Reutilización y valoración de residuos vítreos de naturaleza cerámica de procedencia industrial en hormigones
Reuse and recovery of glassy ceramic waste of industrial origin in concretes
Eugenio Gómez Gómez (1)
Resumen
En la jerarquía de gestión de residuos se establecen varias opciones, y una de las preferentes es la recuperación de recursos a través de procesos innovadores que permitan impactar de forma positiva en la cadena de valor, mediante la valorización y conseguir que el residuo tenga una finalidad útil, pasando de residuo a recurso. De esta forma, se puede contribuir a fomentar una estrategia muy viable en la producción y consumo responsable, como es la economía circular, la cual está orientada al uso racional de los recursos, a fomentar la capacidad científica y tecnológica a la vez que la sostenibilidad industrial.
Palabras clave
Esmalte vítreo, residuo, economía circular, sostenibilidad, hormigón.
Abstract
In the waste management hierarchy, several options are established, and one of the preferred ones is the recovery of resources through innovative processes that have a positive impact on the valve chain, through recovery and ensuring that the waste has a useful purpose, changing from waste to resource. Thus, we can contribute to promoting a very viable strategy in responsible consumption and production, such as the circular economy, which is oriented towards the rational use of resources, promoting scientific and technological capacity as well as industrial sustainability.
Keywords
Vitreous enamel, waste, circular economy, sustainability, concrete.
Recibido/received: 06/09/2024. Aceptado/accepted: 13/10/2024.
(1) Ingeniero técnico químico. Máster en Gestión Ambiental de la Empresa por la Universidad Complutense de Madrid (UPM).
Autor para correspondencia: Eugenio Gómez Gómez. Email: eugeniogomezgomez52@gmail.com
1. Introducción
Según la Directiva 2008/98 CE y la Ley 22/2011 del Estado de España, se considera residuo cualquier sustancia u objeto que su poseedor deseche o tenga la intención o la obligación de desprenderse. Se clasifican en domésticos, comerciales, industriales, mineros y sanitarios.
Los residuos industriales son los resultantes de procesos de fabricación, trasformación, utilización, consumo, limpieza, mantenimiento generados por la actividad industrial, excluidas las emisiones atmosféricas. En la Directiva 2008/98 se establece una nueva jerarquía de residuos que los Estados miembros deben aplicar.
La opción preferente es la prevención de los residuos, seguida de la valorización en su triple vertiente de reutilización, reciclaje y recuperación energética. La última opción es la eliminación segura de los residuos en vertederos. La reutilización de residuos industriales hace posible que estos materiales sean transformados de nuevo en productos, materiales o sustancias, tanto si es con finalidad original como en cualquier otra finalidad, dando origen a la economía circular. Una vez que la industria genera un residuo, hay que preguntarse ¿cómo puede ser este residuo aprovechado? La respuesta es inmediata: el paso de residuo a recurso mediante el arte de aprovechar lo inútil.
Utilizando residuos o subproductos no solo se trata de abaratar costes, sino que también se obtiene un valor añadido de los residuos, los cuales, de otra forma, acabarían en el mejor de los casos con una gestión por gestor autorizado o por un simple abandono de estos residuos y en ambos casos su destino final es un vertedero, lo que implica una degradación ambiental.
2. Objetivos del trabajo de investigación
La investigación realizada sobre la reutilización de residuos vítreos de naturaleza cerámica es novedosa y totalmente pionera en este tipo de residuos, ya que este campo de trabajo no ha sido investigado hasta el momento. Dicho trabajo se realizó durante los años 2021 y 2022 en el Laboratorio de Materiales de la Escuela Técnica Superior de Ingenieros de Caminos Canales y Puertos de la Universidad de Cantabria (LADICIM) como tesis del autor del programa senior y dirigida por el profesor Carlos Thomas García.
