del cilindro. En consecuencia, el pistón comienza lentamente su descenso y el vapor continúa fluyendo hacia el cilindro mientras la válvula de vapor permanezca abierta.
Una vez que ha entrado la cantidad de vapor suficiente, que dependerá de la presión a la que este se encuentre y su poder de expansión, la válvula se cierra para evitar cualquier entrada de vapor adicional en el cilindro. De esta forma, la comunicación entre el cilindro y la caldera se corta. El vapor continúa ejerciendo presión sobre el pistón por su propia fuerza y comienza a expandirse, por lo que aumenta su volumen y disminuye su presión. A medida que esto ocurre, la fuerza ejercida por el pistón comienza a asemejarse a la resistencia al movimiento de este ejercida por el vástago principal y el conjunto de bombas asociadas al mismo. En este punto, el pistón puede vencer la resistencia al movimiento debido a la energía cinética que en este punto tiene el pistón. Esta energía se gasta, por tanto, en vencer la resistencia y, por ello, comienza a frenar su velocidad descendente hasta llegar al final de la carrera. La energía cinética acumulada se debe al excedente de la misma al comienzo de la carrera. El cierre de la válvula de vapor está accionado por la cataratay, de esta forma, se regula la cantidad de vapor que se introduce en el cilindro.
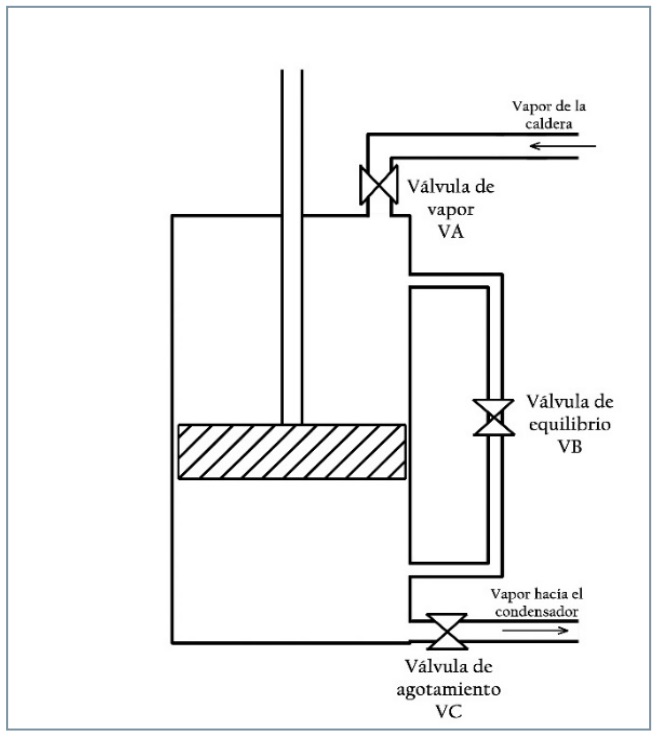
Cuando la carrera descendente está llegando a su final y el pistón ha descendido casi hasta el fondo de su recorrido, un empujador presiona una empuñadura inferior, conectada a los puertos de las válvulas, y realiza así tres operaciones. En primer lugar, ejecuta el cierre de la válvula de agotamiento que se ha mantenido abierta durante todo el recorrido del pistón. En segundo lugar, cierra la válvula de inyección y detiene la entrada de agua en el condensador. Y, en tercer y último lugar, abre la válvula de equilibrio. En algunas ocasiones la válvula de equilibrio se abre mediante la adición de una nueva catarata, como ejemplo la maquina Cornish en Old Ford. Este hecho, sin embargo, no era algo común.
La abertura de la válvula de equilibrio pone en comunicación la parte superior e inferior del cilindro y, en consecuencia, la presión a cada lado del pistón tiende a igualarse y entrar en equilibrio; de ahí el nombre de dicha válvula y de la tubería de equilibrio. Debido, por tanto, al cambio de presión en la parte superior al cilindro, esta presión ya no puede vencer la resistencia ejercida por el vástago y las bombas y, por ello, el pistón se desplaza en dirección ascendente.
Durante el ascenso del pistón, el vapor pasa gradualmente de la parte superior a la parte inferior del cilindro, a través de la válvula de equilibrio, y llena el vacío que deja el pistón tras él. Cerca del final de esta carrera ascendente, una varilla acciona de nuevo la válvula de equilibrio y esta se cierra para el comienzo de una nueva carrera descendente.
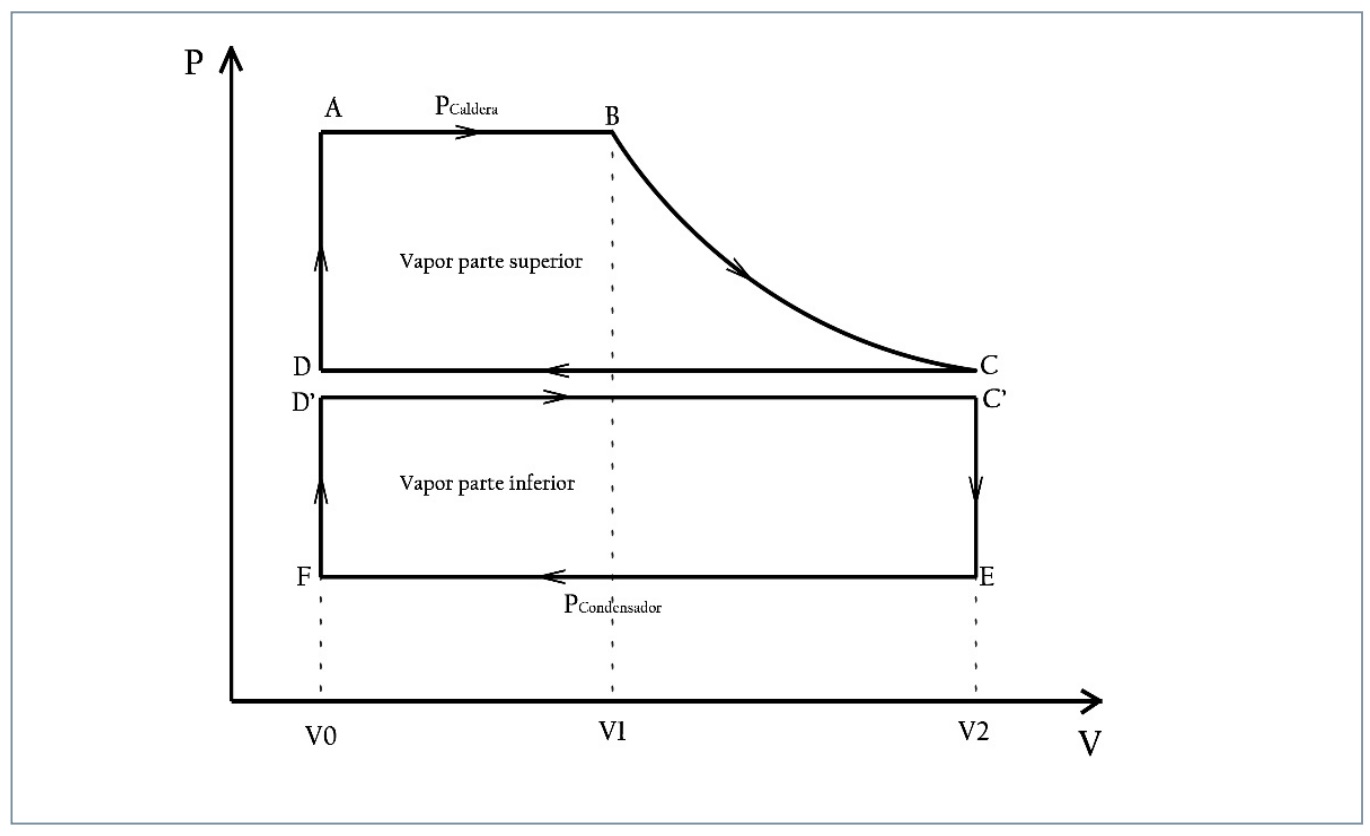
En el mismo periodo mencionado anteriormente, el vapor se precipita al condensador, lo que genera un vacío debajo del pistón. La precipitación del vapor hacia el condensador se consigue con la ayuda de la bomba de aire situada contiguamente al condensador, ya que esta propicia el vacío necesario.
