Manuel Gómez-Franqueira Álvarez
Presidente de Grupo Coren
La I+D+i es una de nuestras prioridades, que nos ha permitido ir por delante del sector
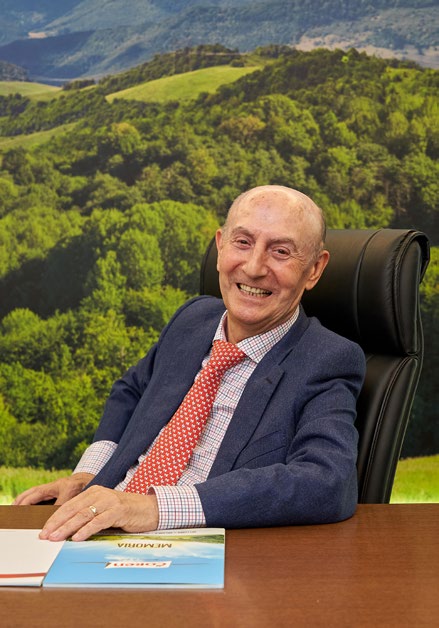
Coren es la principal cooperativa agroalimentaria cárnica de España, con una trayectoria de más de 60 años dedicada a la producción de avicultura, porcino, vacuno y cunicultura. Actualmente, la cooperativa cuenta con 7.000 familias entre socios y trabajadores, tiene una red de 23 industrias en toda Galicia y supera los 1.500 millones de euros de facturación. Manuel Gómez-Franqueira Álvarez, ingeniero técnico industrial por la Escuela de Ingeniería de Vigo, está al frente de la cooperativa desde 1986, primero como consejero delegado, y desde 2011 también como presidente.
¿Cuál es el origen de Coren?
El nacimiento de Coren se remonta a finales de los años 50, cuando los avances en vacunación contra la gripe aviar permitieron la cría de aves en grandes grupos, que hasta entonces no era posible, y los americanos impulsaron el desarrollo de la avicultura orientada al mercado. Para su expansión, en España contactaban con los gerentes de las Uteco provinciales. En 1959, Don Eulogio Gómez Franqueira, maestro de escuela en Castrelo de Miño, fue nombrado gerente de Uteco Orense, y una empresa americana, llamada Swift, contactó con él para proponerle el plan de crear aquí las primeras 20 granjas de 5.000 pollitos.
En aquella Galicia marcada por la extrema pobreza del ámbito rural y la emigración, Don Eulogio Gómez Franqueira creyó que era posible vivir dignamente del campo y puso en marcha aquel proyecto. La primera cooperativa nació el 30 de abril de 1962, fundada por mi padre junto a 20 socios, a los que logró convencer de este proyecto después de muchas dificultades, ya que les parecía utópico. De hecho, muchos de estos primeros socios eran también maestros de escuela como él, con cierta formación para ver las posibilidades de aquella iniciativa.
Mi primer gran desafío fue la entrada en la Comunidad Europea, y cuando llegó el momento supimos afrontar las dificultades para competir con Europa y vender también allí
Durante los tres primeros años, los americanos de la Swift suministraban los pollitos de un día y el pienso. Pero después los socios de Uteco decidieron desvincularse y organizar la cooperativa con recursos propios, por lo que promueven el matadero avícola de Santa Cruz de Arrabaldo y la fábrica de piensos de O Vinteún. La iniciativa fue un éxito y pronto surgieron nuevas granjas e industrias.
Después del desarrollo de la producción avícola tanto de carne como de huevo en los años 60, a lo largo de los 70 se fue incorporando el porcino -en 1979 adquirimos la planta de Industrias Frigoríficas del Louro Frigolouro en Porriño-, y luego llegaría el vacuno, tras la adquisición de Novafrigsa en 1990.
¿Y cuándo se incorpora usted?
Eulogio Gómez Franqueira se mantuvo al frente hasta 1984, pero yo ya estaba en la cooperativa desde años antes. Ya desde niño, acompañaba a mi padre en las reuniones de Uteco. Recién salido de la Facultad de Ingeniería, creé mi propia explotación ganadera de conejos y matadero frigorífico, así como una planta hortofrutícola, que llegarían a ser las más grandes de España en la época. En Coren, comencé desde abajo para conocer las diversas áreas de la empresa: Producción Avícola, Dirección Comercial, Coordinación de Industrias, Dirección de Industrias y la Subdirección General, hasta ser nombrado director general de Coren en la asamblea de 1986.
Mi primer gran desafío fue la entrada en la Comunidad Europea, una división en la que no estábamos al nivel de nuestros competidores. Sin embargo, desde la cooperativa ya nos habíamos preparado y, cuando llegó el momento, supimos afrontar las dificultades para competir con Europa y también vender allí. Siempre nos ha orientado la premisa de adaptarnos al mercado, y tanto nuestros cooperativistas como equipo de dirección han tenido claro que era fundamental para el futuro de la cooperativa.