El objetivo principal de este trabajo de investigación ha sido estudiar la viabilidad técnica de empleo de este tipo de residuos como sustitutivos totales o parciales de áridos finos y filler calizo en hormigones. Para alcanzar los objetivos propuestos, la investigación ha tenido dos fases de trabajo:
•Caracterización de los residuos, tanto física como químicamente, conociendo su composición cualitativa y cuantitativa y su homogeneidad.
•Ensayos con hormigones autocompactantes (HAC), utilizando el residuo vítreo como reemplazo de áridos finos en los materiales de adición. Se harán distintas dosificaciones y se caracterizarán en estado fresco y endurecido, comprobando sus características físicas, mecánicas y de durabilidad en comparación con un hormigón de control al que se denomina de aquí en adelante HAC-C.
3. Esmalte vítreo y procedencia del residuo vítreo
Un esmalte se puede definir como una masa que solidifica en forma de vidrio, mediante fusión, de composición inorgánica y fundamentalmente integrada por óxidos metálicos que se funden sobre piezas metálicas. Sus componentes principales son fritas, arcilla, cuarzo, aditivos, colorantes y agua. Todos estos componentes se muelen en molinos de bolas de esteatita y se obtiene una mezcla homogénea (barbotina) de 1,70-1,85 g/cm3 de densidad que posteriormente se aplica sobre piezas de acero y es sinterizado a 850 ºC.
El principal componente de un esmalte vítreo es la frita, la cual se puede definir como una mezcla de sustancias químicas inorgánicas (fluoro y boro silicatos) que mediante un fundido (1.300-1.500 ºC) y enfriamiento rápido se transforma en un compuesto vítreo insoluble que se presenta en forma de escamas. El residuo investigado, procede de las instalaciones industriales de fabricación de productos de menaje de cocina en acero vitrificado pertenecientes a la empresa cántabra Vinitror SAL. En estas instalaciones, el esmalte molido (barbotina) es aplicado mediante pistolas neumáticas en cabinas provistas de sistema de aspiración. Una parte de la barbotina es aplicada en las piezas a fabricar y otra es recogida por la aspiración y pasa a unos filtros de mangas que retienen las partículas en suspensión, dejando salir aire exento de partículas de esmalte. Estas partículas retenidas son las que constituyen el residuo objeto de esta investigación, en estado de polvo, que anualmente es enviado a un vertedero controlado; la cantidad de residuo generada anualmente es de 150-200 toneladas.
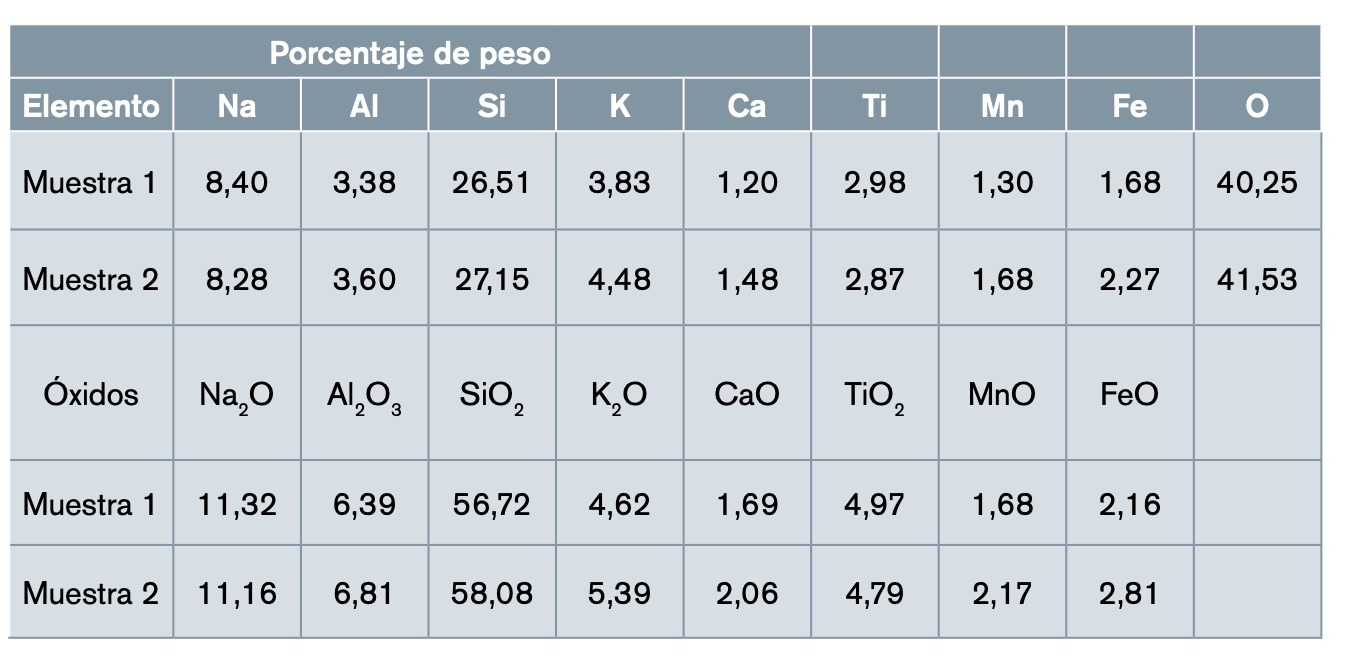
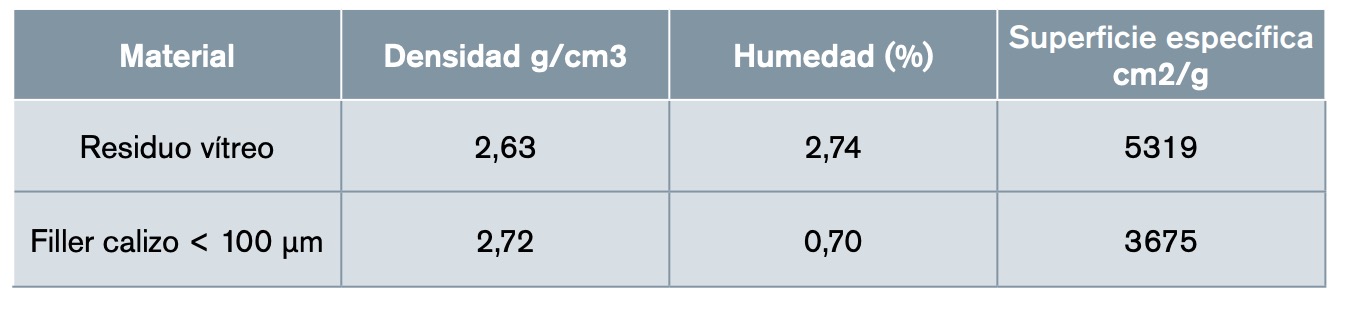
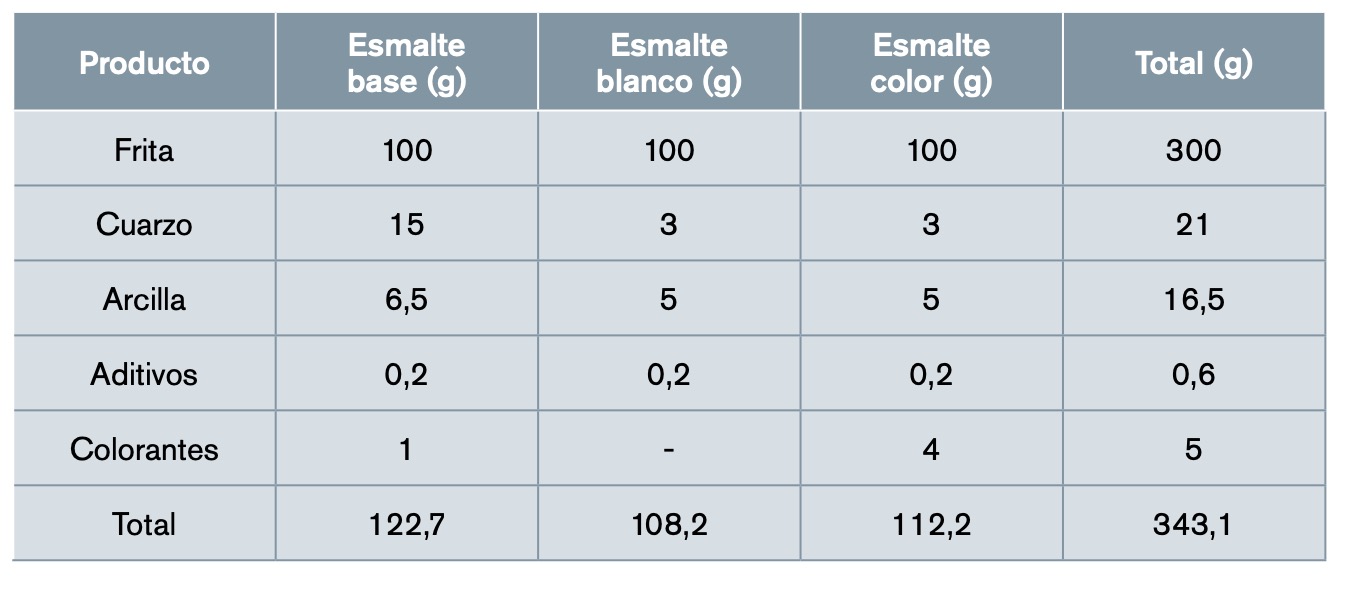
4. Caracterización del residuo vitreo
El residuo ha sido caracterizado químicamente mediante espectrometría y físicamente en los parámetros de densidad, humedad, superficie específica, cantidad de frita existente en el residuo y morfología.
4.1. Caracterización química
La caracterización química se realiza mediante la técnica denominada espectrometría de dispersión de energías de rayos X (EDX), basada en el análisis de la radiación provocada por el salto electrónico entre orbitales. La energía de los fotones emitidos está directamente relacionada con el peso atómico del elemento emisor. De este modo, se puede determinar el elemento químico por la energía de cada fotón y por el número de fotones la cantidad de cada elemento (tabla 1).
El análisis químico indica que el residuo vítreo se compone mayoritariamente de SiO2 (56-58 %) seguido de los óxidos de Na, Al, K y Fe; son minoritarios los óxidos de Ca, Ti y Mn.
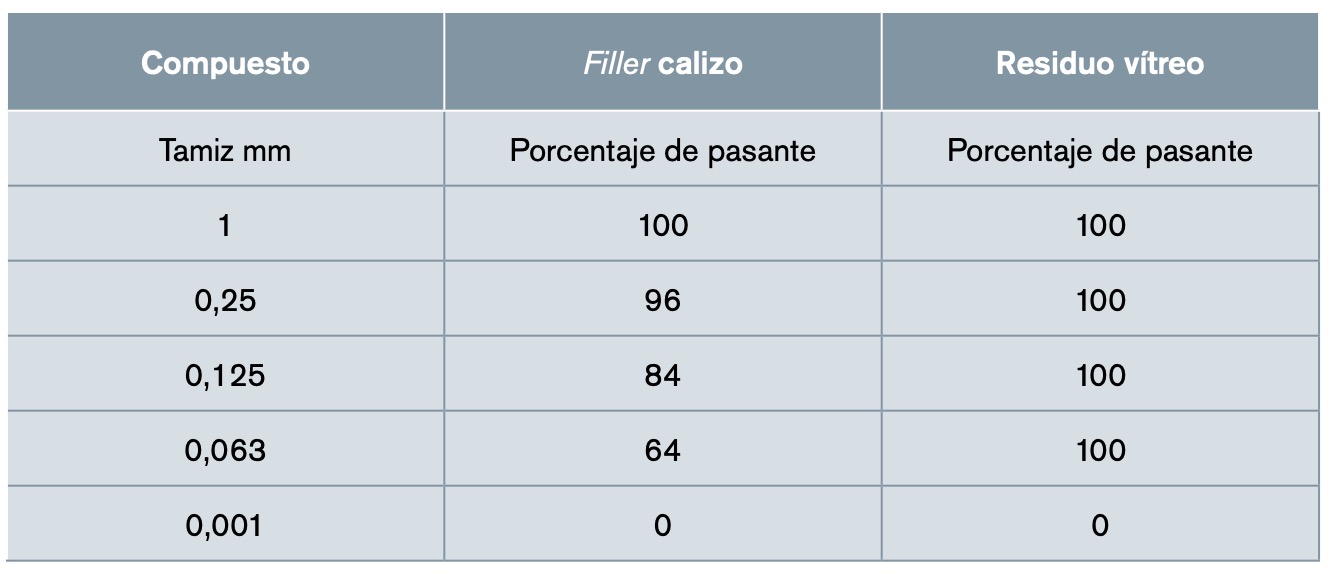
4.2. Caracterización física
Se realizan ensayos para la determinación del porcentaje de humedad, la densidad, materia vítrea existente en el residuo, la determinación de la superficie especifica y caracterización morfológica.
La determinación del porcentaje de humedad sirve para determinar la cantidad de agua presente en la muestra y se basa en la pérdida de peso de dicha muestra por calentamiento durante 4 horas a 110 ºC en estufa de laboratorio. La densidad ha sido determinada con el picnómetro de Le Chatelier, la determinación de la superficie especifica se ha realizado por el método de Blaine, siguiendo la norma UNE-EN196-6:2010 y la caracterización morfológica, según la norma UNE-EN 12620.