Por otra parte, esta carrera descendente del pistón produce la carrera ascendente del vástago principal de la maquinaria que lleva acopladas una serie de bombas para ejecutar la principal misión de la maquinaria, la extracción de agua de la mina.
Estas bombas llevan acoplados una serie de émbolos que, en la carrera ascendente del vástago, son capaces de succionar agua de la mina. Para que la extracción de esta cantidad de agua sea completa, hay unas válvulas antirretorno que imposibilitan la devolución de agua a la mina. En la carrera descendente del vástago, el émbolo presiona el agua succionada y, al encontrarse con las válvulas antirretorno, esta agua encuentra su camino en una tubería que también tiene una válvula que la deriva de forma ascendente hacia un depósito superior. Este conjunto de embolo, válvulas y tuberías se denomina bomba aspirante e impelente [4][5].
Los depósitos solían estar separados entre 30 y 40 metros, aunque era muy común encontrarlos separados de 70 a 80 metros. En el fondo del pozo se excavaba un foso de 5 a 10 metros donde se acumulaba el agua [3].
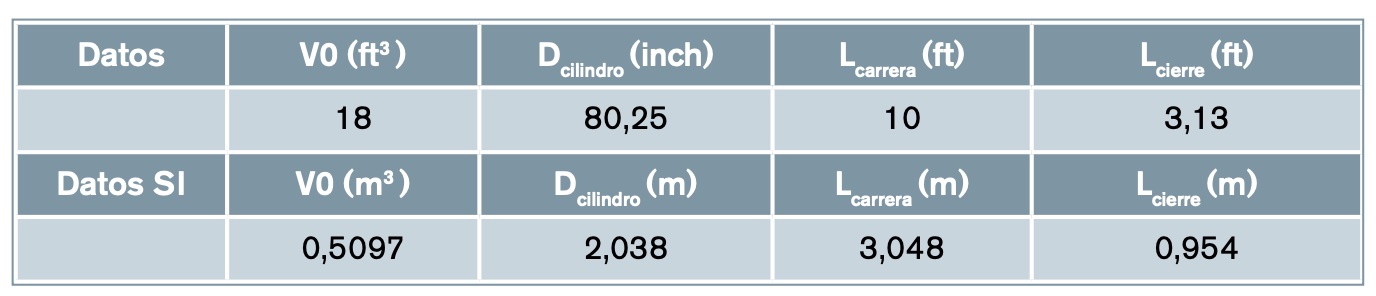
Ciclo termodinámico de la máquina
Debido a las peculiares características de admisión de vapor en la máquina de vapor Cornish, se puede determinar que se producen dos ciclos termodinámicos simultáneamente, uno en la cara superior del pistón y otro en la cara inferior del mismo, como se refleja en la figura 3.
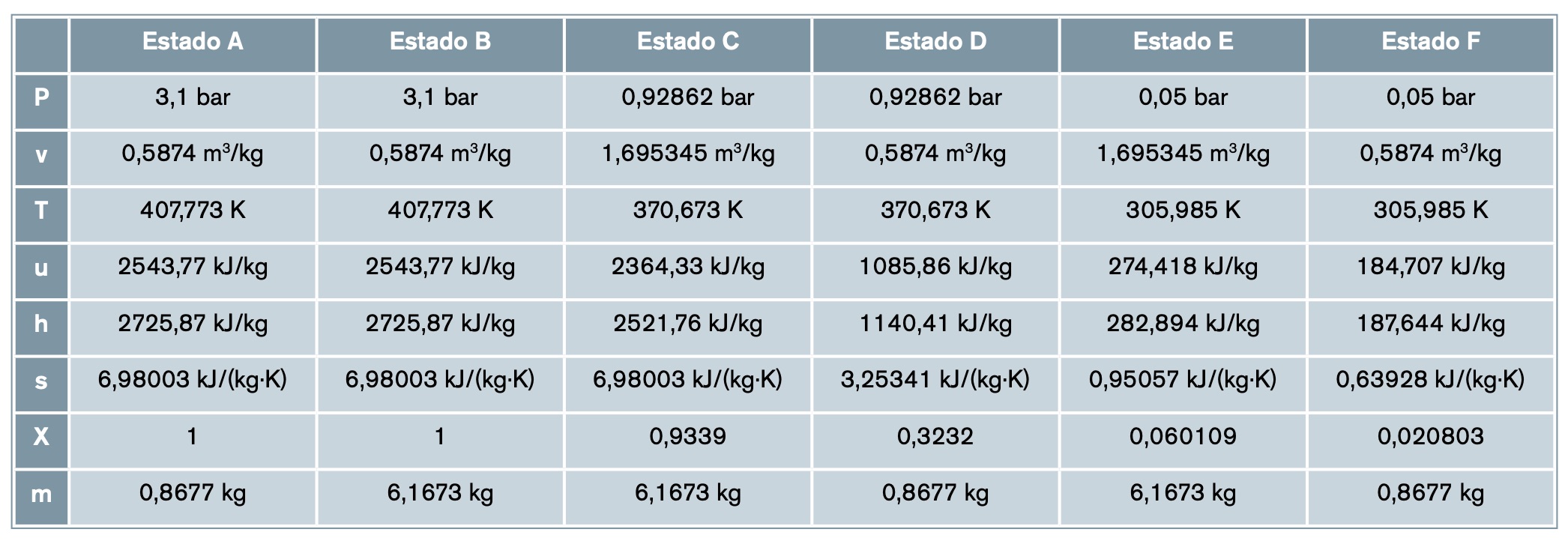
Comenzaremos la descripción del ciclo termodinámico en el punto A para la cavidad superior y simultáneamente en el punto E para la cavidad inferior con la ayuda del esquema simplificado del sistema de válvulas de la figura 4. En estos puntos del ciclo termodinámico la válvula de admisión de vapor VA está abierta, la válvula de equilibrio VB, cerrada y la válvula de agotamiento VC, abierta. En la cámara superior del cilindro tiene lugar, por tanto, la trasformación A-B, en la que se admite vapor proveniente de las calderas al cilindro a presión constante (Pcaldera). Sin embargo, en la cámara inferior el vapor está saliendo del cilindro hacia el condensador a presión constante (Pcondensador) siendo esta la transformación E-G.