En esta línea, hemos sido pioneros en iniciativas como la cría de pollo campero y huevo campero, o la recuperación de la castaña en la alimentación de los cerdos. Desde nuestros orígenes, trabajamos siempre con el compromiso de ofrecer productos de la máxima calidad. Y seguiremos en esta línea, asumiendo nuevos proyectos sin renunciar a nuestros valores: respeto al medio ambiente, bienestar animal, innovación y máxima calidad alimentaria.
¿En qué magnitudes se mueve actualmente la cooperativa en cuanto a producción e industrialización?
Hemos cerrado 2023 con una facturación por encima de los 1.500 millones de euros. Tenemos 4.000 socios entre directos e integrados y el volumen de empleo ronda ya los 3.300 trabajadores. Nuestra producción anual asciende a más de 100 millones de kilos de pollo, 26 millones de kilos de pavo, 65 millones de kilos de porcino y 5 millones de kilos de vacuno.
En cuanto a industrialización, contamos con 23 plantas por toda Galicia, entre las que destaca nuestro Centro de Procesado Avícola de Santa Cruz de Arrabaldo, que ha sido estratégico para posicionar a Coren como líder en distribución avícola. Esta industria, con una inversión acumulada desde sus inicios hasta hoy de más de 250 millones de euros, es un modelo en tecnología y seguridad alimentaria en la UE, que ha permitido dar respuesta a las necesidades del mercado y a la demanda de cada cliente, y en la que se producen más de 1.700 referencias avícolas.
Junto a él, los otros dos referentes son el Centro de Procesado de Porcino Frigolouro (en Porriño) y el Centro de Procesado de Vacuno de Novafrigsa (Lugo). Anexo a este último se encuentran nuestros secaderos de jamones, una moderna planta con capacidad para 700.000 piezas. A ello se suman cinco plantas de pienso, el Centro Tecnológico de Incubación de Pollitos, ubicado en el Parque Tecnológico de Galicia, o el único Centro de Incubación de Pavitos del noroeste peninsular, en Vilamarín. Todas ellas son instalaciones punteras, a la vanguardia del sector.
Una de esas innovaciones en las que fueron pioneros es la visión artificial en avicultura. ¿En qué consiste?
Desde 2016 contamos con un innovador sistema de visión artificial para determinar la calidad de las canales de pollo. Los sistemas anteriores se basaban en muestreos aleatorios de las partidas que conllevaba un componente subjetivo en la valoración por parte de los operarios, aparte de una extrapolación de resultados de un muestreo que podía ser sesgado y conducir a un resultado erróneo, con la repercusión económica que esto tiene.
La visión artificial permite un proceso muy preciso, rápido y objetivo para evaluar la calidad de las canales. Utiliza las últimas tecnologías de captura de imagen y procesamiento de datos, con un rendimiento excepcional a las velocidades de línea más altas (hasta 13.500 aves/hora). Consta de una cámara montada en la línea de procesado, iluminación led y un software de reconocimiento avanzado. Va tomando imágenes de todas las canales que pasan por la línea, utilizando la forma, el color y la textura para detectar la disminución de la calidad, con gran precisión. El software de reconocimiento procesa las imágenes recibidas desde la cámara y asigna una clasificación de calidad. Esta información se transfiere a los sistemas de control, para su análisis y determinar el destino de cada producto según su calidad. El uso de una cámara digital de alta gama y la iluminación led permite capturar imágenes más nítidas y detectar defectos con una precisión imposible hasta ahora. El sistema permite generar informes en tiempo real sobre el perfil de calidad de cada lote, gestionando con mayor eficacia.
Algunas iniciativas son el uso de gemelos digitales para la gestión de salas de despiece y plataformas digitales que aplican inteligencia artificial
¿Cuáles son las últimas innovaciones y nuevas tecnologías que aplica la empresa?
La I+D+i es una de nuestras prioridades, que nos ha permitido ir por delante del sector en muchos aspectos. Debido a que nuestra cooperativa abarca todo el ciclo productivo, son muchas las áreas de las que la aplicamos.
Por una parte, en nuestros centros de incubación incorporamos sensores para monitorear el desarrollo embrionario, optimizar el proceso de incubación y mejorar los resultados en uniformidad y calidad de la producción avícola. Así, una primera tecnología crea la temperatura de incubación óptima para el lote específico de huevos, imitando el proceso natural. Una segunda tecnología de eclosión simultanea brinda a los embriones los mismos estímulos que experimentaría en la naturaleza, generando el ambiente adecuado para que los polluelos nazcan simultáneamente, alcanzando una mayor incubabilidad y uniformidad.
Otra área es la fabricación de piensos compuestos para alimentación animal, en la que hemos implementado tecnologías avanzadas de higienización de piensos asegurando así la seguridad alimentaria y la calidad del producto final, con una tecnología específica de vapor, sumada a la implantación de sistemas de control de humedad y temperatura en todas las etapas de producción para prevenir la proliferación de microorganismos. También hemos implementado tecnología NIR (Espectroscopia de Infrarrojo Cercano), para realizar análisis rápidos y precisos de la composición nutricional de los piensos ya en el proceso de producción, permitiéndonos ajustar las formulaciones en tiempo real para cumplir los estándares de calidad. Asimismo, se han implementado sistemas de trazabilidad basados en blockchain para garantizar la seguridad alimentaria y la transparencia en toda la cadena de suministro.