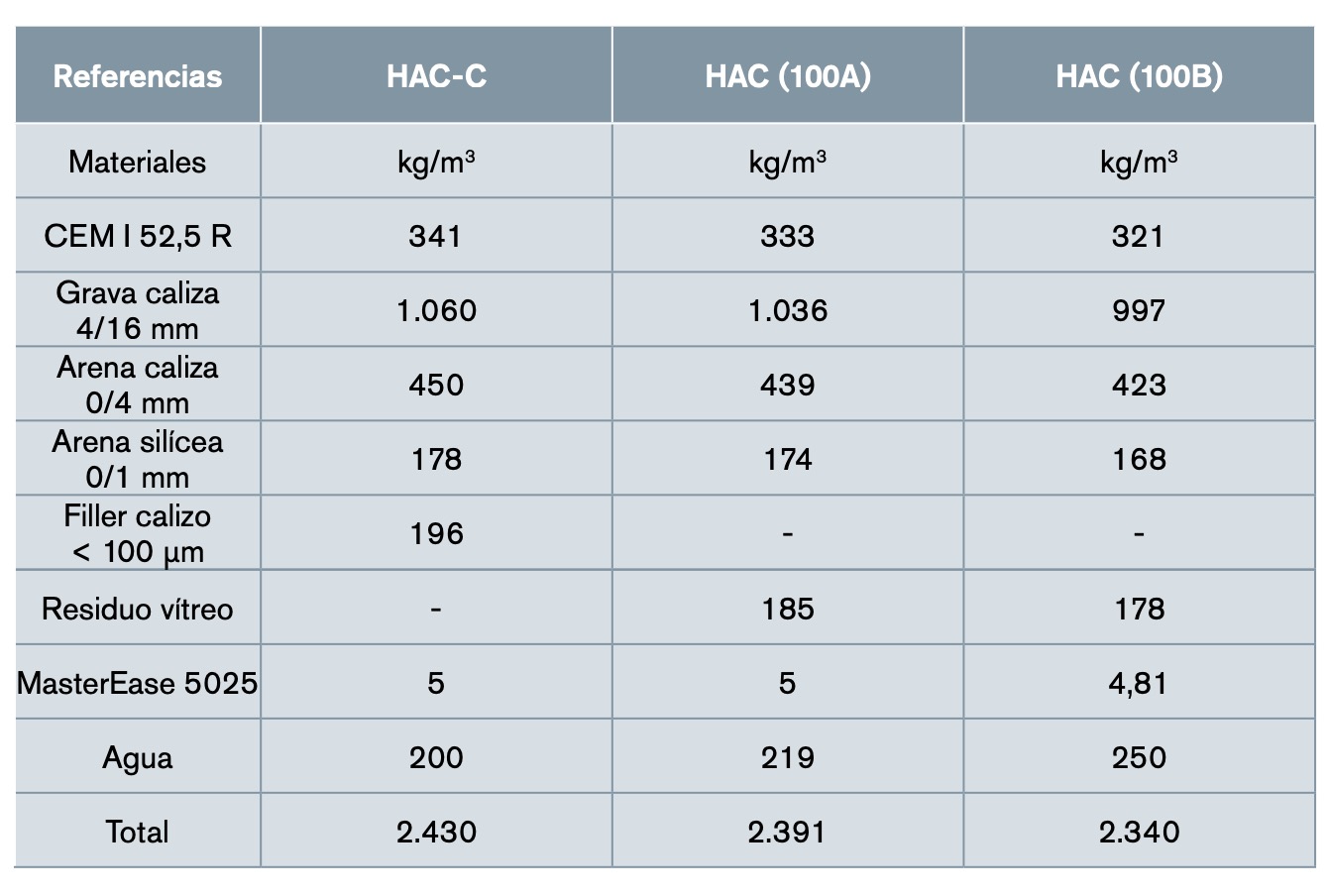
En estas determinaciones se han comparado los resultados con los obtenidos sobre un filler calizo (carbonato cálcico 100 %, finamente pulverizado cuyas partículas son < 100 µm) (tabla 2).
Para la determinación de la frita existente en el residuo vítreo, se parte de tres formulaciones básicas de esmalte representadas en tabla 3.
Como se puede observar en tabla 3, en las formulaciones empleadas solo se han tenido en cuenta los sólidos que entran en la molienda y que dan origen a los residuos vítreos investigados. Con estos datos se pueden calcular los gramos de frita existente por cada kilogramo de esmalte seco: 300 × 1.000 / 343,1 = 874,38.
La cantidad de frita existente en el residuo vítreo varía con relación al dato obtenido en seco, ya que se debe tener en cuenta la humedad del residuo (2,74%):
343,1 × 1,0274 = 352,50 g g(frita) / kg de residuo vítreo = 300 × 1000 / 352,5 = 851,06.
El análisis morfológico (granulométrico) del residuo vítreo se hace comparándolo con el filler calizo. En la tabla 4 se expresan los resultados.
Tras la caracterización del residuo, se pueden extraer las siguientes conclusiones:
•La caracterización química indica que el residuo es muy homogéneo.
•La densidad es muy parecida a un filler calizo y semejante a otros áridos empleados hormigones: arena de sílice, arena caliza, grava y gravilla caliza.
•El residuo tiene una elevada concentración de frita, es decir, de componente vítreo.
•El residuo tiene una morfología muy fina debido al proceso de molienda, en torno a 50 µm, como lo corrobora el análisis morfológico y la superficie específica que es el 44,7 % superior al filler calizo.
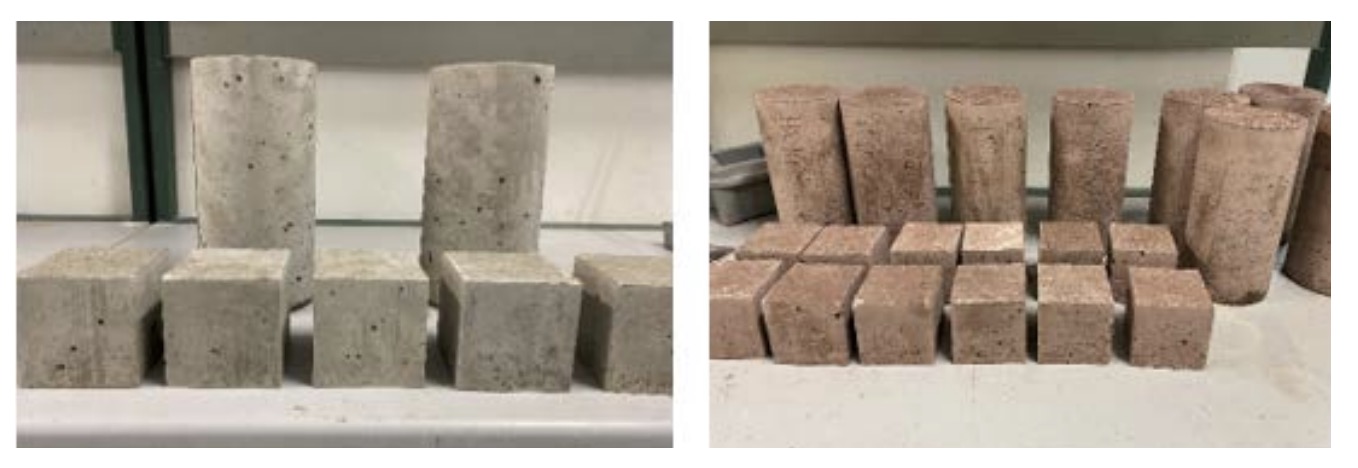
5. Metodología experimental
5.1. Dosificaciones de hormigones autocompactantes
El HAC es un hormigón fluido que tiene la capacidad de rellenar perfectamente los encofrados por la acción de su propio peso y compactarse sin la necesidad de aplicación de energía externa, fácil colocación por gravedad o bombeo, gran capacidad de relleno de moldes, sobre todo en geometrías complicadas.
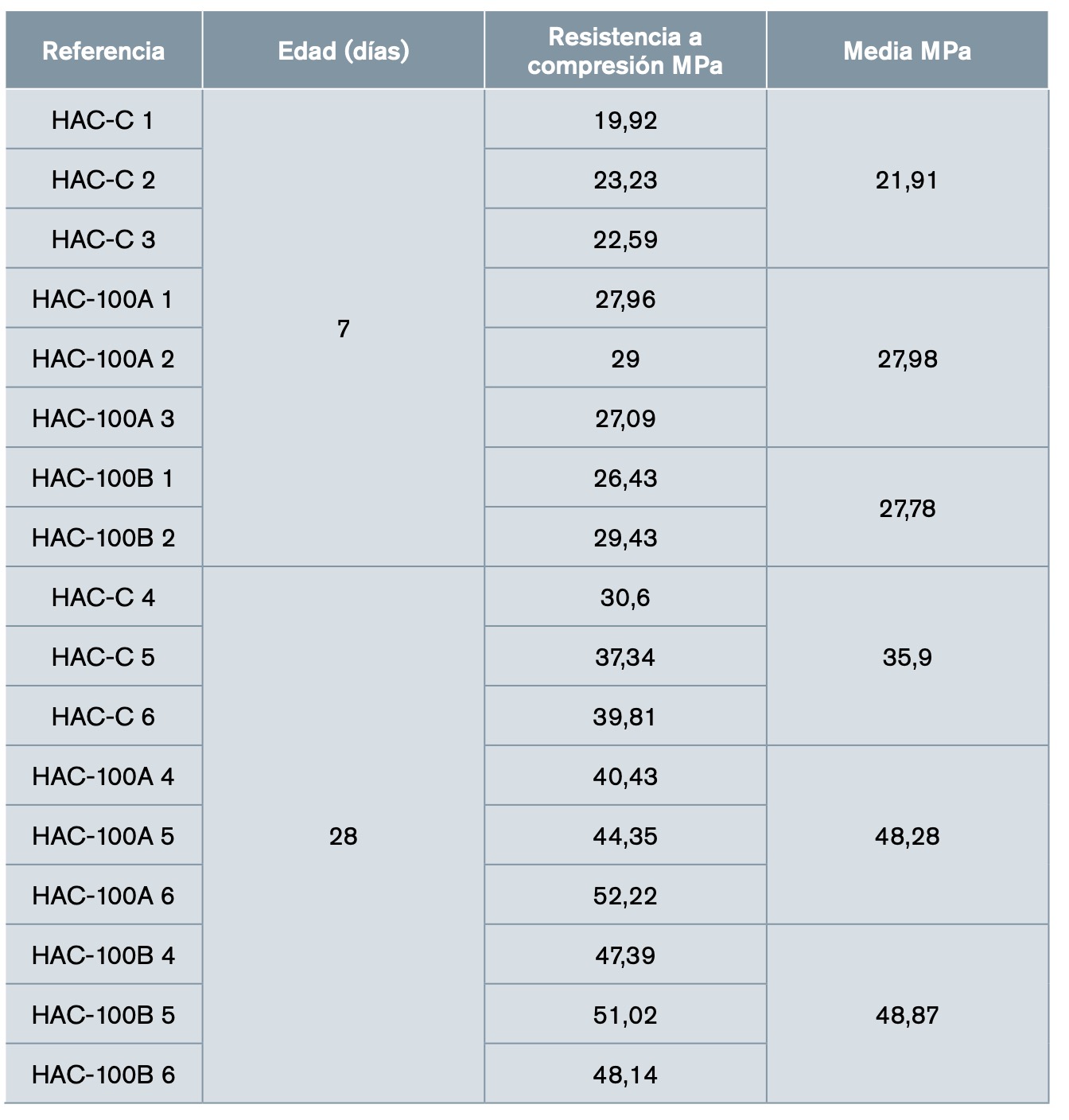
En general, un HAC se diferencia de un hormigón convencional por tener menor contenido de árido grueso, menor tamaño de árido y mayor volumen de finos y aditivos plastificantes. Las dosificaciones empleadas han sido varias hasta ajustar parámetros en estado fresco, siempre comparando el HAC-C con HAC con residuos vítreos. En la tabla 5 se indican las dosificaciones empleadas en las cuales se ha reemplazado la totalidad del filler calizo y parte de los áridos finos en los HAC100A y HAC100B con respecto a la dosificación del HAC-C.