Al llegar al punto B del ciclo termodinámico, la válvula de admisión de vapor VA se cierra y origina la expansión del vapor de la cámara superior de forma adiabática mientras el pistón continúa su carrera descendente, transformación B-C. El resto de válvulas permanecen en la misma posición (VB cerrada y VC abierta). En la parte inferior del cilindro sigue saliendo vapor a Pcondensador, ya que la válvula de agotamiento sigue abierta, transformación G-F.
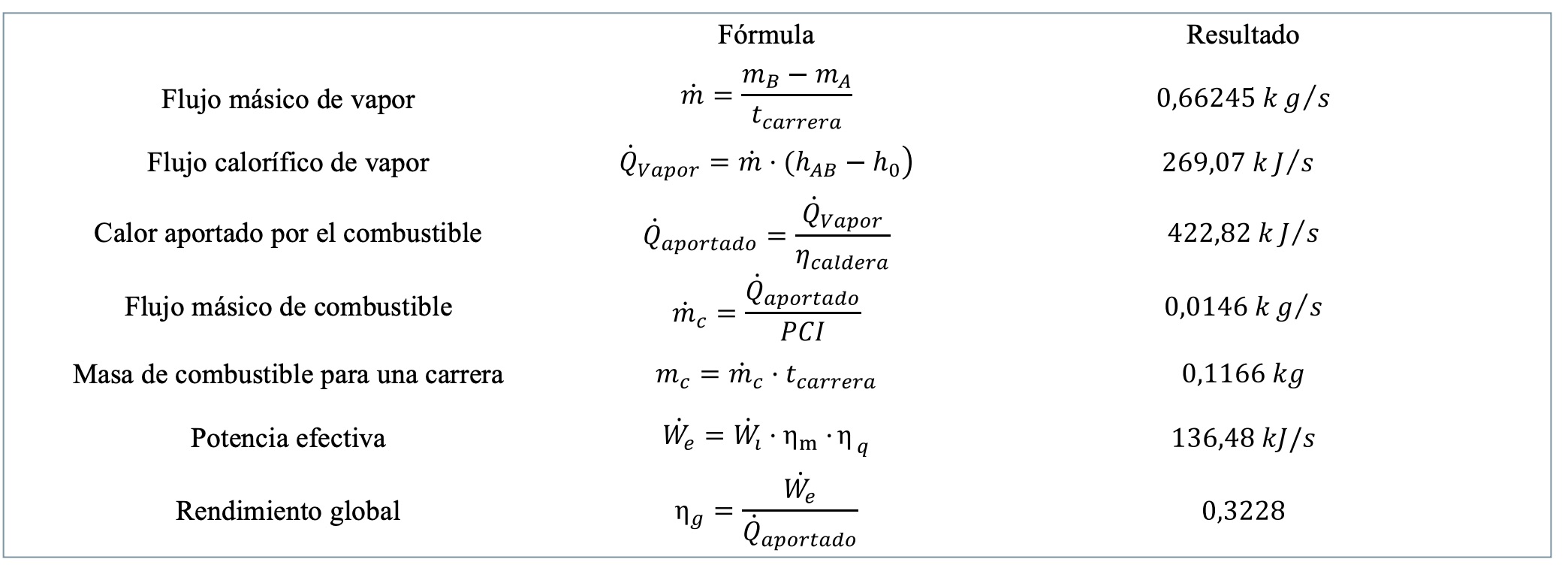
Una vez que el pistón ha descendido por completo, se abre la válvula de equilibrio VB y se cierra la válvula de agotamiento VC mientras la válvula VA se mantiene cerrada. Esto sucede en los puntos C y F, respectivamente. Se equilibran las presiones de ambas cámaras por el cambio de posición de estas válvulas, lo que causa una subida instantánea de la presión en la parte inferior del cilindro hasta alcanzar la presión de la cámara superior Pmedia; en la cámara superior la presión se mantiene, ya que esta es mucho mayor, transformación F-D’ del ciclo de la cavidad inferior y punto C en el ciclo de la cavidad superior.
Cuando ambas cámaras se encuentren conectadas por la abertura de la válvula de equilibrio, la subida de presión en la cámara inferior hace que el pistón comience a subir mientras VA y VC se mantienen cerradas, transformación C-D y D’-C’. El pistón se eleva durante su carrera ascendente y la cámara superior va disminuyendo su volumen a presión constante, desalojando el vapor de la cámara superior que pasa hacia la cámara inferior del cilindro. En la cámara inferior, el volumen aumenta hasta V2.
Al llegar a los puntos D y C’, se cierra la válvula de equilibrio VB y se abre la admisión de vapor a través de la válvula VA y, simultáneamente, la válvula de agotamiento VC, lo que origina un aumento instantáneo de la presión del vapor de la parte superior del cilindro hasta la Pcaldera, transformación D-A. En la parte inferior del cilindro, al abrir VC la presión cae instantáneamente hasta la Pcondensador (transformación C’-E).
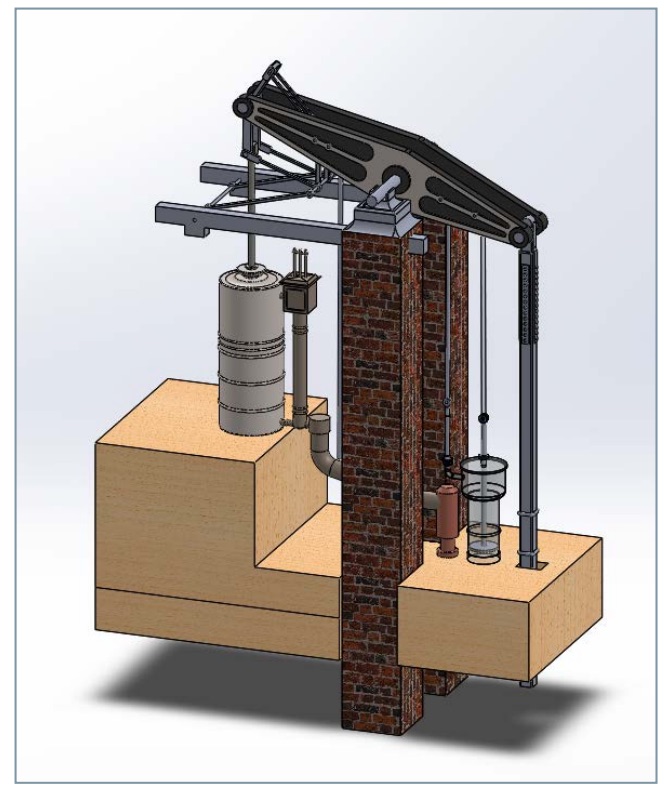
Análisis del ciclo
Con la comprensión del ciclo descrito, se ha procedido a un análisis termodinámico a partir de los datos iniciales de la tabla 1. En primer lugar, se calculan los volúmenes principales del ciclo, descritos anteriormente teniendo en cuenta el valor V0 aportado como dato, así como el diámetro del cilindro, la longitud de carrera del pistón y la longitud que recorre antes del cierre de la válvula de admisión, todo ello extraído de la bibliografía y de la máquina tomada como referenFigura 3. Ciclo teórico de la máquina Cornish. cia. También se tiene en cuenta que la presión del vapor procedente de la caldera se va a tomar como 45 libras por pulgada cuadrada que equivale a 3,1 bares [4].