Y también cabe destacar una tercera área, nuestros centros de procesado, con avances en diversas líneas. Por ejemplo, la implantación de almacenes caóticos en los que el sistema informático garantiza, a través de la gestión de las distintas cintas y robots, la trazabilidad individual de cada pieza que compone el lote de expedición. Otra iniciativa es el uso de gemelos digitales para la gestión de las salas de despiece, una herramienta digital que permite adecuar los pedidos de cada tipo de producto a la capacidad de la industria, o ayudas en gestión de sala para cada tipo de corte, buscando el modo más eficiente de trabajo de los recursos de maquinaria y personal. También se han puesto en marcha plataformas digitales que aplican inteligencia artificial para optimizar el consumo de energía, agua, vapor o aire comprimido en distintos procesos productivos según la franja horaria. Igualmente, los sistemas informáticos de planificación y programación permiten la trazabilidad, automatización y control para conocer datos de productividad, posibles averías y cadencias de las líneas. Y en oficinas, digitalizamos múltiples procesos para disminuir el uso del papel: firma digital de contratos y documentos, gestión automatizada de albaranes y facturas, gestión digital de certificados, firma digital de albaranes de entrega a clientes, e integración automática en los sistemas informáticos de gestión.
¿Qué medidas e iniciativas se está desarrollando en producción sostenible y economía circular?
Por nuestro compromiso de compatibilizar la actividad agroganadera con el máximo cuidado del entorno, tanto socios como empleados se implican con un modelo de trabajo responsable. Nuestro Plan de Sostenibilidad Ambiental se orienta a la modernización energética, la reducción de emisiones y la gestión eficiente de los recursos, en línea con la Agenda 2030 y el Acuerdo del Clima de París. Este tipo de acciones nos ha permitido reducir en los últimos cinco años las emisiones de CO2 en más de un 45%, un porcentaje muy superior a la media nacional.
Las granjas cuentan con los más modernos sistemas de gestión de residuos, entre ellos instalaciones de biomasa ganadera, inyectores de purines (para su depósito bajo el terreno con mínimo impacto en superficie) o un sistema de ultracentrifugación portátil que separa la fracción sólida y líquida para su reaprovechamiento como abono orgánico en agricultura. En todas las instalaciones se implantan los últimos sistemas de energía renovable y eficiencia energética. De hecho, las granjas cuentan con instalaciones de biomasa, sistemas de energía fotovoltaica e incluso geotérmica.
Nuestro equipo de I+D investiga nuevos sistemas de tratamiento y valorización de residuos, lo que nos ha llevado a poner en marcha plantas que se encuentran entre las más innovadoras del sector. Así, la Planta de Energía Renovable para el tratamiento de biomasa ganadera permite generar energía a partir de los residuos de las explotaciones avícolas, que se destina al funcionamiento del Centro de Procesado Avícola. Los gases generados en su combustión pasan por un complejo sistema de filtrado que garantiza cero emisiones a la atmósfera. Esta planta se ejecutó en dos fases (2016 y 2021) y evita la emisión de 8.500 toneladas de CO2/año. Otro ejemplo es la Planta de Biometanización para generar biogás valorizando los residuos orgánicos del Centro de Procesado Avícola mediante digestión anaeróbica, una fermentación llevada a cabo por bacterias anaeróbicas en ausencia de oxígeno, generando biogás, por una parte, y por otra, fertilizante orgánico rico en nutrientes como nitrógeno y fósforo, apto para agricultura. Este sistema evita la emisión de 5.500 toneladas de CO2 al año.
Mientras, en las industrias se han llevado a cabo acciones para sustituir los combustibles fósiles por gas natural y otras fuentes renovables. Igualmente, reducimos el consumo de agua y disponemos de las últimas tecnologías en depuración para devolver el agua utilizada al medio con óptimos parámetros de calidad (incluso mejores que cuando la recibimos). También impulsamos la reducción del uso de plástico en los envases y el empleo de materiales reciclados
¿Cuáles son los próximos proyectos y nuevos retos?
El proyecto principal es el de mejora y ampliación del proceso productivo y logístico del Centro de Procesado Avícola de Santa Cruz. Tenemos ya varias etapas de esta actuación, entre ellas el nuevo sistema de aturdido en atmósfera controlada para la mejora del bienestar de los animales; o la mejora del proyecto de valorización de residuos de lodos de depuradora, de modo que el biogás, lo transformaremos en biometano para inyectarlo a la red. Y una tercera mejora sería la valorización de digestato resultante, o bien a través del secado e incineración para producción de energía térmica, o como fuente de nutrientes adecuada para suelos de cultivos leñosos como la vid y el olivo. En posteriores etapas se acometerán las inversiones necesarias para comercializar nuevas gamas de productos.
En líneas generales seguiremos trabajando en los proyectos que tengan que ver con análisis de datos e IA, tanto tradicional como generativa. Además de esto, se van a realizar múltiples automatizaciones en las industrias, con implantación de sistemas autónomos y robots, especialmente en controles de calidad, clasificación, trazabilidad y eficiencia de los procesos.