Para la realización de las amasadas se sigue el siguiente orden al adicionar los materiales:
Primero los áridos, comenzando por el de mayor granulometría y siguiendo en orden descendente hasta homogeneizar bien. Seguidamente, se introducen las adiciones, el filler calizo, el residuo vítreo y el cemento. A continuación, el agua a la cual le hemos añadido el MasterEase 5025. Se sigue amasando durante 5 minutos hasta que la mezcla esté bien homogeneizada. Realizadas las amasadas, se procede a su caracterización en húmedo según la norma UNE-EN 12350.
Una vez realizados dichos ensayos, se procede a fabricar probetas cúbicas de 100 mm de arista y cilíndricas normalizadas de 300 mm de altura y 150 mm de diámetro de base. Las probetas son desmoldeadas a las 24 horas y se conservan en cámara de humedad en condiciones de curado controladas de 20 ± 2 °C y con el 99% de humedad relativa, hasta su utilización a los 7 y 28 días. En figura 1 se muestran probetas recién desmoldeadas.
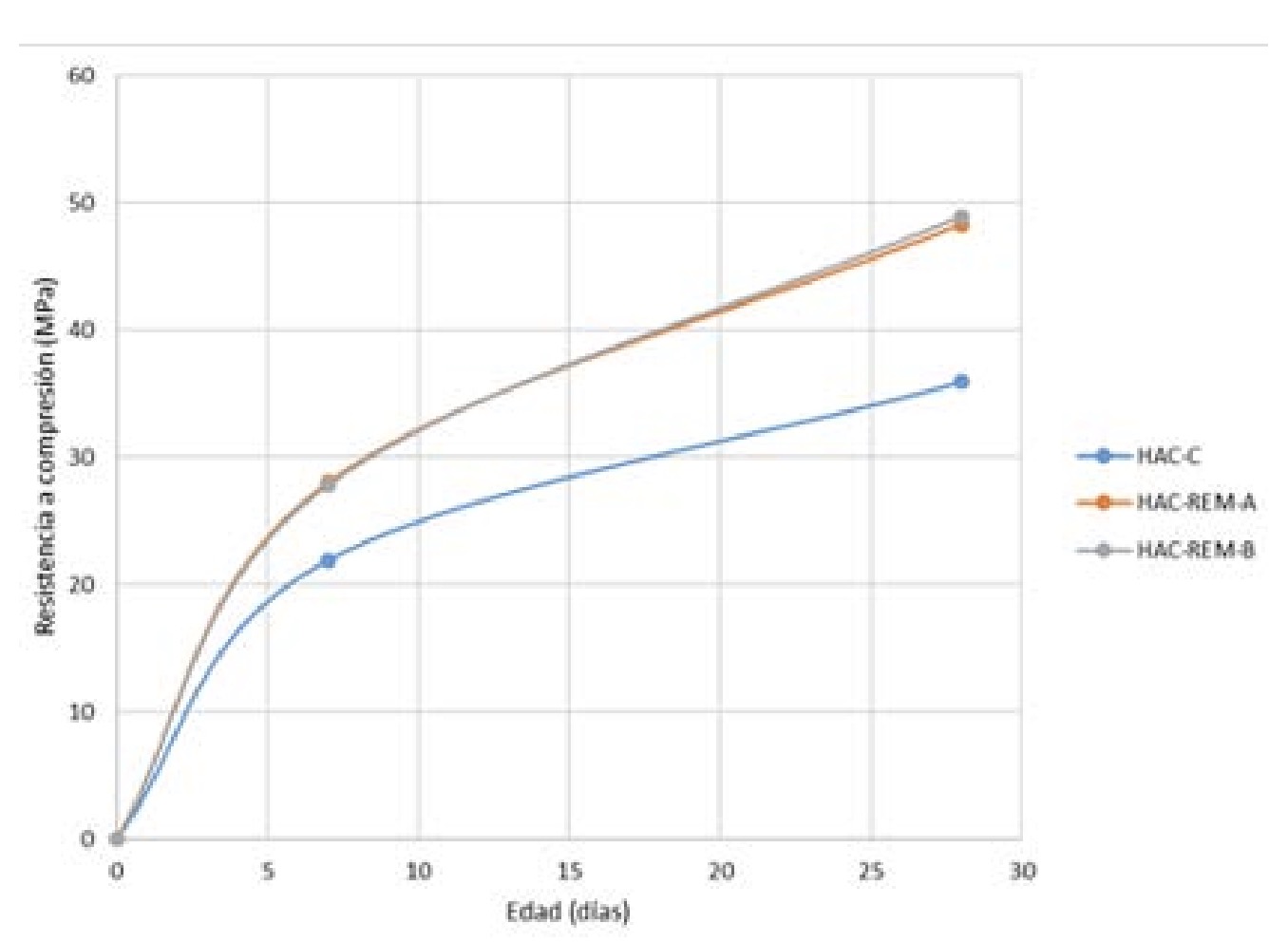
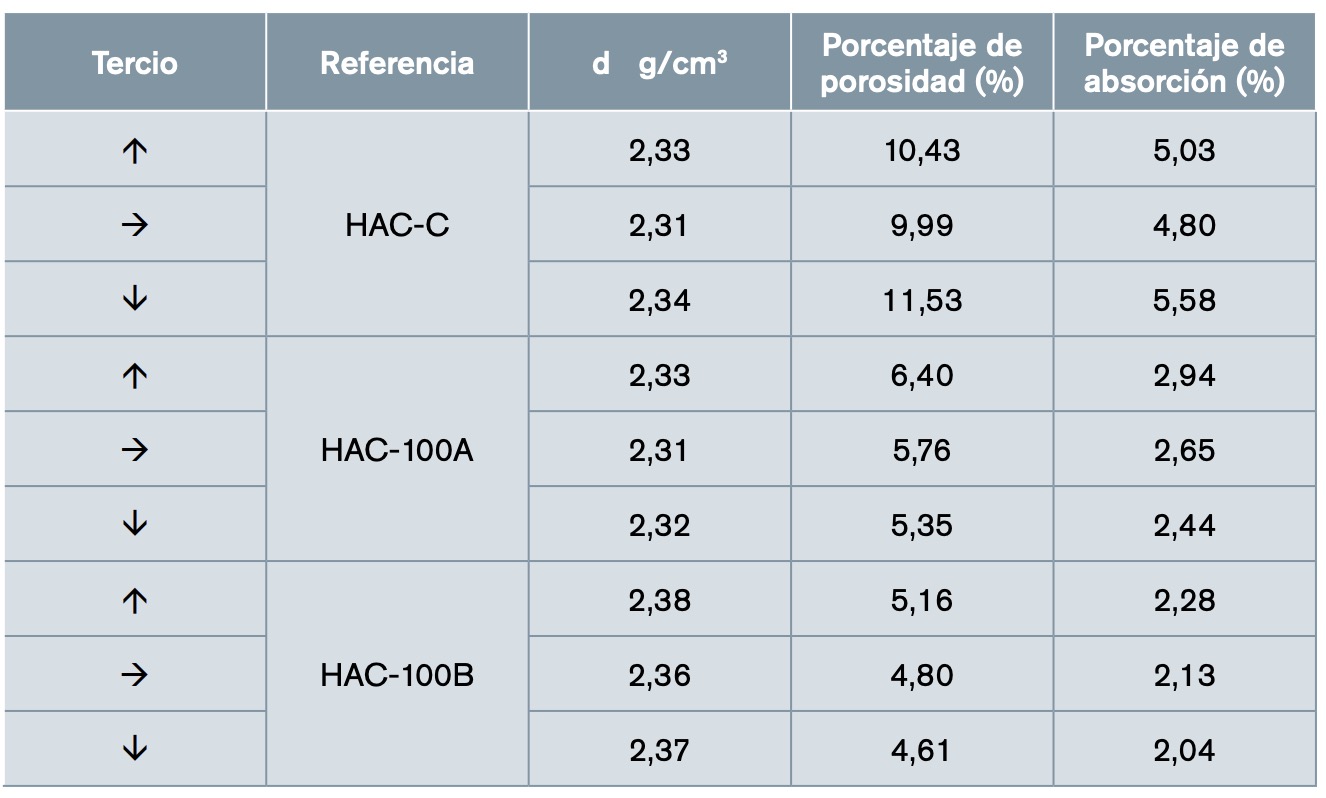
5.2. Ensayos realizados sobre los HAC fabricados
Se realizan ensayos tanto en estado fresco como en estado endurecido.