Se ha realizado un cálculo de propiedades de todos los puntos del ciclo termodinámico para el que se ha usado la herramienta TermoGraf, simulador termodinámico, y se han obtenido los datos reflejados en la tabla 2.
Tras la obtención de estos datos, se han calculado una serie de parámetros bastantes importantes (tabla 3) como el flujo másico del vapor a partir de la duración de una carrera completa del pistón (8 segundos), el flujo calorífico que llega desde la caldera y el calor aportado por el combustible teniendo en cuenta el rendimiento de la caldera. A partir de este dato se puede extraer el flujo de masa de combustible necesaria y, tras ello, y teniendo en cuenta la duración de una carrera, se obtiene la cantidad de masa necesaria para la misma.
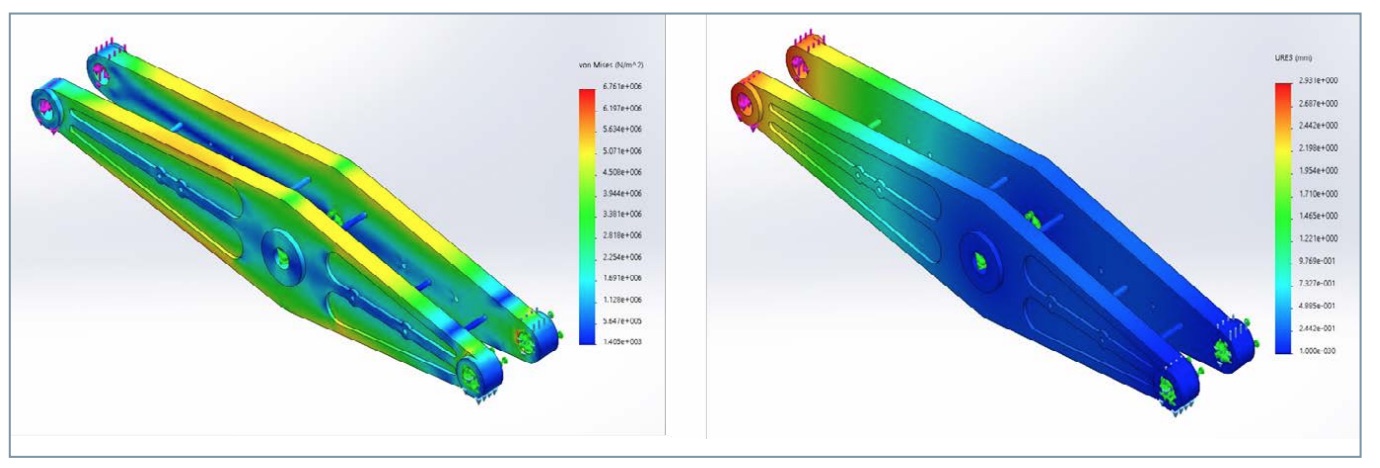
A continuación, se ha calculado el trabajo efectivo que proporciona la máquina térmica, que depende del rendimiento mecánico de la maquinaria y del trabajo proporcionado por la máquina térmica. A este último se le denominará indicado, que, multiplicado por el rendimiento mecánico y de calidad que se han establecido como 0,6 y 0,9, respectivamente, se obtendrá el trabajo efectivo y también la potencia efectiva del conjunto. Finalmente, se puede calcular el rendimiento global del motor térmico con los datos ya calculados. Este rendimiento global será la relación entre la potencia efectiva desarrollada por la máquina y el flujo de calor aportado por el combustible en las calderas. Se establece, por tanto, que el rendimiento global del motor térmico con las suposiciones realizadas es del 32,28%, dato estimado.
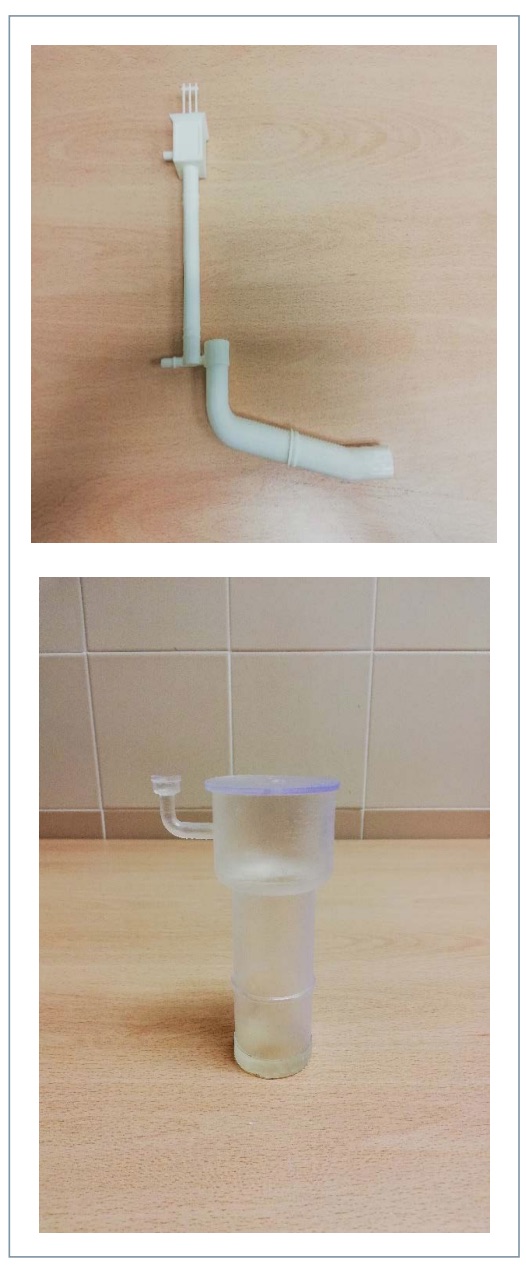
Modelado tridimensional de la máquina y análisis mecánico
El modelado tridimensional se ha realizado a partir del desarrollado en trabajos anteriores [1], modificando y creando algunos mecanismos y piezas del conjunto para adaptarlo a los nuevos datos que se han obtenido durante la investigación de la máquina. Para se ha utilizado ello el software tridimensional SolidWorks. La modificación más importante se ha hecho sobre las barras del movimiento paralelo de Watt. Este conjunto de piezas ha sido estudiado con detenimiento, ya que la posición de las mismas y sus medidas determina la eficacia y verticalidad del movimiento del mismo, y se obtiene el modelado que se puede ver en la figura 5.
A continuación, se realiza un estudio mecánico, mediante SolidWorks, en algunos de los elementos tridimensionales diseñados más significativos de la maquinaria, para comprender cómo se comportaban con las fuerzas que soportaban.
Se considerará el análisis estático más desfavorable. Este es al final de la carrera descendente del pistón, cuando el balancín se encuentra momentáneamente en equilibrio y haciendo uso de la presión obtenida al final de la carrera descendente del pistón, ya que en este punto el momento ejercido por la fuerza del vapor se puede igualar al momento que produce la fuerza opositora, y calculando el área del cilindro, se puede calcular la fuerza ejercida por el vapor y, a partir de esta y haciendo uso de la igualdad de momentos, se puede extraer la fuerza opositora.
A partir de estas fuerzas se ha hecho un estudio estático de esfuerzos sobre el balancín y se han obtenido propiedades del sólido, tensión de Von Mises, desplazamientos resultantes y deformación unitaria equivalente. Los resultados se pueden ver en la figura 6.
Modelo real a escala
A continuación, se detallan algunos aspectos importantes tenidos en cuenta para llevar a cabo la fabricación del prototipo, así como los elementos que se han adquirido para ello.
La escala elegida para la fabricación del modelo es de 1:25. Se eligió esta por adaptarse a las dimensiones requeridas por el pistón, del cual se hablará más adelante. Con el uso de esta escala también se consigue que el tamaño del modelo sea el adecuado para poder visualizar con mayor detalle la maquinaria. La tecnología usada para su creación ha sido la fabricación aditiva, y se ha usado la deposición de hilo fundido, así como la estereolitografía. También se han usado métodos convencionales de fabricación como el mecanizado por abrasión o por arranque de viruta.
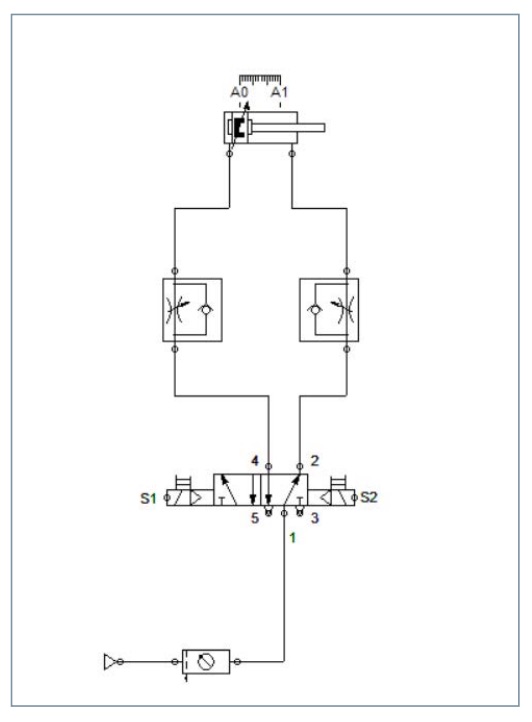
Materiales y tecnología
Para la deposición de hilo fundido se han usado dos materiales distintos, PLA y fibra ONYX (compuesto por nailon y reforzado con fibra de carbono). Por tanto, para la impresión de piezas también se han usado dos máquinas distintas. Con fibra Onyx® se ha fabricado el balancín, en dos partes, ya que las dimensiones de la pieza impidieron hacerlo en una sola. Se han diseñado dos pestañas para asegurar la sujeción de ambas partes tras ser pegadas y evitar posibles problemas derivados de este corte. El hecho de que esta pieza posea diferente material reside en la rotura de una parte de otra pieza igual pero impresa con PLA. A partir de esta segunda fabricación se ha observado que el cambio de material conlleva un cambio en la contracción del mismo, así como del acabadosuperficial, y este es mucho mejor en la pieza fabricada con fibra Onyx® y su correspondiente impresora [6].
Por otra parte, con la técnica de fabricación mediante estereolitografía (SLA) se ha fabricado la bomba de aire. El material utilizado, una resina fotopolimérica, al ser translúcido, permite visualizar el pistón que alberga en su interior. Ejemplos de resultados de estas técnicas se pueden ver en la figura 7.
También se han usado métodos convencionales de fabricación como el mecanizado por abrasión o por arranque de viruta. Para la fabricación de piezas como las barras del movimiento paralelo y el eje principal del balancín se han utilizado distintos materiales como aluminio y acero entre otros. Y se han usado técnicas de torneado, fresado y taladrado.
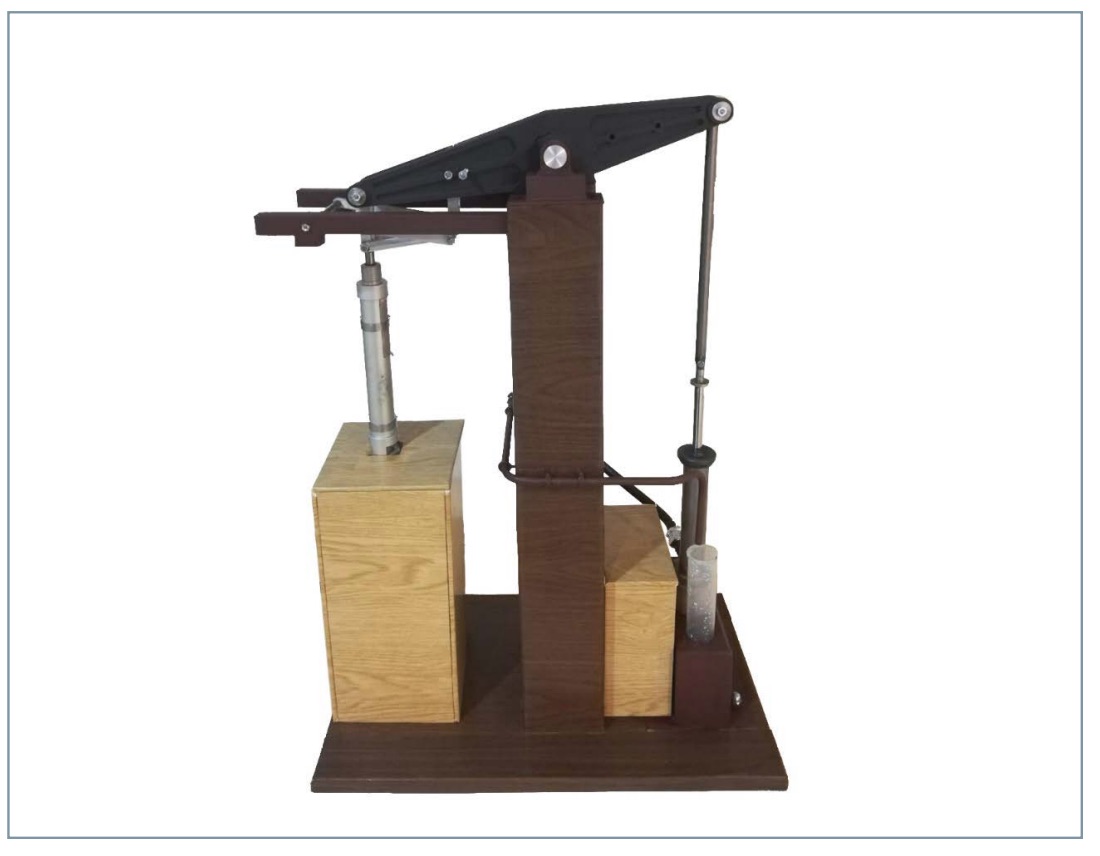
Montaje neumático
Los elementos cilindro y pistón de la máquina Cornish para el prototipo han sido adquiridos en vez de fabricados. Se ha optado por adquirir un sistema de pistón neumático accionado con aire a presión para ser automatizado y que ejecute el movimiento de vaivén que tenía la maquinaria. La selección de este elemento se ha hecho en función de la carrera del mismo, que depende de la escala que ha sido elegida. Se ha escogido el pistón con 125 mm de carrera atendiendo a criterios de similitud con la medida original.