•Ensayos en estado fresco. Son los ensayos denominados de caracterización y sirven para evaluar el estado de la masa de hormigón recién homogeneizada. Se realizan según la norma UNEEN 12350 y en ellos se caracterizan tres aspectos fundamentales: la capacidad de flujo, la capacidad de paso y su estabilidad. Los ensayos realizados son los siguientes:
» Ensayo de caja en L (norma UNE-EN 12350-10). Se evalúa la habilidad de paso del HAC a través de las armaduras y su estabilidad. » Ensayo de embudo en V (norma UNE-EN 12350-9). Se evalúa la viscosidad y la capacidad de relleno de los moldes por la propia acción de la gravedad y el peso.
» Ensayo de escurrimiento con cono de Abrams (norma UNE-EN 12350-8). Evalúa la capacidad de relleno del HAC en ausencia de obstáculos.
» Ensayo de escurrimiento con anillo japonés (norma UNEEN 12350-12). Evalúa la resistencia de paso del HAC a través de las barras de la armadura, en condiciones de flujo libre.
•Ensayos en estado endurecido. Se realizan ensayos atendiendo a sus propiedades físicas, mecánicas, de aspecto superficial y de durabilidad.
» Propiedades físicas. A los 28 días se realizan las determinaciones de densidad, porcentaje de porosidad y de absorción de las dosificaciones HAC-C, HAC100A y HAC100B. Estos ensayos se realizan sobre las probetas cilíndricas previamente cortadas en tres tercios con objeto de ver si los resultados son homogéneos en todos estos tercios.
» Propiedades mecánicas. Se realiza mediante la determinación de la resistencia de rotura a compresión uniaxial según la norma UNE-EN 12390-3:2009. Este ensayo se realiza sobre las tres referencias de HAC fabricados, con una vida de 7 y 28 días, sobre probetas cúbicas de 100 mm de arista en prensa hidráulica de 1500 kN de capacidad de carga, marca SUZPECAR.
» Aspecto superficial.
» Ensayos de durabilidad. Son realizados sobre probetas cilíndricas a los 28 días de vida, previamente cortadas en tres tercios. Se realizan los siguientes ensayos:
– Permeabilidad al oxígeno (norma UNE-EN 83966:2008). El ensayo se basa en la capacidad que tienen los gases para penetrar en el seno de un material y circular por su interior. Consiste en aplicar una presión constante con gas (oxígeno) sobre una de las caras de la probeta para, después de un tiempo suficiente para que el gas atraviese toda la muestra, alcanzar la cara opuesta y registrar el caudal del gas de salida.
- Ensayo de penetración de agua bajo presión (norma UNE-EN 12390-8:2009). Las probetas se mantienen durante 72 horas a la actuación de una columna de agua bajo una columna de aire a una presión de 5 bares. Trascurrido ese tiempo, las probetas se rompen por tracción indirecta y se mide la profundidad de penetración del agua en el seno del hormigón.
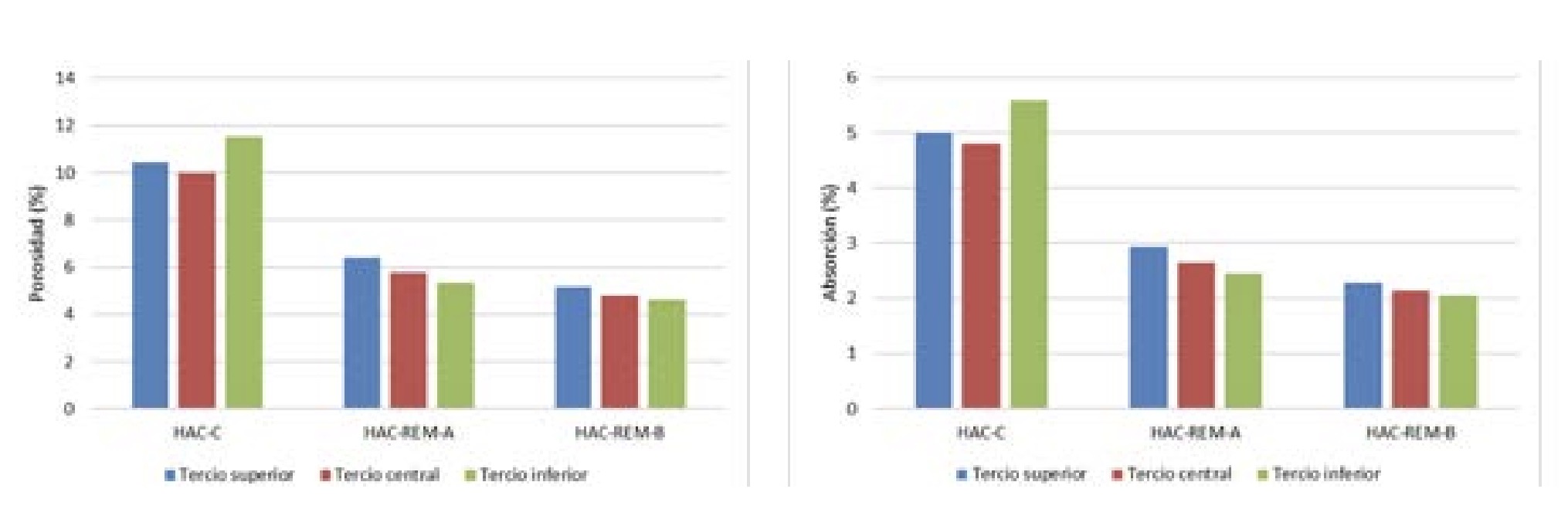
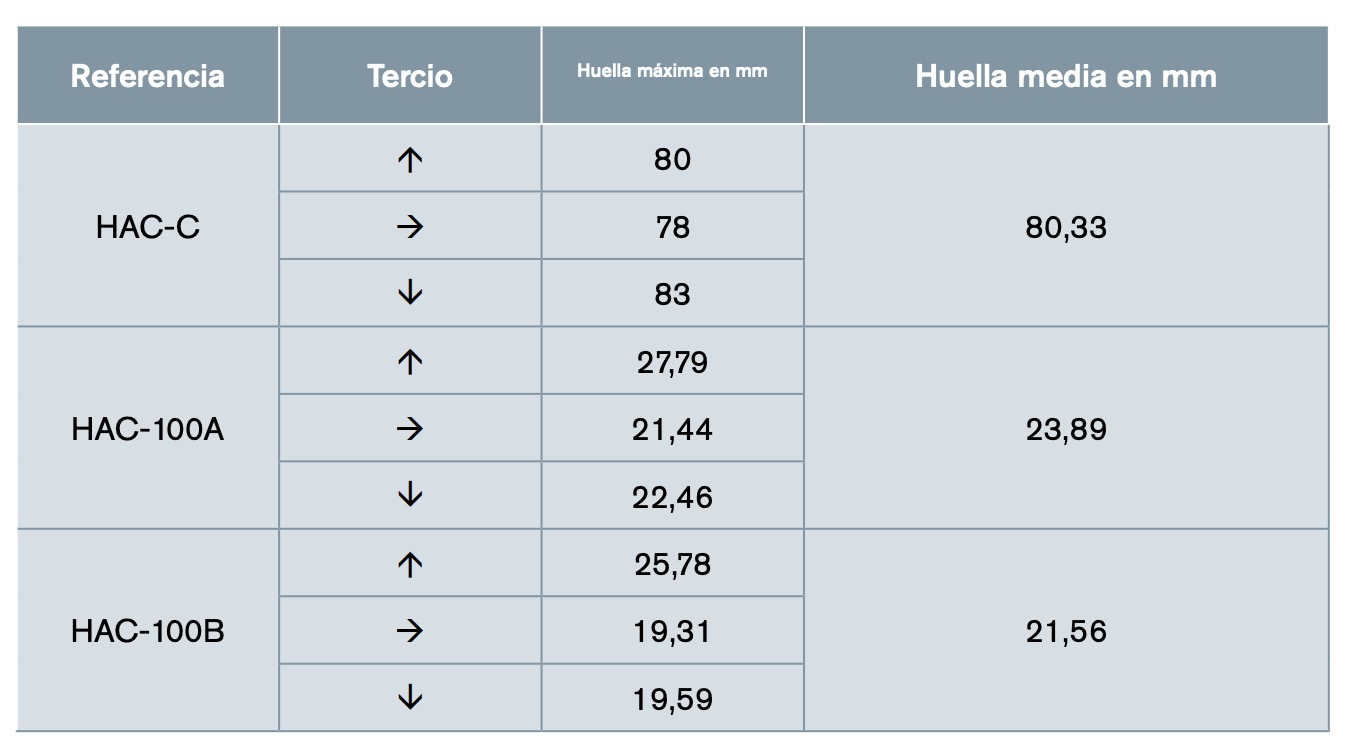
6. Resultados experimentales obtenidos
6.1. Ensayos mecánicos de rotura a compresión
A los 7 y 28 días de vida, se realizan los ensayos de rotura a compresión según la norma UNE-EN 12390-3 en prensa hidráulica.
Los resultados obtenidos en los ensayos han sido los siguientes según se indican en la tabla 6.
Según los datos obtenidos, se puede asegurar que las adiciones de residuo vítreo como reemplazo de filler y áridos finos mejora las prestaciones mecánicas tanto a los 7 como a los 28 días. A los 7 días, la mejora es del 31% con respecto al HAC-C y siendo muy similar la resistencia a la compresión de las referencias HAC-100A y HAC-100B; 27,98 y 27,78 MPa, respectivamente. A los 28 días, la mejora supone el 35% con respecto al hormigón de control, y los resultados permanecen muy parecidos a los obtenidos en las referencias HAC-100A y HAC-100B; 48,28 y 48,87 MPa, respectivamente.
Las mejoras obtenidas en las prestaciones mecánicas se deben a las características del residuo vítreo y, concretamente, a la cantidad de frita/kg de residuo (85%). La frita es la parte vítrea de un esmalte y se caracteriza por su naturaleza vítrea, su dureza y su elevada resistencia a la compresión. Por ello, este dato es muy importante para poder entender estos resultados.
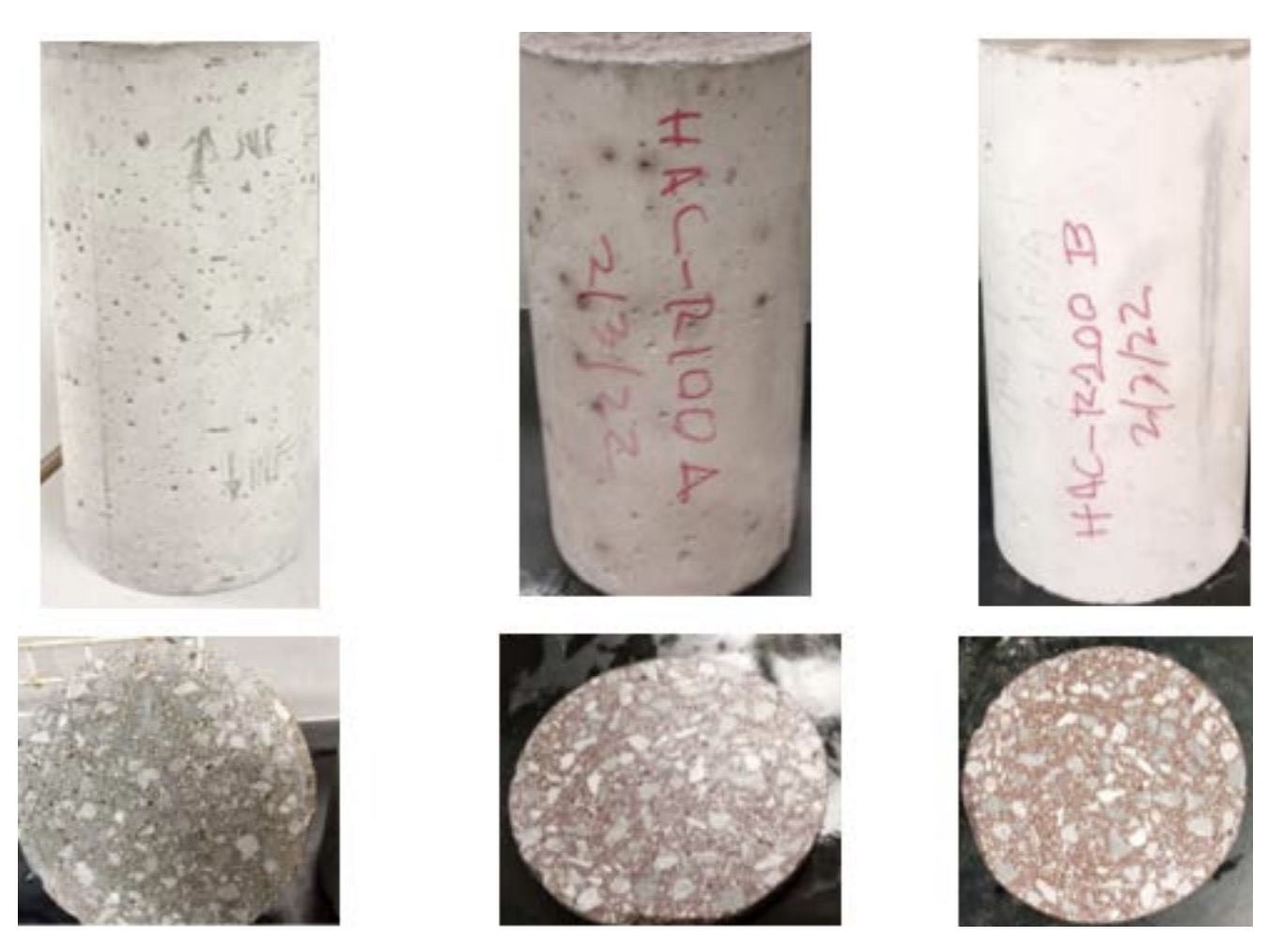
6.2. Resultados de ensayos físicos
En tabla 7 se recogen los resultados obtenidos de caracterización física de los hormigones fabricados HAC-C, HAC-100A y HAC-100B. Todos los ensayos se realizan en todos los tercios de cada una de las probetas para comprobar la homogeneidad de resultados de los hormigones fabricados.
Las densidades de las distintas referencias son bastante homogéneas en los diferentes tercios de cada referencia, lo cual indica que el hormigón de las distintas referencias es homogéneo.
La porosidad del HAC-C es del 10,65% de media y la del HAC-100A y HAC-100B tienen unos valores medios del 5,83% y del 4,85%, respectivamente, lo cual representa una disminución del porcentaje de porosidad del 83% y del 119% con relación con el HAC-C. Esta disminución, sin duda, se debe a que los hormigones con residuo vítreo tienen una porosidad accesible mucho menor como consecuencia de la propia naturaleza del residuo, el cual impide la penetración de aire en la estructura de los hormigones HAC-100A y HAC-100B. En figura 3 se representan gráficamente los resultados de porosidad.
Los resultados de porcentaje de absorción van en línea con los porcentajes de porosidad. En el HAC-C (5,13 de media) son semejantes a un hormigón convencional; sin embargo, en los HAC-100A y HAC-100B, la absorción es mucho menor, del 2,67% y del 2,15% de media, respectivamente, lo cual hace que el HAC-100A tenga un porcentaje de absorción del 92% menos y el HAC-100B el 138% menos con respecto al HAC-C. La naturaleza vítrea del residuo sigue mejorando las prestaciones ya que no permite absorber más agua frente al peso del hormigón. En figura 3 se presentan los resultados de los porcentajes de absorción.

6.3. Aspecto superficial
Se pueden destacar las siguientes cuestiones:
•Respecto al aspecto superficial del HAC-C, a pesar de ser bueno, se ven poros de burbujas de aire ocluido. Sin embargo, en los HAC-100A y HAC-100B, el nivel de poros va disminuyendo, y es menor en el HAC-100B.
•En los cortes transversales se observan homogéneamente repartidos los áridos gruesos, y no hay síntomas de segregación.
•También en los cortes transversales se observa la diferencia de color del HAC-C con respecto al HAC100A y HAC-100B. Estos últimos toman una coloración rojiza debido a que el residuo vítreo tiene esa coloración. En los cortes transversales de la figura 4 se observan estos cambios de color.
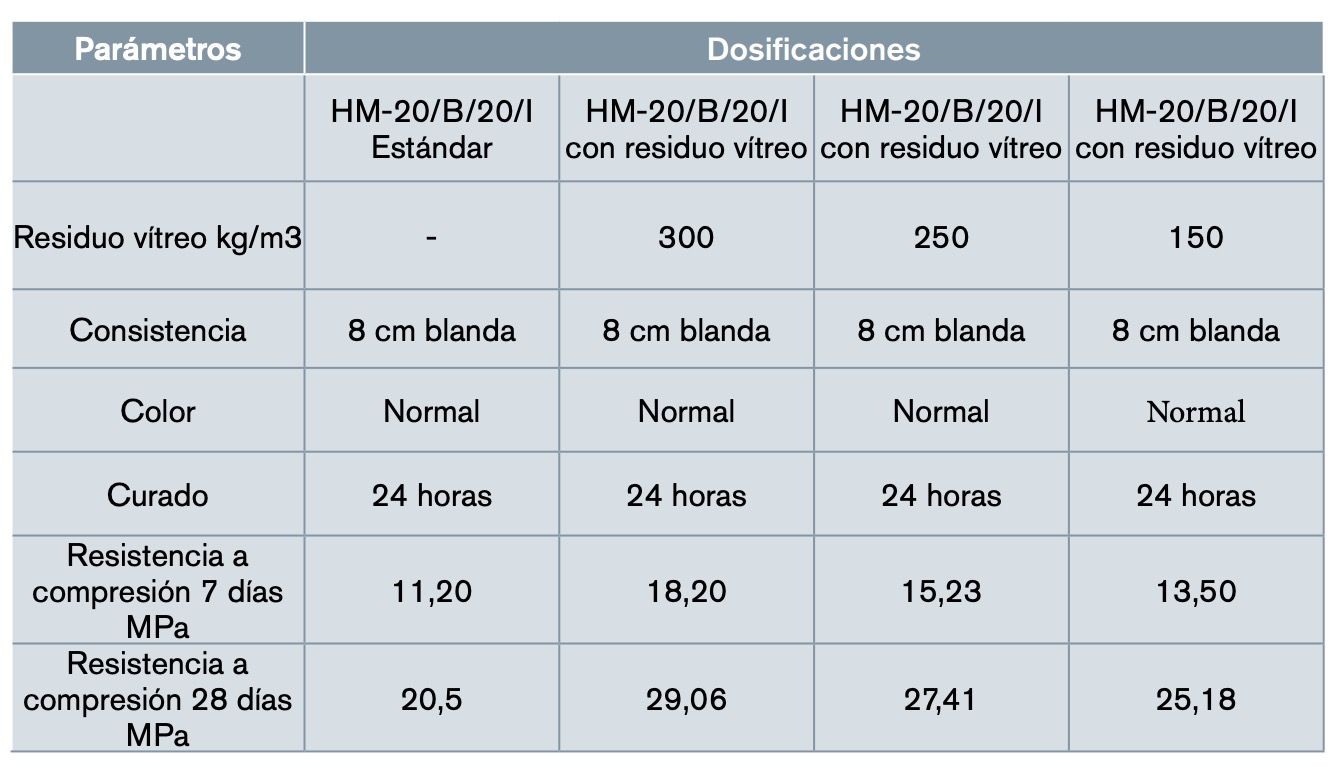
6.4. Resultados de ensayos de durabilidad
Se han realizado los ensayos de permeabilidad al oxígeno y penetración de agua bajo presión.