La idea original del montaje del sistema para la recreación del movimiento fue hacerlo de forma totalmente mecánica, sin el uso de la electricidad ni otra tecnología para evitar en la medida de lo posible el uso de dichas tecnologías que no se usaban en la época para tales maquinarias. Por ello, se consideró la posibilidad de usar finales de carrera mecánicos, así como una válvula distribuidora mecánica, que desviase el flujo de aire comprimido cada vez que se accionasen dichos finales de carrera. Sin embargo, la posición del cilindro haría necesaria la colocación de estos finales de carrera por encima del pistón, lo que obligaría a la colocación de un soporte para ellos que debido al balancín que se encontraría en la parte superior y a otras piezas del mecanismo, así como el par que sufriría el final de carrera y su soporte. Este sistema es inviable para la recreación de la maquinaria, ya que su uso daría muchos problemas y obligaría a hacer una gran estructura pesada. Debido a lo anteriormente mencionado, se ha optado por el uso de una electroválvula y unos finales de carrera electromagnéticos. La principal misión de la electroválvula es la desviación del flujo de aire comprimido a las cámaras superior e inferior del cilindro para accionar, de esta forma, el movimiento del mismo. Esta desviación se ejecuta por impulsos eléctricos que le llegan a la válvula por medio de los finales de carrera o detectores magnéticos que detectan la posición del cilindro. Para el correcto funcionamiento del circuito neumático se han adquirido otras piezas fundamentales como una fuente de alimentación, reguladores de caudal y accesorios como racores o silenciadores.
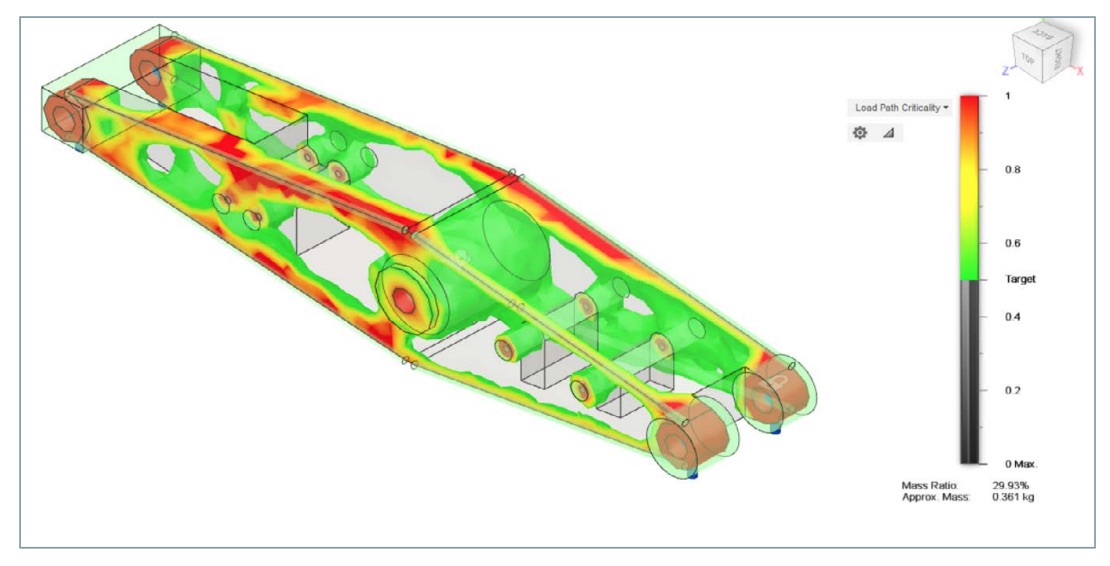
El movimiento de vaivén continuo que se produce con el esquema anterior de la figura 8 funciona de la siguiente manera: una vez que se pone el conjunto en funcionamiento mediante la admisión de aire comprimido, este pasa por la válvula distribuidora, para después pasar por el regulador de caudal. Este elemento es el encargado de la velocidad a la que el pistón cambiará de posición. Una vez que pasa el aire al pistón, este se desplaza hasta llegar a uno de los finales de carrera, en el esquema A0 y A1. Estos sensores mandan un impulso eléctrico que conecta con la electroválvula y que hacen que esta cambie de posición, lo que supone la modificación de la entrada y salida de aire al pistón. De este modo, se origina el movimiento del mismo en sentido opuesto al movimiento anterior. Esto se produce de forma continua y así se realiza el movimiento de vaivén del pistón. Para la simulación y obtención del esquema de la figura 8, se ha utilizado el programa Festo FluidSim.