•Permeabilidad al oxígeno. Los resultados obtenidos indican que los HAC menos permeables corresponden a los que contienen residuo vítreo en su dosificación como reemplazo de los áridos finos y filler calizo. El HAC-100A y el HAC-100B tienen un índice de permeabilidad del orden de 10- 18m2 y el HAC-C tiene este índice de permeabilidad en 10-17m2, con lo cual su índice de permeabilidad es 10 veces mayor. Por eso, los HAC-100A y HAC-100B son hormigones de baja permeabilidad.
•Penetración de agua bajo presión. En la tabla 8 se indican los resultados obtenidos. A la vista de los resultados, el hormigón menos permeable es el HAC-C (no tiene residuo vítreo), mientras que los más permeables son, por este orden, el HAC100B y el HAC-100ª, con una gran disminución de la permeabilidad sin duda originada por las adiciones de residuo vítreo como reemplazos de filler calizo y áridos finos.
Ambos hormigones se pueden catalogar como impermeables, pues el valor máximo de penetración de agua bajo presión exigido a un hormigón estructural es de 50 mm y la media de estas dos referencias es de 23,89 mm y 21,56 mm. Esto permite su exposición incluso a ambientes agresivos. En la figura 5 se observa esta diferencia de penetración de agua bajo presión en las tres referencias investigadas.
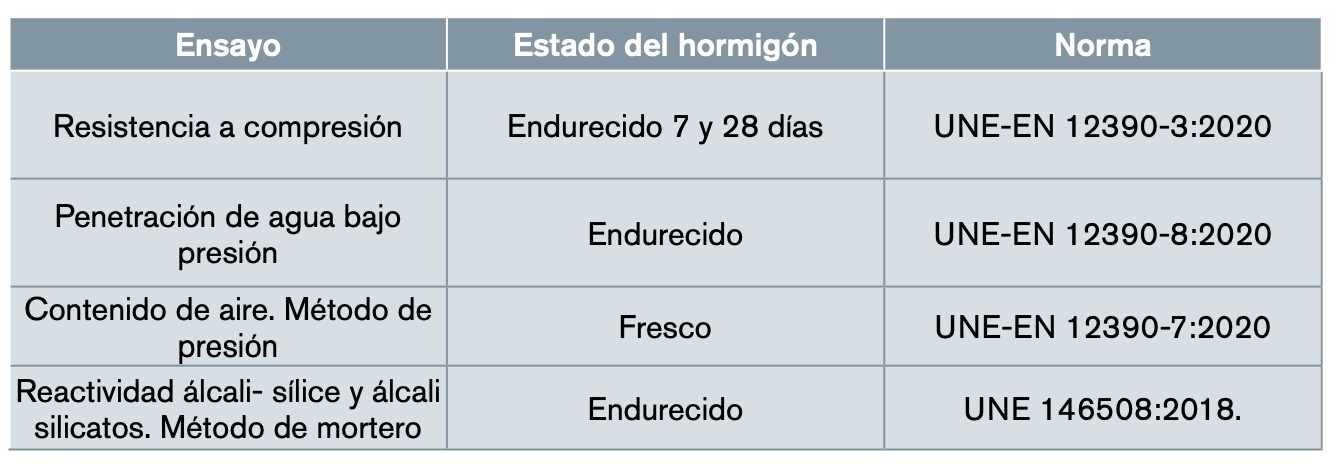
7. Conclusiones experimentales
Las conclusiones extraídas son:
•El acabado superficial es bueno y la distribución interna es homogénea y sin ningún signo de segregación.
•Las propiedades físicas, el porcentaje de porosidad y el porcentaje de absorción mejoran de forma sustancial en los hormigones autocompactantes con residuo vítreo en su composición, ya que se reducen estos parámetros el 83% y el 119%, respectivamente.
•Las propiedades mecánicas de resistencia a compresión, a los 7 y a los 28 días, mejoran en el 31% y el 38%, respectivamente, en los hormigones autocompactantes con residuo vítreo en su composición.
•Los ensayos de durabilidad indican que los hormigones autocompactantes con residuo vítreo son 10 veces menos permeables a los gases que el que no tiene residuo vítreo. Este residuo vítreo, a su vez, hace que en estos hormigones autocompactantes aumente la impermeabilidad, ya que la penetración de agua bajo presión es la mitad que un hormigón convencional.
•Como conclusión, se puede afirmar que la utilización de estos residuos vítreos en hormigones autocompactantes mejora, sin duda, las propiedades físicas, mecánicas y de durabilidad ensayadas.
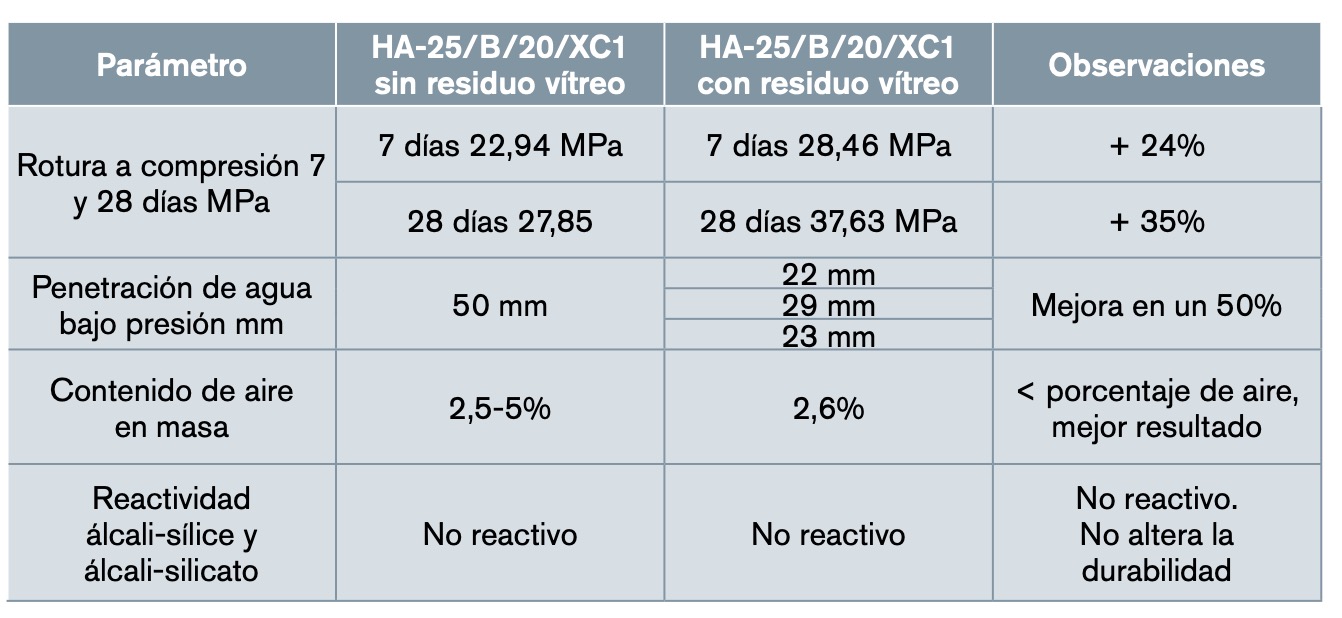
8. Implantación industrial de reutilización del residuo vítreo en la fabricación de hormigones
8.1. Objetivos de la implantación industrial
Los objetivos de la implantación industrial fijados son los siguientes:
•Comprobar industrialmente si los residuos vítreos originados en Vitrinor pueden ser reutilizados como aditivo de sustitución de filler calizo o áridos finos en la fabricación de hormigones.
•Convertir un residuo inútil en materia prima para la fabricación de hormigones, cerrando así el círculo de economía circular.
•Mejorar el deterioro ambiental, ya que el residuo vítreo estudiado es confinado en un vertedero controlado y con su reutilización se elimina esta cuestión.
•Convertir el residuo en recurso para lograr una reducción en la extracción de áridos. •Comprobar si los excelentes resultados obtenidos en la investigación se expresan también industrialmente, mejorando las características técnicas de los hormigones a fabricar.
8.2. Empresas necesarias para la realización de las pruebas industriales
Evidentemente para la realización de las pruebas industriales, son necesarios tanto el que origina el residuo industrial vítreo como el posible receptor de este, es decir, una empresa fabricante de hormigones y que esté en disposición de colaborar en las pruebas industriales.
Tras las conversaciones iniciales, todas las pruebas se hacen durante el año 2023 entre Vitrinor (generador del residuo) y Hormigones Santullán (fabricante de hormigones) y con la participación directa del autor de este artículo, a petición de las partes.
8.3. Planteamiento de las pruebas industriales a realizar
El planteamiento de las pruebas industriales a realizar incluye:
•Hacer diferentes dosificaciones con el residuo vítreo en amasadas de 3 toneladas.
•Probar en primer lugar con hormigones de masa con el residuo vítreo como reemplazo del árido fino, y comprobar la fluidez en estado fresco y la resistencia a compresión a los 7 y a los 28 días.
•Una vez vistos los resultados de los hormigones de masa, si estos son buenos, se ha de pasar a probar en hormigones estructurales, comprobando la fluidez en estado fresco y los ensayos de durabilidad exigidos en el CTE en estado endurecido, resistencia a compresión, profundidad de penetración de agua bajo presión, aire ocluido que sustituye a los ciclos hielo-deshielo y reactividad.
8.4. Pruebas industriales con hormigones de masa
Este tipo de hormigones se ponen en los suelos como base de otros hormigones estructurales. Para las pruebas industriales, se parte de las dosificaciones estándar en hormigones de masa utilizados por Hormigones Santullán tipo HM-20/ B/20/I. Esta nomenclatura quiere decir que es un hormigón de masa, con una resistencia a compresión a los 28 días de 20 MPa, consistencia blanda en cono de Abrams, con árido máximo de 20 mm y para ambiente de intemperie.
Evidentemente, las dosificaciones, por una cuestión de confidencialidad, no se pueden explicitar.
Se realizan tres tipos de dosificaciones con el residuo vítreo, cada una de 3 toneladas y todas ellas reemplazando el árido fino (0-2 mm) por el residuo vítreo en dosificaciones de 300, 250 y 150 kg/m3, manteniendo constantes las dosificaciones de otros áridos (0-5 mm y 20 mm), ligeras variaciones en la dosificación de cemento (CEM II/A-M (V-L) 42,5 R y en el agua. Las relaciones agua/cemento son de 0,62, 0,63 y 0,54 y la relación residuo vítreo/cemento, de 1,37, 1,15 y 0,68, respectivamente.
Las amasadas se realizan industrialmente y son vertidas en moldes para su curado. En la tabla 9, se indican los valores requeridos para un HM-20/B/20/I estándar y los valores obtenidos para las tres dosificaciones de HM-20/B/20/I fabricados con reemplazo de árido fino por residuo vítreo. A la vista de los resultados, se extraen las siguientes conclusiones:
•Los resultados de resistencia a compresión, a los 7 y a los 28 días, son mejores en las dosificaciones con residuo vítreo que en la estándar sin residuo vítreo.
•El incremento de resistencia a compresión es mayor en las dosificaciones con mayor cantidad de residuo, y varían del 41 % en la dosificación de 300 kg/m3 al 23% en la dosificación de 150 kg/m3.
•La relación residuo vítreo/cemento ha sido elevada; 1,37, 1,15 y 0,68, y en la parte experimental esta relación está cuantificada en 0,55.
•Rebajando esta relación a 0,55, el endurecimiento será más fiable y mejor, y se deja para posteriores pruebas industriales la dosificación de residuo vítreo en 100 kg/m3.
•Vistos estos resultados, el siguiente paso que se da será trabajar con hormigones estructurales.
8.5. Pruebas industriales con hormigones estructurales
El hormigón elegido para estas pruebas industriales es un hormigón armado HA-25/B/20/XC1. Se trata de un hormigón estructural de 25 MPa de resistencia mínima a compresión, consistencia blanda en cono de Abrams, y el árido de mayor granulometría es de 20 mm.
Las dosificaciones por temas de confidencialidad no se exponen, pero la dosificación del residuo vítreo es de 100 kg/m3, sustituyendo como reemplazo parcialmente al árido de menor granulometría (arena 0-2mm). En la dosificación se mantienen los áridos de 0-5 mm, 10 mm y20 mm. El cemento utilizado es CEM II /A-M (V-L) 42,5 R y la relación agua/cemento es de 0,52.
La amasada se realiza en hormigonera industrial y se descarga en moldes para hacer los dados que fraguaran a la vez que se fabrican las probetas cúbicas y cilíndricas para los diferentes ensayos de durabilidad a realizar. En estado fresco se comprueba el escurrimiento con cono de Abrams, obteniendo un escurrimiento de 10 cm, por lo tanto, tipo B (blando).
La durabilidad del hormigón es una forma de ver a futuro si los hormigones fabricados con residuo vítreo pueden tener alguna problemática técnica a posteriori. La realización de estos ensayos se hace en un laboratorio independiente, un laboratorio geotécnico homologado, y los ensayos prescritos por el CTE son los que se exponen en tabla 10 junto a sus normas.
El ensayo de aire ocluido sustituye los ciclos de hielo-deshielo y determina la cantidad de aire que puede contener el hormigón recién amasado (estado fresco) excluyendo el aire que puedan contener las partículas de los agregados. El resultado normal de este ensayo es de 2,5-5%. En este HA-25 con residuo vítreo el resultado es de 2,6%, lo que da idea de un hormigón muy compacto, sin duda debido a la adición del residuo vítreo, lo cual indica que al tener poco aire ocluido quedarán menos espacios para el hielo-deshielo.
El ensayo de reactividad álcalisílice y álcali-silicato tiene por objeto evaluar la reactividad potencial de los áridos, en este caso del residuo vítreo, a través de la exposición de probetas de mortero sumergidas en una disolución de hidróxido sódico (NaOH) a 80 °C de temperatura. Una reacción álcali-silicato se produce cuando interactúan áridos que contienen minerales potencialmente reactivos con los álcalis del cemento. Esta reactividad lleva consigo la formación de geles que en presencia de humedad se expanden, y ese hecho se manifiesta en agrietamientos, lo que supone una reducción drástica de la durabilidad. Para este ensayo se parte de tres dosificaciones: una sin residuo vítreo y dos con el residuo en diferentes dosificaciones. Los resultados certifican que el residuo vítreo no presenta reactividad.
La resistencia a compresión es mayor en los HA-25 con residuo vítreo (37,63 MPa) frente a los 27,85 MPa del HA-25 sin residuo vítreo, lo que supone una mejora del 35 %.
La penetración de agua bajo presión también mejora con el residuo vítreo incorporado, ya que la profundidad de penetración es de 22 mm, 27 mm y 23 mm frente a una profundidad de penetración del HA25 sin residuo de 50 mm.
En tabla 11 se indican los resultados obtenidos con HA25/B/20/XC1 con residuo vítreo frente a los obtenidos con HA25/B/20/XC1 sin residuo vítreo en su composición.
9. Conclusiones definitivas
A la vista de los resultados obtenidos tanto en fase experimental como industrial, las conclusiones son las siguientes:
•El residuo vítreo es totalmente apto para su utilización como reemplazo total o parcial tanto de filler calizo como de áridos finos.
•Su utilización mejora las características técnicas de hormigones autocompactantes, de masa y estructurales. •Estas mejoras consisten en una menor porosidad y absorción, mayor resistencia a compresión, menor penetración de agua bajo presión, menor contenido de aire ocluido en masa y su nula reactividad.
•Actualmente se está empezando a utilizar el residuo en la fabricación de hormigones, y hasta el momento se han reutilizado 40 toneladas.
•Una vez acabadas las pruebas industriales, y previa solicitud, ha sido concedida la patente bajo la forma de modelo de utilidad ES 1305851 en todo el territorio nacional durante 10 años.
•El objetivo final cumplido es que un residuo inútil se ha conseguido valorizar y se ha cerrado el ciclo de economía circular.
Agradecimientos
A la Universidad de Cantabria, y concretamente a LADICIM, por poner a disposición del autor de este artículo sus laboratorios y personal para la realización de las investigaciones.
Al profesor Carlos Thomas García por dirigir la tesis del Programa Sénior del autor de este artículo.
A las empresas Vitrinor y Hormigones Santullán por su involucración y convicción de que la innovación y la sostenibilidad son una oportunidad de negocio y de mejora.
Bibliografía
Gómez Gómez, Eugenio (2022). Tesis Programa Sénior. “Reciclado y valorización de residuos vítreos procedentes del esmaltado de acero vitrificado en materiales de construcción. Morteros y hormigones”.
Gómez Gómez, Eugenio (2023). “Memoria de la aplicación industrial de residuo vítreo en hormigones de masa y estructurales”.
Sosa Yépez, Israel (2017). Tesis doctoral. “Incorporación de escorias siderúrgicas en hormigones autocompactantes de altas prestaciones”.