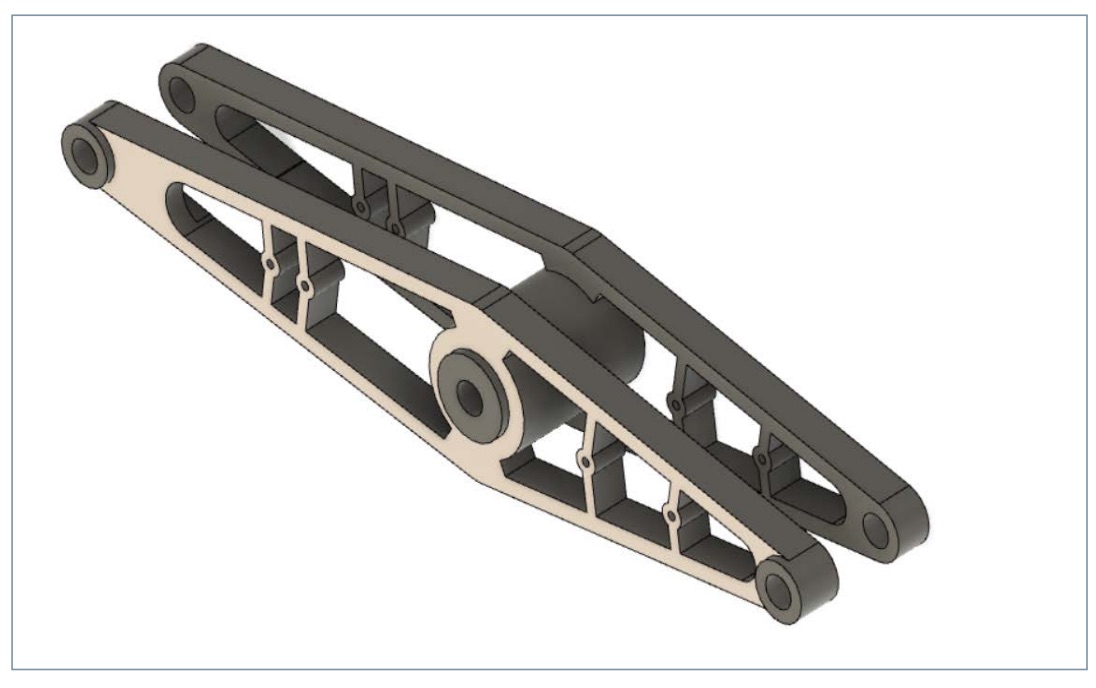
Montaje mecánico
Tras el montaje neumático y con el resto de piezas fabricadas y listas, se ha procedido al montaje mecánico.
Para realizar el montaje de las partes mecánicas del prototipo, se ha comenzado con la construcción de los pilares que son sujeción del balancín, así como de una base principal donde estos pilares están anclados. Como base se ha utilizado aglomerado, cortado a las medidas necesarias para todo el montaje del prototipo. Para los pilares, se han reutilizado vigas de madera de pallets. A estos pilares se le han hecho una cavidad para anclar las vigas de la máquina Cornish. Para conferirle mayor estabilidad a la estructura, se han atornillado dos tacos pequeños de madera como separadores entre las dos columnas. Posteriormente, se atornilla esta estructura a la base.
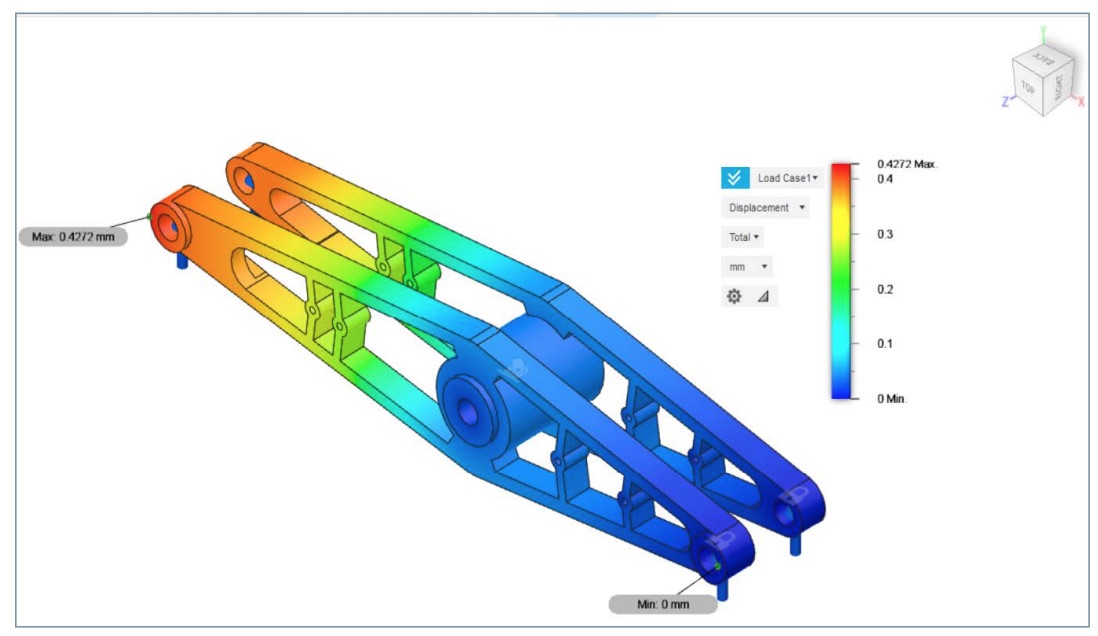
Tras esto, se ha procedido a la colocación de las piezas que son sujeción del eje principal en el que se encuentra el balancín. Fueron diseñadas con las medidas adecuadas para su colocación sobre los pilares de madera. Se han fijado con silicona y, además, estas piezas se han atornillado a la madera haciendo uso de las cavidades diseñadas previamente en dichas piezas. Con posterioridad se coloca el eje principal y el balancín; luego se instalan las vigas en las cavidades creadas para ello.
El siguiente paso que se ha dado es la colocación de las barras encargadas del movimiento paralelo. Para la unión de estas entre sí y con el propio balancín, se han usado varillas roscadas de 5 mm de diámetro. Para separar todos los elementos entre sí y que estos no cambien de posición durante el funcionamiento de la maquinaria, se han colocado pequeñas piezas a modo de separador que han sido cortadas de un tubo cuyo diámetro interior es lo suficientemente grande como para que las varillas roscadas puedan atravesarlo. A continuación, se ha colocado el pistón, ya que parte de las barras están conectadas a él. Para la colocación de este elemento sobre la base principal, se ha optado por la fabricación de una estructura metálica que proporcione la correcta estabilidad y fijación sobre dicha base. Esta estructura está forma – da por un perfil rectangular de acero. Para cerrarlo, se han soldado dos cha – pas en ambos lados del perfil. A conti – nuación, se rosca el pistón a la estruc – tura metálica y se aprieta haciendo uso de la tuerca incorporada con la compra del pistón que ejerce de contratuerca.
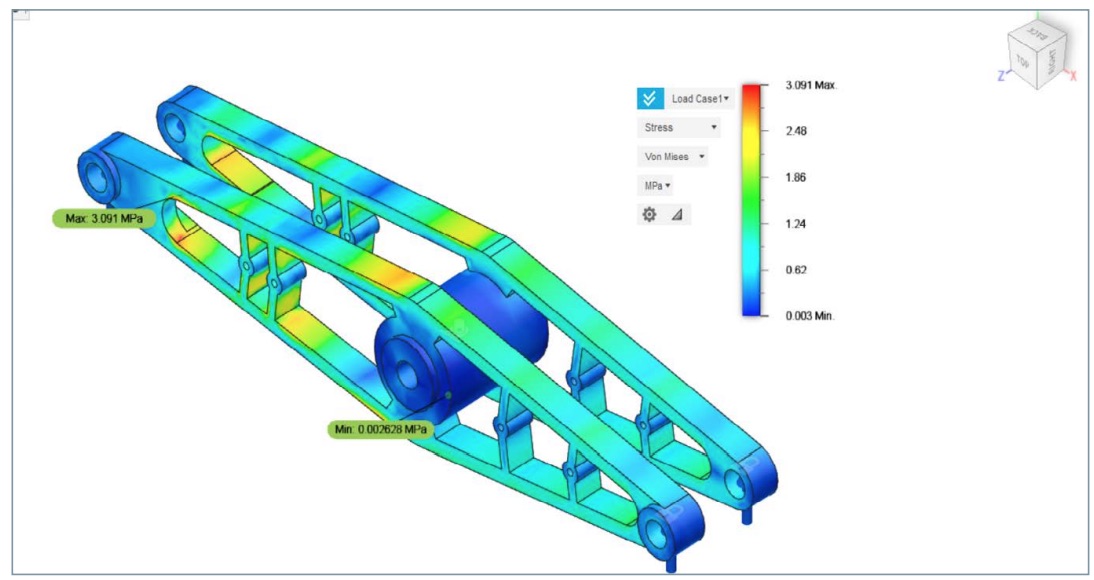
La siguiente fase del montaje pasa por la fabricación de una bomba de agua que realice las mismas funciones que las bombas impelentes que se ha – llaban en las minas donde la maquina Cornish extraía el agua, y se ha opta – do por una fabricación a partir de un amortiguador hidráulico de coche usa – do. Dicho amortiguador consta de un cilindro y un pistón, construido de tal forma que la succión de agua es posible. Para ello, ha sido necesaria la fabrica – ción de una pieza que haga de unión de todos los elementos necesarios. Di – cha bomba constará del pistón para succionar y expulsar agua, una válvula antirretorno conectada con el depósito que solo permita la succión y otra vál – vula antirretorno que solo permita la expulsión de agua. Para conectar todos estos elementos, se ha fabricado una nueva pieza que, para una unión más estanca, se ha colocado una junta tórica entre esta última pieza y el depósito. El siguiente elemento que se ha fabricado ha sido el depósito de agua. Este se ha fabricado a partir de un perfil de chapa. A este perfil se le han soldado dos cha – pas en los laterales para que se convier – ta en depósito estanco y pueda albergar líquido en su interior. El ensamblaje del pistón de la bomba de agua con el ba – lancín se hace por medio de una varilla conectada con el mismo. Aunque en las maquinas originales no se realizaban articulaciones, o no hay constancia de ello, en esta ocasión se ha optado por realizar una articulación entre la varilla y el vástago del pistón con objeto de no crear fuerzas que pudiesen perjudicar a ningún elemento de la maqueta.
Finalmente, se ha creado un pe – queño circuito por el que el líquido aspirado pasará para volver al mismo depósito y, de esta forma, evitar tener que ir rellenándolo. Una vez que se ha terminado el montaje mecánico, se ha procedido a embellecer la maqueta para un buen acabado estético.
El resultado final del prototipo se puede ver en la figura 9.
Optimización de piezas impresas
Al finalizar el montaje del prototipo y obtenerse los datos de fuerza ejercidos por el pistón sobre el balancín, se puede estimar un ahorro de material de impresión sobre algunas de las piezas con la optimización que se lleva a cabo sobre el mismo haciendo uso del programa Autodesk Fusion 360. El principal elemento al que se le ha aplicado esta simulación de optimización es el balancín, ya que se trata de la pieza con mayores dimensiones del conjunto. Para esta simulación importamos la pieza maciza, le asignamos el material y las fuerzas que soportará el balancín. La presión mínima que requiere la maqueta para su funcionamiento es de 1,5 bares, por lo que las fuerzas que soportan el balancín se estimarán a partir de este valor y teniendo en cuenta el área del pistón donde se ejerce la fuerza. Se obtienen los resultados que se pueden ver grafiados en la figura 10 [7].
Estos resultados nos indican qué zonas del modelo se deben conservar de la forma más óptima atendiendo a los parámetros introducidos, así como la criticidad de la ruta de carga a través de un mapa de colores. Así mismo, se muestra el peso aproximado del modelo y el porcentaje de material conservado.
Con dichos resultados se procede a realizar los cortes necesarios para la eliminación de material. El resultado final es el que se muestra en la siguiente figura 11.
Por último, y para asegurarnos de que la pieza ya creada soportará las cargas a la que será sometida, se ha procedido a un estudio de tensión estática con este mismo programa. Este estudio analiza la deformación y la tensión en el modelo a partir de cargas estructurales y restricciones. Según los resultados obtenidos (figuras 12 y 13), se pueden analizar e investigar diferentes parámetros como las tensiones y los criterios comunes de falla.
Se comprueba de esta forma que la optimización de la pieza no presentaría problema alguno y que se obtendría un ahorro de material total del 64,42%, ya que la pieza inicial tendría un peso de 1,158 kg y la final de 0,412 kg.
Debido a la falta de información de datos, en un primer momento no fue posible la fabricación de esta pieza de forma optimizada, ya que tras el montaje completo se pudo extraer la presión mínima a la que esta pieza funciona. Por tanto, este estudio es objeto de una posible futura mejora de la maqueta para una optimización de la misma.
Conclusiones
Este trabajo se ha desarrollado aplicando los conocimientos de diferentes áreas de la ingeniería, adquiridos durante el estudio del grado y máster universitario y, especialmente, en las áreas de fabricación, mecánica y máquinas y motores térmicos, así como del área de automática.
Los conocimientos de la ingeniería mecánica aplicados han sido muy diversos entre sí, ya que en el trabajo se ha llevado a cabo tareas de diseño y análisis de diferentes técnicas de fabricación del prototipo y de análisis termodinámico.
Con este trabajo también se ha podido profundizar en aspectos técnicos y de funcionamiento de la máquina de vapor Cornish, máquina muy importante en su fecha y que trajo con su instalación en la provincia de Jaén grandes cambios e impulsó la revolución industrial de la provincia.
Referencias
[1]M. Pérez-Viedma. Inicio de la revolución industrial en Jaén. Maquina de vapor Cornish y aplicaciones. Universidad de Jaén, 2017.
[2]R. Polwhele. The History of Cornwall, vol II, Londres, 1834.
[3]A. C. P. Arrayanes, «Proyecto Arrayanes» [online]. Disponible en: https://www.proyectoarrayanes.org/ revolucion_tecnologica.php.
[4]W. Pole. A Treatise On the Cornish Pumping Engine. Londres, 1844.
[5]C. Pamely. The Colliery Manager’s Handbook. Londres: Crosby Lockwood and Son, 1891.
[6]«Filament2Print» [online]. Disponible en: https:// filament2print.com.
[7]«Autodesk» [online]. Disponible en: https://www. autodesk.com/products/fusion-360/overview.